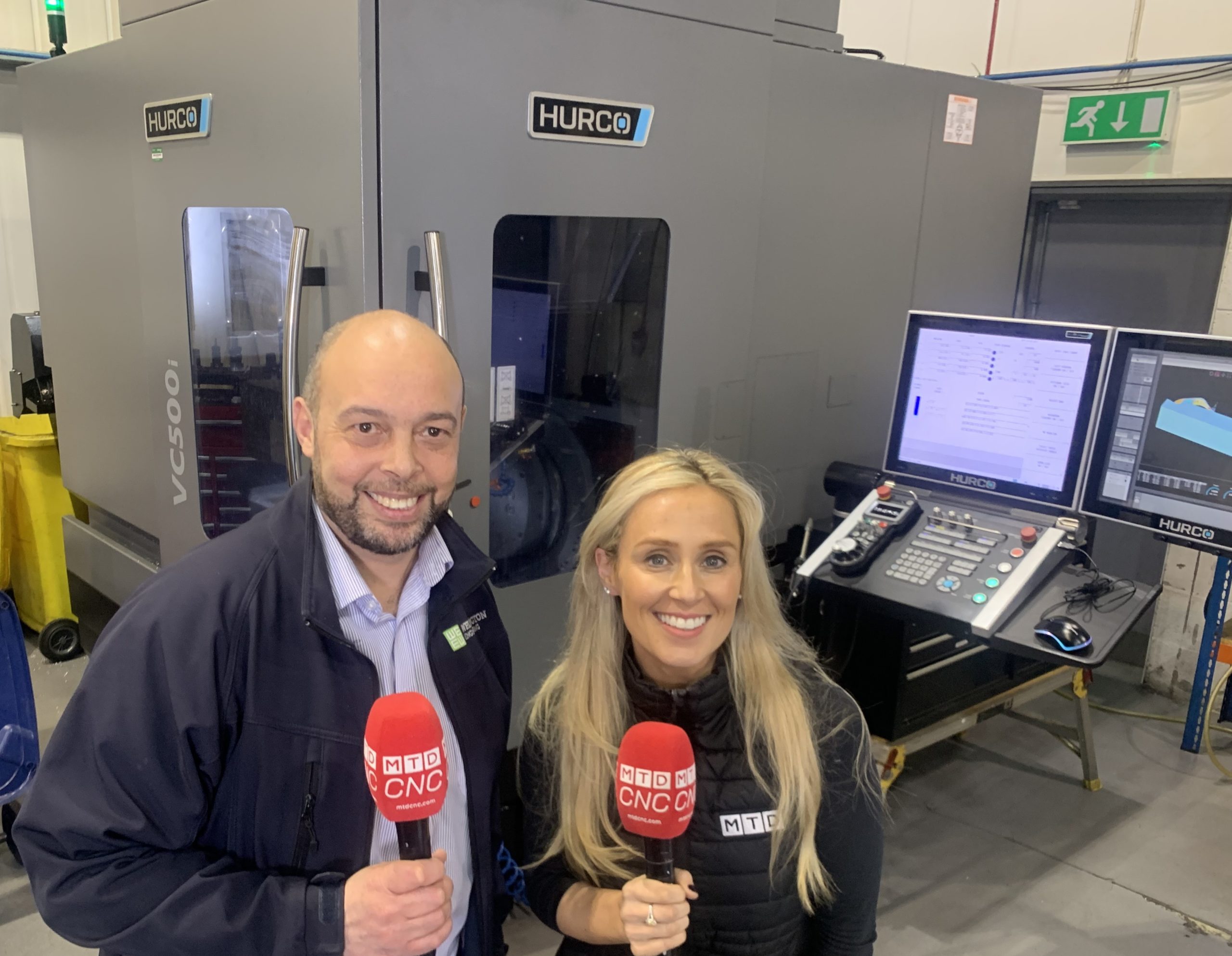
Located in Hayes, Wellington Engineering Ltd was founded in the 1980s as a subcontract machine shop that now serves industry sectors as diverse as aerospace, medical and research, semiconductor and cryogenics.. With over 40 staff, the company has invested in machine tools from manufacturers such as Ajax and Colchester through to Doosan – but the one brand that takes centre stage is Hurco.
The machine shop has 45 CNC machine tools, but the prismatic machining department is full of Hurco machining centres with everything from the smallest VM10 through to the larger capacity Hurco VMX42M. The latest addition is another Hurco machining centre, a 5-axis VC500i.
Alluding to why the company has invested in the latest 5-axis VC500i, Daimon Wellington from Wellington Engineering said: “As a business owner, it is all about productivity and producing more complex components. To accomplish this, we need 5-axis machinery. We have a lot of Hurco machines here, but this was the next step up technology.”
Discussing why productivity and the purchase of the 5-axis machining centre are so important, Daimon adds: “Productivity drives profit – and we all need that. Equally, we have been seeing a lot more complex-shaped components coming into the business, and it is taking too long for our conventional processes like 3 and 4-axis machining to get parts out of the door. Since we have had the 5-axis machine, we have had some excellent results. Parts are now coming off the machines quicker, but we are also freeing capacity from other machines and we are seeing a lot less deburring and secondary hand finishing. It frees up our other machines to do other work.”
Looking at the pain points of the business before stepping up to 5-axis machining, Daimon adds: “We knew the type of work we wanted to put on the machine, but we had to ensure there was enough work to justify the purchase. However, I have seen far too many complex components taking far too long to get through the business and they were taking too much time on too many machines. The complex setups were also taking too much manpower and creating workholding issues. With the Hurco 5-axis, we are getting components through the factory much quicker and our cycle times are reduced, giving us confidence that we can tell our customers exactly when they will receive their components.”
Looking at how the company is calculating the impact of the latest Hurco addition, Daimon says: “We have machine efficiency software that monitors how often the machine is running, the cycle times and other parameters. We are seeing benefits through that. Additionally, we don’t have to put complex parts through 3, 4 or 5 machines. We had a situation recently where an employee called in sick and this broke our process chain of jobs on the machines – everything is a jigsaw puzzle. With the 5-axis Hurco, we know we can put a job on the machine and get the parts off in a maximum of two operations.”
“We all appreciate that there is not a huge pool of young engineering talent coming through, so investing in machines that can do the job of 4-5 people can negate this situation. Yes, there is a skill to it, but with the Hurco support and the ease of the programming, we can produce lovely components in very good times.”
“We are now looking at jobs differently. Every job we look at, is potentially a job for the 5-axis machine. The machine is set up as a simultaneous 5-axis machine, we also have jobs where we will just do five-sided machining.” Concluding on the benefits of the machine that has only been installed a few months, Daimon adds: “We are already getting reports back from our customers that we are really starting to compete with the low-cost sourcing outfits, whereas before some customers would go abroad because they would get better pricing or shorter cycle times overseas. Another huge benefit is jobs that were taking three or four weeks to go through the shop floor on multiple machines are now passing through our process chain a lot quicker, so we can invoice quicker, get paid quicker – and then we free up the machines for more new work.”