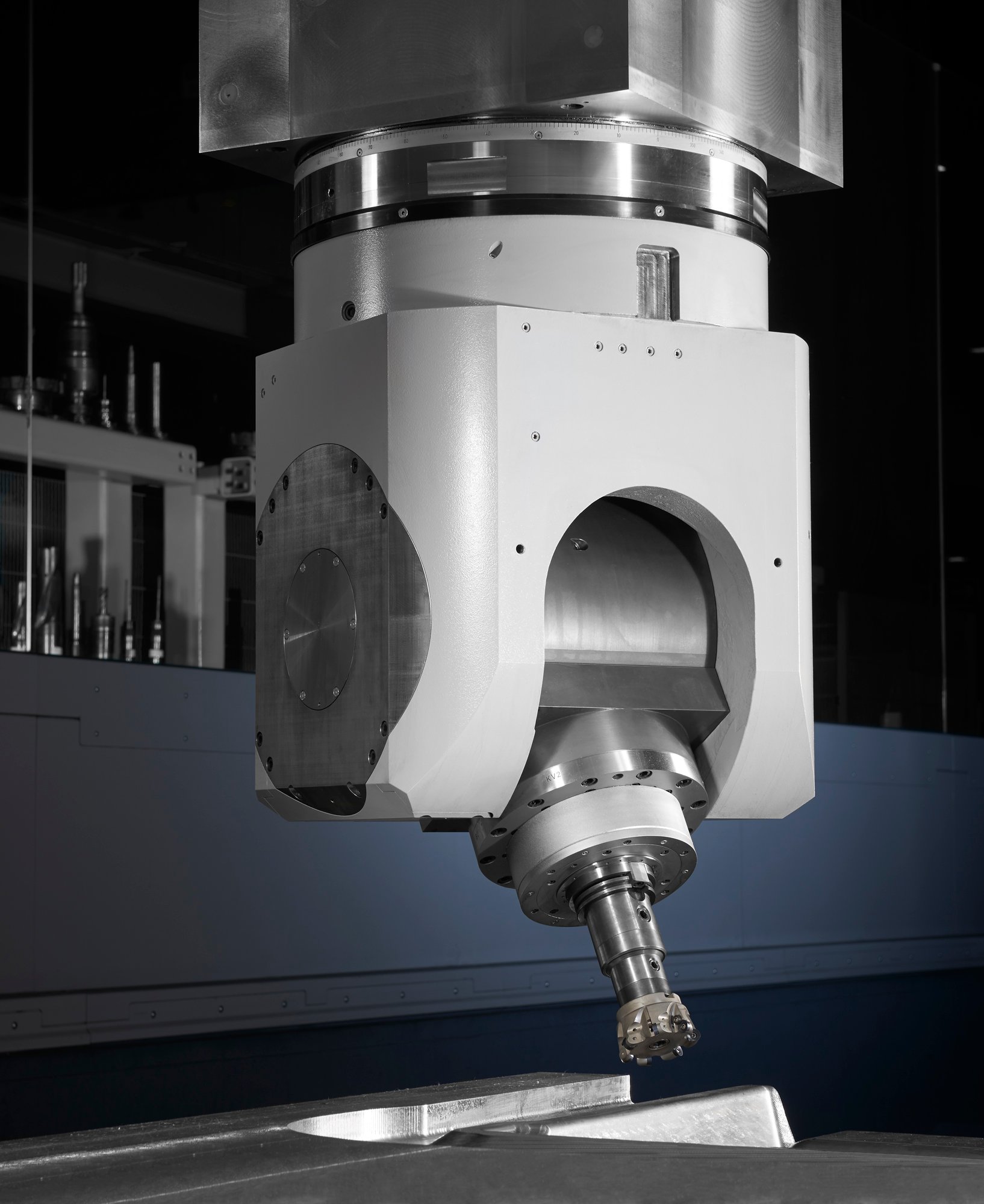
On Stand 110 in Hall 17 at MACH, McDowell Machining Technologies will be demonstrating why it is the premiere machine tool solution supplier for the heavy manufacturing sectors. From the 4th to the 8th of April, McDowell will be introducing the colossal machining technology available from WaldrichSiegen part of the globally renowned HerkulesGroup, as well as their industry leading solutions from Niles-Simmons.
In early 2020, WaldrichSiegen investigated the UK market to find a technical partner rather than historical sales agents that have come before. After speaking to several machine tool references throughout Europe to gain insight into the UK heavy and large capacity machine market to ascertain who was active in this field, the answers kept coming back the same – McDowell Machining Technologies. This company has become known for prioritising the large and heavy machine tool sector over commodity machine sales and are actively a technical project sales-driven company.
Commenting upon the relationship, McDowell Machining Technologies Managing Director, Mr Stuart McDowell says: “It was very well received being contacted by WaldrichSiegen, since entering the large machine tool market more than 15 years ago, our business has gained vast experience and exposure with many OEMs. It has always been very clear who the top performers are, who has the best product offerings and who has the stature to deliver on large projects. With this knowledge, it was very easy for me to encourage the advances of WaldrichSiegen and enter into a long term strategic partnership. We have formed excellent working relations over the past couple of years and are very excited about what the future holds.”
McDowell Machining Technologies will support its partners with its ever-expanding team that currently operates with 16 service and applications engineers that are supplemented further by reliability and project engineers. This resource was attractive to WaldrichSiegen, but more important is the collective experience and exposure to heavy hydrostatic machines and the environment they operate in. At MACH, this expertise will be on-hand for show visitors to discuss their large machining projects.
Commenting upon the new relationship, Dr. Thorsten Mehlhorn, President and CSO of HerkulesGroup global sales said: “In the course of our further strategic alignment, the UK market is an important milestone in our growth. We were looking for a technically experienced partner who is experienced in the large and heavy machine tool sector. We are very excited about our future strategic partnership with McDowell Machining Technologies. Our focus lies on target-oriented and innovative consulting by technically experienced personnel. We are looking forward to continuing a professional and cooperative partnership.”
Reinforcing this opinion, Marco Tannert, the President and COO WaldrichSiegen states: “With McDowell Machining Technologies, we found a professional partner in the UK that is a technical expert for heavy machine tool projects and has significant experience in maintenance and repair works for all kinds of large machine tools. Together, we will be able to take our service to UK customers to a new level.”
Introducing the WaldrichSiegen brand to MACH for the first time, McDowell Machining Technologies will be highlighting the range of machines that encompass everything from milling, turning, vertical turning, turn/mill centres, grinding and boring machines. The WaldrichSiegen series of portal milling machines will be introduced at MACH and with a fixed or movable cross rail, the ProfiMill is available with a clearance between the columns from 3m to 14m with a clearance from the table or floor plate to the spindle nose of 2m to 12m with table width from 2.5m to 8m with a length of 5m. If the dimensions appear incomprehensible, the exhaustive choice of milling units all manufactured by WaldrichSiegen will certainly resonate with engineers.
Complementing the ProfiMill is the ProfiTurnV vertical lathe that excels in precision, efficiency and reliability. The ProfiTurnV stands out from its competitors due to its uncompromising performance and precision in roughing, semi-finishing or finishing. The ability to integrate a variety of technologies allows for the highly flexible machining of complex workpieces. The fully hydrostatic design in all main axes guarantees the ultimate in cutting performance and accuracy whilst guaranteeing no wear to critical surfaces. Facilitating parts up to 500 tonnes with maximum turning dimensions of 13m diameter by 11m height, the ProfiTurn V rotary table is available with power of 300kW with 560,000Nm torque and Y-axis. Ram (Z-axis) travel of up to 4m is available with numerous ram sections and attachments selected to best suit the application.
Across both ProfiMill & ProfiTurnV platforms, the standard W-axis cross rail is integrated due to its dynamic capabilities. This axis optimises the axis positioning to suit the individual workpiece and directly influence cutting performance. The fully equipped axis tracks all machine geometry and doesn’t influence workpiece datums when moved for instance to a second home position to change a head or a tool. Not only are these operations fast, but also do not compromise quality. Furthermore, the standard ‘no counterbalance’ system also has a huge influence on machine reliability and performance. By removing the counterbalance, it effectively removes a part of the machine that requires intensive maintenance – ropes, chains, pulleys, cylinders and valves.
There are further benefits to the machine performance, the counterbalance does in effect apply the same force in the opposite direction to what gravity creates. By equalling this force, there is a load on the positioning system of the machines that needs to be overcome when moving. This load creates wear on the ball screws, heat on the motors and drives, and makes fine positioning more challenging. By removing these factors, the machine is much more reliable and accurate. The standard C-axis design located within the ram brings added capability to all the milling heads by enabling them to move continuously through the Z-axis. For heavy workpieces that require contouring with complex tool paths, this additional feature means the machines do not have to dramatically move the workpiece (in C&Y) and instead move over the part in all axes without limiting access whilst ensuring stability.
WaldrichSiegen is acclaimed for producing the world’s largest horizontal turning centre with a 7m swing and turning length of 35m, capable of accommodating parts up to 350 tonnes the WaldrichSiegen range of ProfiTurn H (horizontal), and ProfiTurn M mill/turn centres available from McDowell Machining Technologies set the standard for heavy turning. Designed for maximum performance, the ProfiTurn H can also be specified as a turn/mill centre to reduce set-ups and improve productivity and flexibility for customers. The ProfiTurn H provides the highest level of accuracy, reliability and performance that enables high quality and economic machining of complex workpieces. The rugged design demonstrates maximum stiffness of the overall machine structure, and the range is equipped with hydrostatic guideways in all linear axes to provide high, wear-free operation along with excellent damping characteristics. From a power perspective, the H series delivers up to 500kW of power with 400,000Nm of torque. Despite the ability to support oversize and heavy workpieces, the H Series retains a concentricity of up to 5 microns – truly amazing for components of such size.
For more complicated components that demand milling capacity, the ProfiTurn M series has been designed specifically for the complete machining of complex workpieces. Turning and milling units, as well as boring and grinding units can be attached to the master head interface located on the milling tower. The result is the highest efficiency, as all stages of the machining process are performed on a single machine, eliminating multiple set-ups that are both elaborate and costly. Whether turbine or generator rotors or heavy forged parts – the ProfiTurn M has been developed for the precise and efficient machining of demanding workpieces with a diameter up to 4.5m, with a maximum workpiece weight from 20 and 250 tonnes.
Continuing the impressive machine portfolio is the globally renowned Union horizontal borers. A selection of floor, planer, table and compact boring machines are offered with a seemingly endless list of options to tailor the machines to the customer requirements. The Union machines guarantee the efficient machining of workpieces with a length up to 40m and a height up to 10m with a weight of up to 250 tonnes.
From the cost-effective solution with universal applicability up to high-end equipped boring machines for XXL workpieces, the modular structure of the P/PR series, the double hydrostatic guidance, and the dynamically controlled hydrostatic system allows both to have roughing and high-precision machining.
That being said, not everything in the WaldrichSiegen range from McDowell Machining Technologies has unfathomably large dimensions, as the TM125 table-type compact boring mill demonstrates. This innovative foundation-free compact boring mill for the effective and cost-efficient machining of workpieces up to 10 tonnes with a set-up area of up to 2.5m by 2m by 1.6m. It combines the advantages of a table-type boring mill with those of a compact machining centre. Despite the size of the TM125 and the similarly sized KG precision series of boring mills; precision, stability and repeatability is assured. The KG range demonstrates positional accuracy of less than 8microns.
Whilst WaldrichSiegen provides ideal solutions for heavy manufacturing sectors such as the offshore and wind energy, power generation, mining, engine manufacturers and the steel making industries, the smaller, agile Niles-Simmons brand of machines will also be presented at MACH with a host of automotive and aerospace demonstration components that will highlight the flexibility, precision and scale of what is possible with these incredible machines.
The Niles-Simmons brand is the true epitome of high-quality bespoke manufacturing solutions with unparalleled precision and productivity. As the brand of choice for many of the world’s leading OEM manufacturers, the Niles-Simmons portfolio includes everything from turning and turn/mill centres, vertical turning centres and 3 to 5-axis machining centres that can all be tailored to the exacting demands of the end-users. The MC-series of turn/mill machines range from the N20 MC to the N60 MC with a turning diameter from 650 to 1500mm and a maximum turning length up to 7.5m. These machines can be configured as single or multi-slide machines and thanks to the modular building-block system, a variety of machining units can be added to offer the utmost flexibility. Adding value to these machines, Niles-Simmons can incorporate gear hobbing, skiving, grinding, deep hole drilling, ID machining with a boring quill, 5-axis milling, crankshaft milling units, up to three steady rest slides and much more.
Alongside these incredible systems, McDowell Machining Technologies will present a selection of vertical turning centres with the RQ and RQQ variants offering single or twin turning tools that can engage with the workpiece simultaneously to improve productivity whilst the RMC range is equipped with a turn/mill unit for the machining of rotationally symmetric workpieces up to 1.6m diameter. These machines would be of a typical interest for the highly efficient machining or railway wheels or large disk type parts. For more information on the product offerings and solutions available from McDowell Machining Technologies and their partners WaldrichSiegen and Niles-Simmons, visit them at MACH 2022 on stand 17-110.