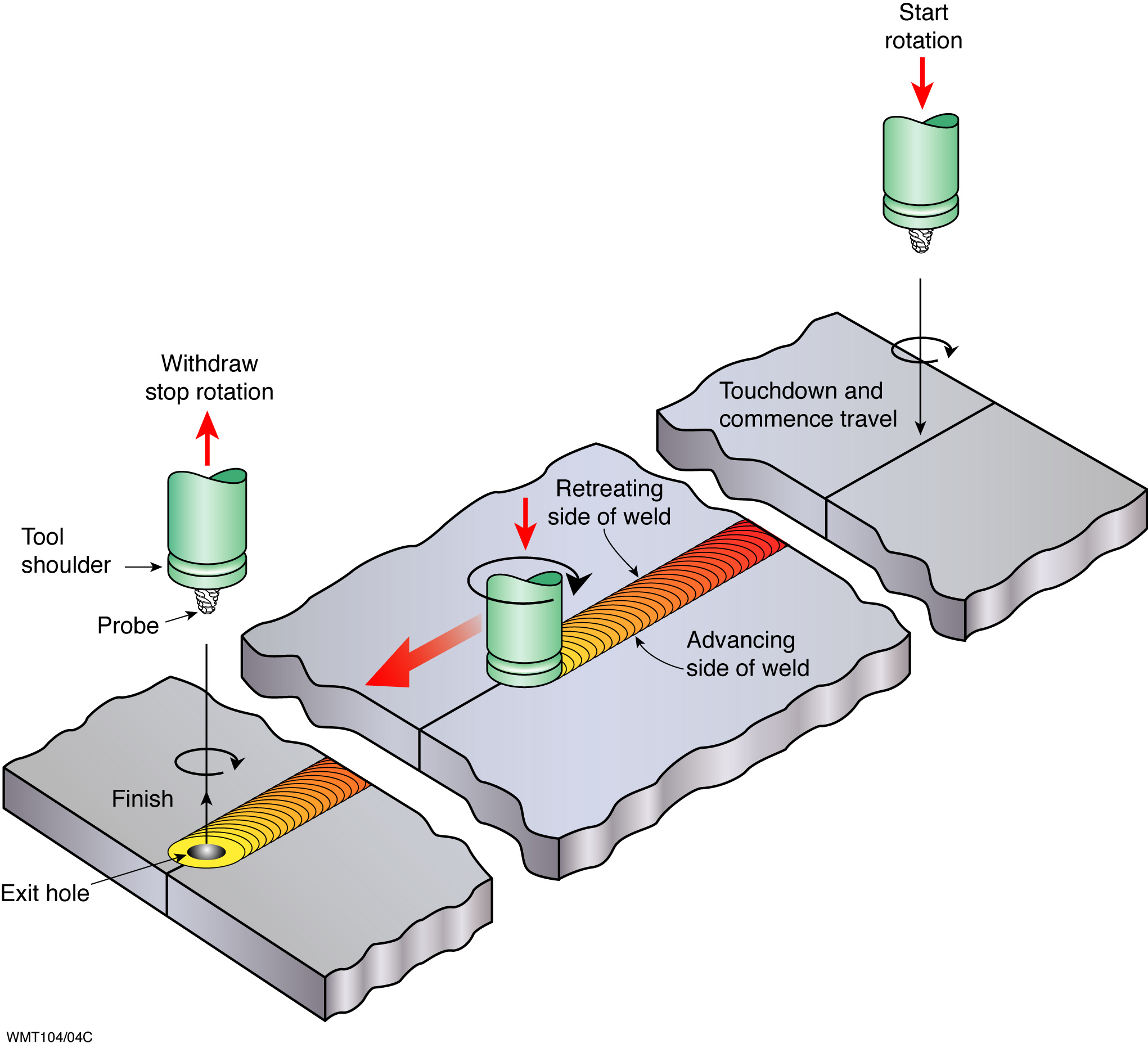
As an independent research and technology organisation, the TWI has recently completed an EU Clean Sky2 research project called ‘OASIS’. The key aim of this project was to develop autogenous welding processes to fabricate ‘rivetless’ welded aerospace structures. One of the technologies developed in this project was Refill Friction Stir Spot Welding (Refill FSSW), an aerospace-targeted manufacturing technology with the key industrial driver of replacing ‘mass-adding’ fastening joints. This supports aircraft weight reduction goals, improves the process of joining different materials and reduces defects. TWI Senior Project Leader, Dr Pedro Santos takes us through this innovative technology.
Refill FSSW is an autogenous solid-state welding process that was initially developed to replace riveted joints in large aluminium structures for the aerospace sector. The absence of a third element to produce a joint and the lower processing temperatures enable cost and weight savings per unit. It also avoids common solidification issues from fusion welding processes. Figure 1 below introduces the Refill FSSW equipment at the TWI and also shows the top surface of an overlap weld that has been performed with Refill FSSW on AA7075-T6, an alloy not weldable via fusion welding processes.
At the forefront of friction welding technology, TWI has been innovating welding research and development since the 1960s, providing everything from design advice through to troubleshooting, feasibility, application and prototype equipment development. The TWI is responsible for many key innovations in solid-phase joining, such as friction stir welding (FSW), invented at TWI in 1991. Another example is the development of linear friction welding for turbine blades.
FSW uses a non-consumable rotating tool designed to generate frictional heat to soften the adjoining metal to a point where it can be viscoplastically deformed and displaced around the tool (Figure 2). The FSW tool traverses the joint line between two parts, where its stirring action enables the formation of a solid-state weld. This has revolutionised welding of aluminium alloys due to the sub-melting point processing conditions that prevent solidification cracking and porosity formation. Furthermore, it reduces distortion, minimising the loss of parent material properties. The resulting joint has excellent tensile strength and fatigue and fracture properties.
Derived from FSW and using an identical tool, Friction Stir Spot Welding (FSSW) is a single spot joining process patented by Mazda. In FSSW, a non-consumable rotating tool is used to produce a localised joint without any linear movement across the workpiece. The process plunges a rotating tool through the upper sheet to a depth that allows interaction with the sheet underneath. The tool is dwelled for a set time to generate sufficient frictional heat and viscoplastic deformation around the tool probe. After the tool is extracted from the material, the sheet joint is completed. Figure 3 below shows the main steps of the FSSW process as well as the typical cross-section.
Unlike conventional single-point fusion techniques, FSSW produces no fumes or spatter, while offering a high energy efficient process. As a solid-state process, FSSW produces great quality joints, especially in materials that would suffer degradation when subjected to melting and subsequent solidification. FSSW has been used in large scale production, but limitations on materials and thicknesses are disadvantages. The inherent exit-hole feature also raises concerns over stress concentration at the centre of the joint, reduction of the effective joined area, localised fouling and corrosion.
To mitigate these issues, FSSW process variants were develop to minimise or eliminate the exit-hole. However, most variants either require a secondary operation, increasing weld cycle time or it produces a secondary exit-hole in a non-critical location. The invention of Refill Friction Stir Spot Welding has addressed many of these limitations.
Refill friction Stir Spot Welding
Refill friction stir spot welding (Refill FSSW) is the newest variant of the FSSW processes. Developed and patented by Helmholtz-Zentrum Hereon in 2004, the process uses a non-consumable tool with a concentric rotating probe and shoulder that are encompassed by an outer static clamp ring, as shown in Figure 4 on the next page.
In this process, the rotating components have vertical independent motion that refills the exit hole with the material displaced by the tool. The addition of an external static clamping ring enables the production of flush surface welds by preventing material losses in form of flash. This improves surface finish compared to FSSW, riveted or resistance spot-welded joints.
Process fundamentals
The refill FSSW process occurs over four stages in one continuous process, as shown in Figure 5 (see page 25). The tool components move to the surface of the top sheet to clamp the overlapped sheets, the rotating components remain at this stage for a set period to produce the frictional pre-heating.
The plunging stage then initiates with the shoulder and probe moving in opposite vertical direction to each other. Depending on the plunging tool component, the refill FSSW process can be performed either via shoulder-plunging or probe-plunging. The plunging component travels into the base material to a pre-defined depth while the retracting component moves to a pre-defined height, thereby maintaining a volume equilibrium and accommodating the displaced material. The contact between the plunging component and base material leads to further heat generation and material softening via interfacial frictional coupling and viscoplastic energy dissipation.
Once the plunging component reaches the pre-defined depth, the plunging and retracting components resume their original positions, returning to the top sheet surface, refilling the weld region with the displaced material. The extraction of the tool from the base material and unclamping the welded sheets concludes the welding cycle.
ADVANTAGES
The key industrial drivers for this technology are to replace mass-adding fastening processes, such as riveting, and to join a range of dissimilar materials, which are currently difficult to join using fusion welding processes. Compared to other mainstream single-point joining or mechanical fastening processes, Refill FSSW avoids many of the defects commonly associated with fusion welding of lightweight metals (e.g. porosity formation and solidification cracking). The lower processing temperatures below melting also offers advantages when controlling shrinkage and distortion, which is critical on large assemblies with multiple spot welds.
It is a readily automated process, making it suitable for a production environment. The process can also weld different thicknesses without the need to exchange the design of tool design (riveting and clinching for instance, would require a bespoke tooling for each thickness/material combination). This reduces the cycle time and costs on equipment in a production environment, especially when joining assemblies comprising various plate arrangements. It is also an energy efficient process without the need for special shielding or cooling units.
Unlike conventional mechanical fastening processes such as bolting or riveting, Refill FSSW does not requir
e the addition of a third element to produce a joint. This means that there is no added weight to the final assembly and no need for pre- or post-joining operations such as hole pre-drilling and cleaning, nor the application of sealants or coatings. The absence of a third element to produce a joint also means that the electrochemical potential of the welded material stays unaltered, providing higher corrosion resistance.
Applications
With the increasing use of lightweight alloys in the various transport sectors, Refill FSSW can provide an alternative solution to applications where established fusion welding and mechanical fastening process may not be suitable. Although the use of this project currently being limited to research applications, the technology lends itself to a variety of potential applications. These include in industries and applications where light weighting is an important factor, such as:
l Shipbuilding and Marine
l Panels for decks, floors and sides
l Bulkheads
l Aerospace
l Skin/stringer applications and closures
l Fuselage and wing structures
l Structural components, such as cellular beams
l Railway industry
l Rail stock vehicle floor, side and roof panels, namely for high-speed trains
l Railway tankers
l Automotive
l Body-in-white components
l Engine chassis cradles
l Car body structures
Application of Refill FSSW on aerospace structures – The OASIS project
TWI has been working with Saab AB, ESAB, Romaero S.A., VZLU A.S., along with Queen’s University Belfast and University West, in an EU Clean Sky2 research project called ‘OASIS’. The key aim is to develop friction stir, refill friction stir spot, and laser beam welding approaches to fabricate ‘rivetless’ welded aerospace structures with the objective of weight reduction, reduction of manufacturing time and costs, while producing components with overall higher stiffness and improved air-side aerodynamic skin properties.
Work started on the OASIS project with TWI and Saab undertaking a design review of Saab’s existing cargo door designs as well as materials selected for skin and stiffner components. Refill FSSW, in combination with a variant of FSW for corner welding, was selected for frame-to-skin and stringer-to-skin joints using high-strength aluminium alloys AA2024-T3 and AA7050-T7451.
Refill FSSW development trials were performed to understand the mechanical and microstructural properties of each spot-weld. To replicate the thickness and materials used in the cargo door demonstrator, a range of parameters were trialled by joining 2mm thick AA7050-T7451 sheet to 2.85mm AA2024-T3 sheet with a sealant interlayer. Inspection and testing of the joints produced in the project was carried out, in accordance with the relevant aerospace standards.
The results from shear testing showed superior performance against conventional riveting. Additionally, fatigue life over one million cycles was achieved for stress values of 50 MPa. Further testing such as exfoliation corrosion, salt spray corrosion and stress corrosion cracking was also performed to assess weld quality.
During the course of this project, an activity based cost model was also developed by Queen’s University Belfast. The labour and joining time involved for this component using refill FSSW process is 21 and 8%, respectively, in comparison with conventional riveting. This translates into a cost savings per component of 12.5% and enables a return on investment in less than one year. By replacing riveted joints with refill welds, a weight savings of 13% per frame can be achieved, which translates into further in-service savings with the increase of range from the aircraft and reducing polluting emissions.
As a physical deliverable, the project also demonstrated and validated the researched approaches on civil aircraft cargo door demonstrators. Offline simulations of the joining activities were carried out both in-house at TWI and at Queen’s University, which helped defining some of the finer-scale design details and clarifying the manufacturing steps. This data was also feed in to cost models. Figure 6 below shows the OASIS cargo door project fabricated using friction welding processes, with the painted frames and stiffners being welded by Refill FSSW through interfacial sealant.