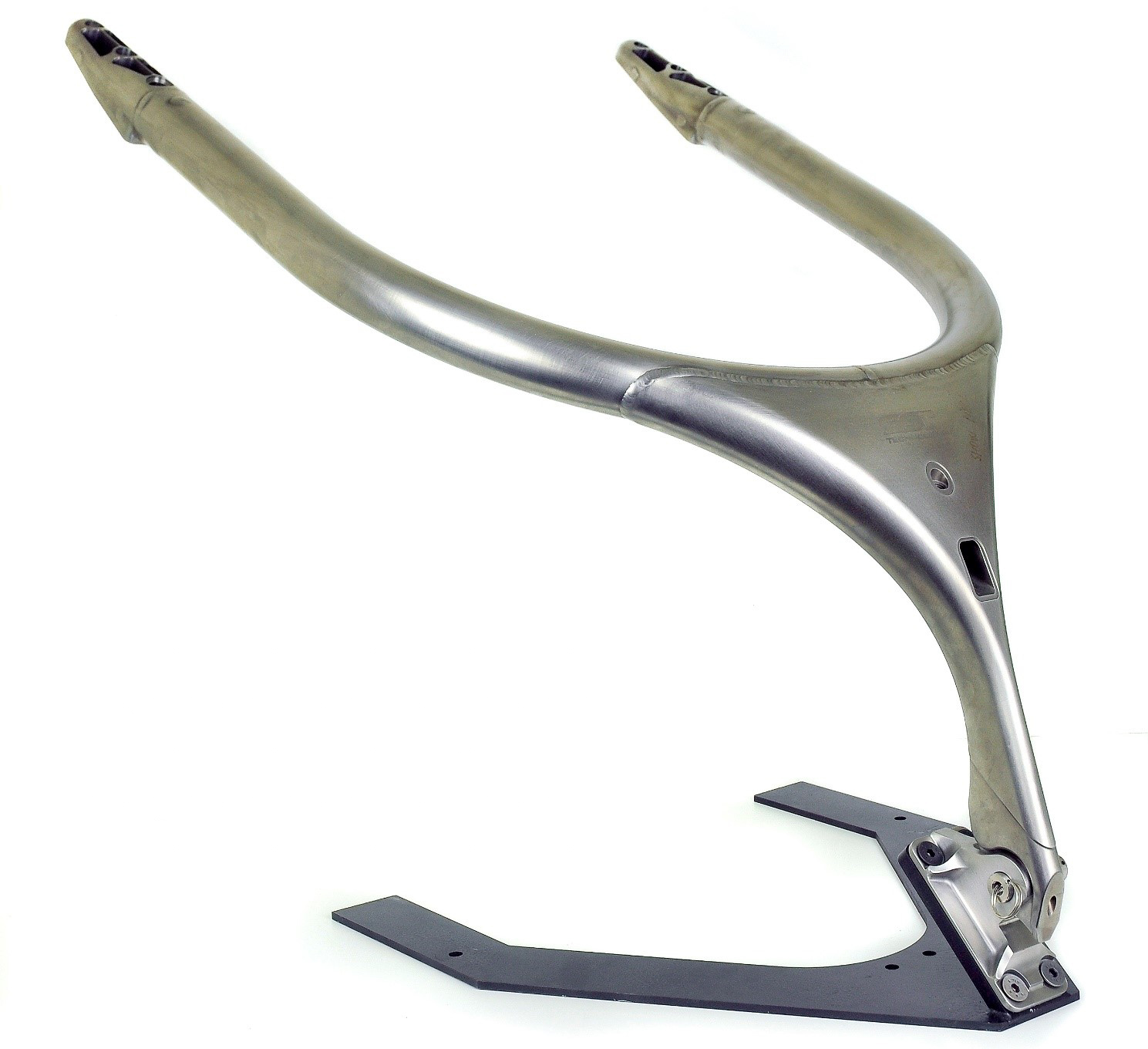
A Unison Breeze all-electric CNC tube bending machine has enabled Oxfordshire-based SST Technology to become the only British-based precision fabricator authorised to produce the life-saving Halo titanium driver protection system like that used in Formula 1. The machine has also equipped the business to complete numerous complex structural projects involving titanium tube.
The Unison Breeze 130mm ‘large diameter’ multi-stack tube bender was purchased to help SST produce high-performance optimal-flow exhaust systems for Formula 1, IndyCar and other motorsport sectors. With a pedigree in motorsport components and a powerful new tube bending machine to hand, SST’s thoughts quickly turned to driver safety. The exceptionally tight material control, production parameters and dimensional tolerances provided by the all-electric Unison Breeze tube bender, combined with SST’s experience in ultra-precise fabrications, led to the company’s Halo design securing FIA conformity for use in Formula 1, Formula 2 and Formula E motorsport and being adopted by several race teams. The design requires precision bending of 4 mm wall thickness titanium tube.
With low uniform elongation typically requiring a much greater bend radii than other metals, titanium doesn’t readily lend itself to being formed – a characteristic that makes creating tubular structures for aerospace and motorsport applications particularly challenging. For successful tube forming, the material must be compressed on the inside of the bend and stretched on the outside, while wall thinning and ovality of the tube have to be kept to very tight tolerances. Traditionally, ‘hot bending’ has been used to overcome the challenges of bending titanium but with support from Unison Ltd, SST developed a cold-bending process for their Halo design.
“Investing in the 130mm Unison Breeze machine has clearly paid dividends,” says SST Technology’s Group Business Development Director, Daniel Chilcott. “Tool changes are rapid, programming is incredibly user friendly, while the automatic setup ensures uncompromising levels of accuracy and repeatability. Sufficiently impressed with the capabilities of our 130mm machine, we have also purchased a smaller 65mm Breeze model for the production of more intricate pipework and parts for aerospace and gas turbine applications.”