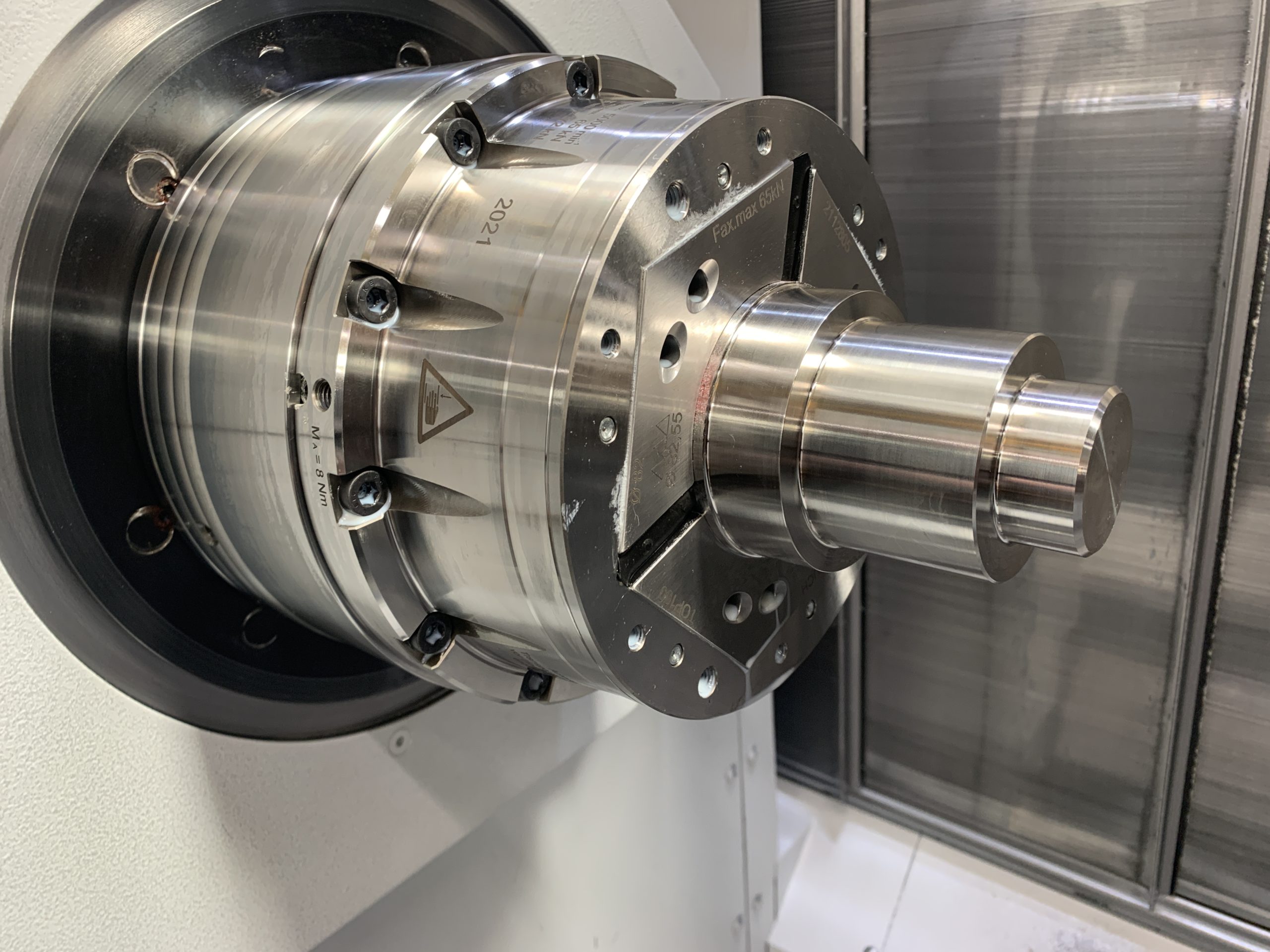
As a specialist stockholder, Intoco recently invited MTDCNC to undertake a series of tests to find the best way to machine Inconel 718. The Cheltenham based company is a respected steel distribution and manufacturing organisation that recognises the importance of the ability to supply raw and pre-machined materials to industry – and that is why they invited the MTD team along with ZCC Cutting Tools and Hainbuch to investigate the best strategies for machining this material that is a challenge for machine shops all around the country.
“Looking at the Inconel 718 material, engineers often ask ‘how does it machine?’ That is such a difficult question to answer. It is a high nickel alloy that is 60% nickel and because of the composition of this material each facet of machining, whether it be milling, turning, threading or boring – every process is slightly different in how it machines when compared to more conventional materials like stainless steel. What we wanted to do is dispel the negativity around machine this material. It is a difficult to machine material, but there are ways around it – and that is what we are here to show,” says Wayne Parkins from Intoco Special Alloys.
The team assembled by MTDCNC that included ZCC Cutting Tools and workholding experts Hainbuch developed several innovative solutions for machining the difficult material. Discussing the project, Nick Peter from Hainbuch says: “The material is very hard to cut, and this gives the cutting tool engineers quite a challenge. From a workholding perspective, the setup needs to be very rigid, and the part needs to be held very firmly. I don’t believe the three-jaw chuck would work in this instance, so we will be using one of our TopPlus collet chucks.”
David Wilshire from ZCC Cutting Tools adds: “We have to take the component away and engineer the process to its optimum performance.” MTDCNC’s Giovanni Albanese adds: “This exercise is highlighting exactly what goes on at the beginning of a process. More often than not, we do not get to see the initial planning and all the potential problems that you need to address along the way to get your solution.” Reinforcing this point, Intoco’s Wayne Parkins says: “The problem we come across when machining the 718 alloy is the life cycle of the tooling we use when cutting.” Unlike some of the MTD videos, viewers don’t get to look behind the scenes at how customers arrive at their outcome – this instance is different.
Commenting upon the project, Hainbuch’s David Noakes adds: “What we have here is a 100mm Hainbuch TopPlus collet. This has the Hex Plus collet system that is totally sealed and ideal for hard metal turning, as it eliminates vibration. With this system, you are clamping against a flat surface which makes it completely sealed. It also provides better rotational clamping forces and when the collet is pulled back into the chuck – it is sealed.”
MTDCNC’s resident workholding expert Gio asks Dave Noakes about the preliminary concerns over the spindle nose of the machine tool. Dave says: “With a machine like this, the DMG MORI NT4300/1500 turning centre – that we may not be too familiar with, we are reliant on the machine tool company giving us the correct data. That information includes the spindle taper and then the draw to diameter and thread as well as the forward and reverse position.”
With the drawings supplied by DMG MORI, the concerns over the stability of the workholding process are alleviated. With this point settled, MTDCNCs cutting tool reporter, Joe Reynolds speaks to Luke Insley from ZCC. Luke tells MTDCNC: “We want to showcase our tooling, so we have opted for a trochoidal turning strategy.” This includes a button turning insert that is run at Vc55m/min with a feed rate of 0.65mm/rev and an Ap of 1mm. This is followed by a 12mm diameter end mill that is applied to machine hexagonal flats around the circumference of the part at Vc=60m/min with a feed rate of 0.08mm per tooth with an Ae of 7%. Luke confirms: “Like with the turning, we opted for a trochoidal milling strategy that enables us to take a shallow depth of cut while moving around the component quickly. This helps to reduce cycle times as well as reducing the load on the cutting tool and the machine spindle.”
From a programming perspective, MTDCNC’s Mark Deadman asks how the strategy is affected by the material type. Answering this pertinent point, Intoco’s Josh Mulka says: “The type of material has a major impact on the depth of cut and the speeds and feeds that we adopt. This is why we are utilising trochoidal turning, as we hope it will improve our tool life while simultaneously speeding up our cycle times. I went on an EdgeCAM course to better understand trochoidal turning. We did have a concern on how we would post from the CAM system to the machine – but by undertaking the course, I had more confidence and we have created a solution.”
With the programming, workholding and cutting tools and respective strategies all in place – the next step was to machine the Inconel on Intoco’s DMG MORI turning centre.
Highlighting the general machining challenges of Inconel, Intoco’s Les Preece adds: “How to machine Inconel is a question that we are asked an awful lot. Complex alloys like 718 and 625 are by nature, high nickel alloys and have challenging machining properties that makes the answer almost impossible to give. It’s not like machining mild steel or stainless steel and each facet of machining presents a different challenge. So, what we do is try to collaborate with some special skills and equipment here to demonstrate the complexities of machining this material – and more importantly how you can overcome those complexities.”
Regarding the material composition and its applicability to specific markets, Les says: “718 principally serves two industries. This is the oil and gas industry and the aerospace market. What we are machining here is the API version for the offshore sector. It is slightly softer than the aerospace version, which is heat-treated differently and comes out harder. The material we are machining is around 38HRc and the aerospace-grade is around 42 to 44HRc. While there are differences, essentially machining is the same.”
Machine Tool Choice
Intoco opted to undertake the project on the DMG MORI NT4500/1500 and alluding to why this machine was selected MTDCNC’s Managing Director, Mr Paul Jones says: “We talked about the right cutting strategies, tools and workholding, but what you need is the foundation where all that starts from. The DMG MORI NT4500/1500 is a true multitasking machine and what this machine has is what DMG MORI refer to as a direct centre of gravity (DCG) machine. This makes the B-axis milling head very rigid as it is supported with a horizontal machining centre construction. It has a ball screw on either side of the head and it is a box in a box construction also. This makes it one of the most rigid ways of supporting the machining head. This is important as you need the strength, the power and the stability surrounding the mechanics so it can dampen out any vibration.”
The machining process.
Adopting cutting tools from ZCC throughout the process, the Inconel part was rough turned with a CNMG insert from 80mm to 65mm diameter with a 42mm diameter for secondary threading. With a depth of cut of 2.5mm, the roughing insert ran at a feed rate of 0.22mm/rev and a surface speed of 40m/min. This was followed by a groove tool that machined a 5mm wide groove at a speed of 70m/min and a feed rate of 0.15mm/rev with a 5mm depth of cut. This was followed by the previously mentioned trochoidal button turning strategy that was followed by a U-drill to drill 26mm diameter at 20mm depth at a feed of 0.07mm/rev and speed of 55m/min. The next process was the drilling of 5mm diameter holes at 10mm DoC on the periphery of the part. One of the final steps was the M42X1 threading operation.
The Outcome
Dave Noakes from Hainbuch states: “The solution has performed better than we thought it would. The Hainbuch chuck with the ZCC tooling has been incredible – the roughing finish looks just like a ground finish. This shows that there is no vibration or chatter.” Adding to this, Intoco’s Wayne Parkins says: “We’re very impressed. The workholding was exceptional and got rid of any vibration from cutting 718 and the tooling has cut very well compared to how we would have previously done the job. We have saved 30% cycle time compared to how we would have previously cut this job. Additionally, we have run this job quite conservatively and we could probably push the machine and the cutting tools a little harder to improve upon the 30% cycle time reduction.”
ZCC’s David Wilshere adds: “We were very confident that we would get positive results considering the stability of the machine and also the workholding. We wanted to apply several strategies to get the best productivity rates and by employing trochoidal turning strategy through the grooving process, we have achieved a minimum of 30% improvement in cycle times – taking the cycle time to 23.5 minutes.”