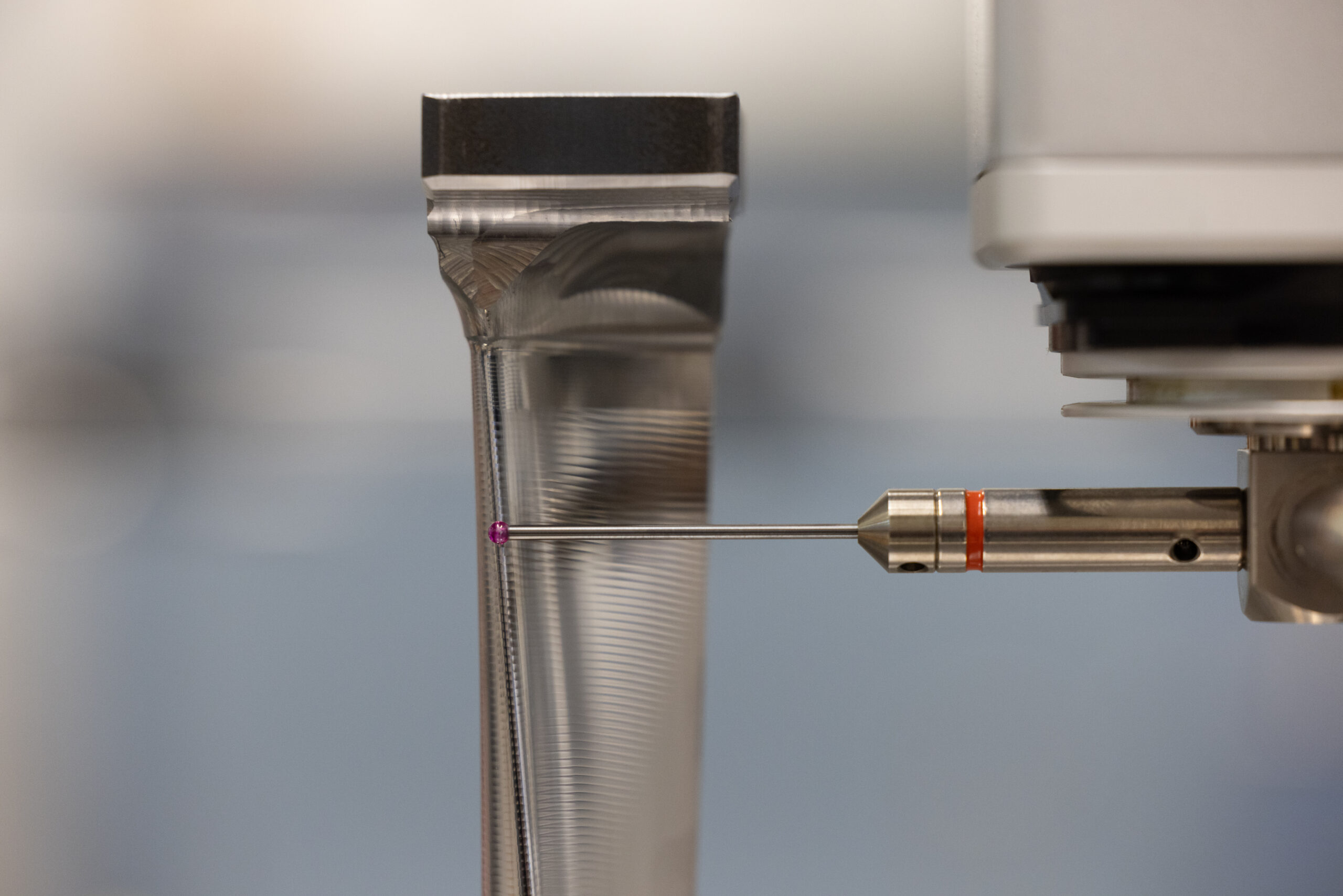
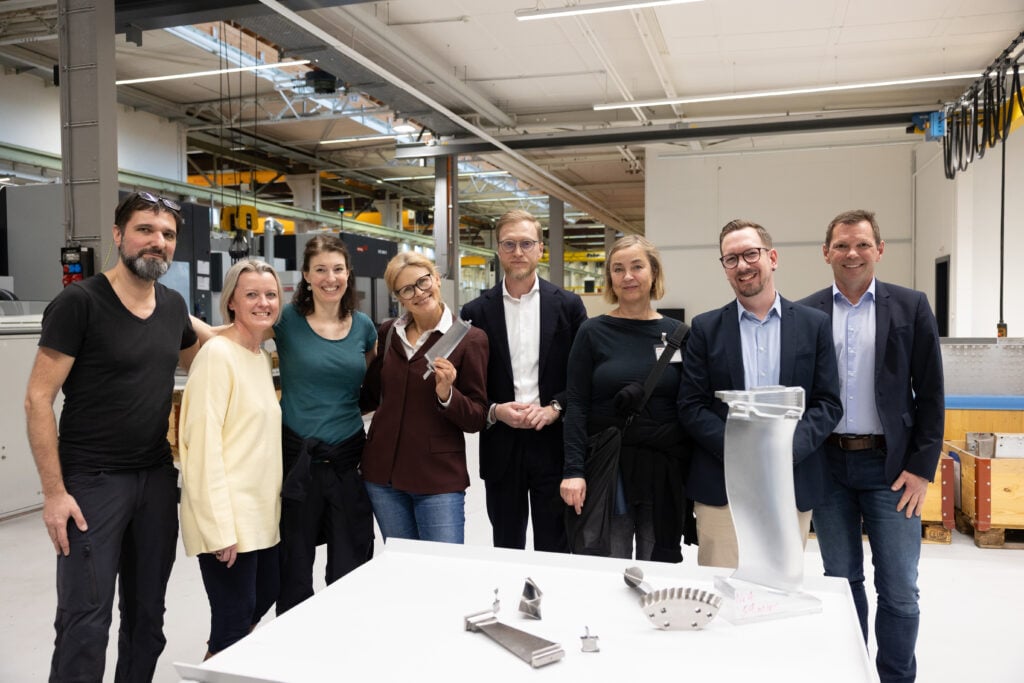
Starrag develops and produces manufacturing solutions for many of the aerospace industry’s leading manufacturers. As part of a pilot project to shorten the measuring times for turbine blades, the Swiss company was the first in the world to work with the ZEISS PRISMO fortis CMM.
Customers react with fascination and great amazement when they see how accurately and quickly turbine blades can be measured on a ZEISS PRISMO fortis with ZEISS CMM Acceleration Mode for aerospace applications. Roland Ziltener, Plant Director at Starrag AG, Rorschacherberg, says: “Speed and maximum precision didn’t go together for a long time.”
Customer requirements have top priority
Customers from all over the world come to Rorschacherberg with their specific tasks to obtain suitable machining centres to produce turbine blades and other aircraft applications. Starrag designs the respective production solution with the appropriate fixtures based on the specified requirements for the number of units or running time of the components. Customers often want a complete solution that ranges from machine and tool to metrology programming.
For Ivan Nytsch, Head of Global Customer Segment Aerospace at ZEISS, Starrag is ‘an ideal pilot customer’. This is also because the provider of complete solutions is very familiar with its customers’ processes. ZEISS has responded to the aerospace industry’s challenge of measuring aerospace components with high precision, reliability and speed by expanding the PRISMO family with the ZEISS PRISMO 7/12/7 fortis CMM
Fascination for a new solution
Roland Ziltener, who was Head of Quality Management at Starrag says: “We had a look at the machine and were immediately impressed.” To check whether the new development delivers the required precision despite the considerable optimisation of the measuring time, all turbine blades manufactured by Starrag on behalf of partner customers were measured with the ZEISS PRISMO fortis over 18 months. As the size, material and geometry of the turbine blades are different, the machine was “widely tested”, according to Ziltener. To evaluate the accuracy of the ZEISS PRISMO fortis, the measurement results were compared with reference values from the ZEISS PRISMO navigator.
During the pilot phase, Ziltener and Nytsch agreed that Starrag and ZEISS worked closely together. For example, the measurement data was discussed together in regular meetings. ZEISS used this information to optimise further the start-up and acceleration behaviour of the rotary table and the machine. ZEISS also simplified the usability of the machine and the creation of test plans during the pilot phase.
Turbine blades and blisks are not only subject to stringent requirements but also cost companies a lot of money. Experience has shown that quality assurance accounts for 20% of total production costs and 25% of total production time. The pilot project showed that productivity in the measurement of turbine blades can be significantly increased with ZEISS PRISMO fortis. The standard measurement, which took four minutes and 30 seconds at Starrag and delivered accurate and reproducible results, was reduced to 70 seconds during the pilot phase. This saves time, “which gives us greater flexibility in the selection of parameters and workpieces to be measured and helps us to optimise our production processes,” emphasises Ziltener.
Starrag acquired the measuring machine at the end of the pilot project to measure turbine blades, which are produced as a proof of concept during the acceptance of the machining centres assembled at the site by the customer. The turbine blades, which are machined for a handful of customers at the Aerospace & Turbine Competence Centre, continue to be inspected using the ZEISS PRISMO fortis.
Subscribe to the MTDCNC Newsletter
Subscribe to our Newsletter today!
Stay up to date with the latest industry news and events.
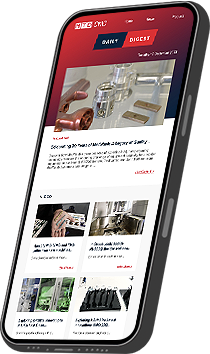