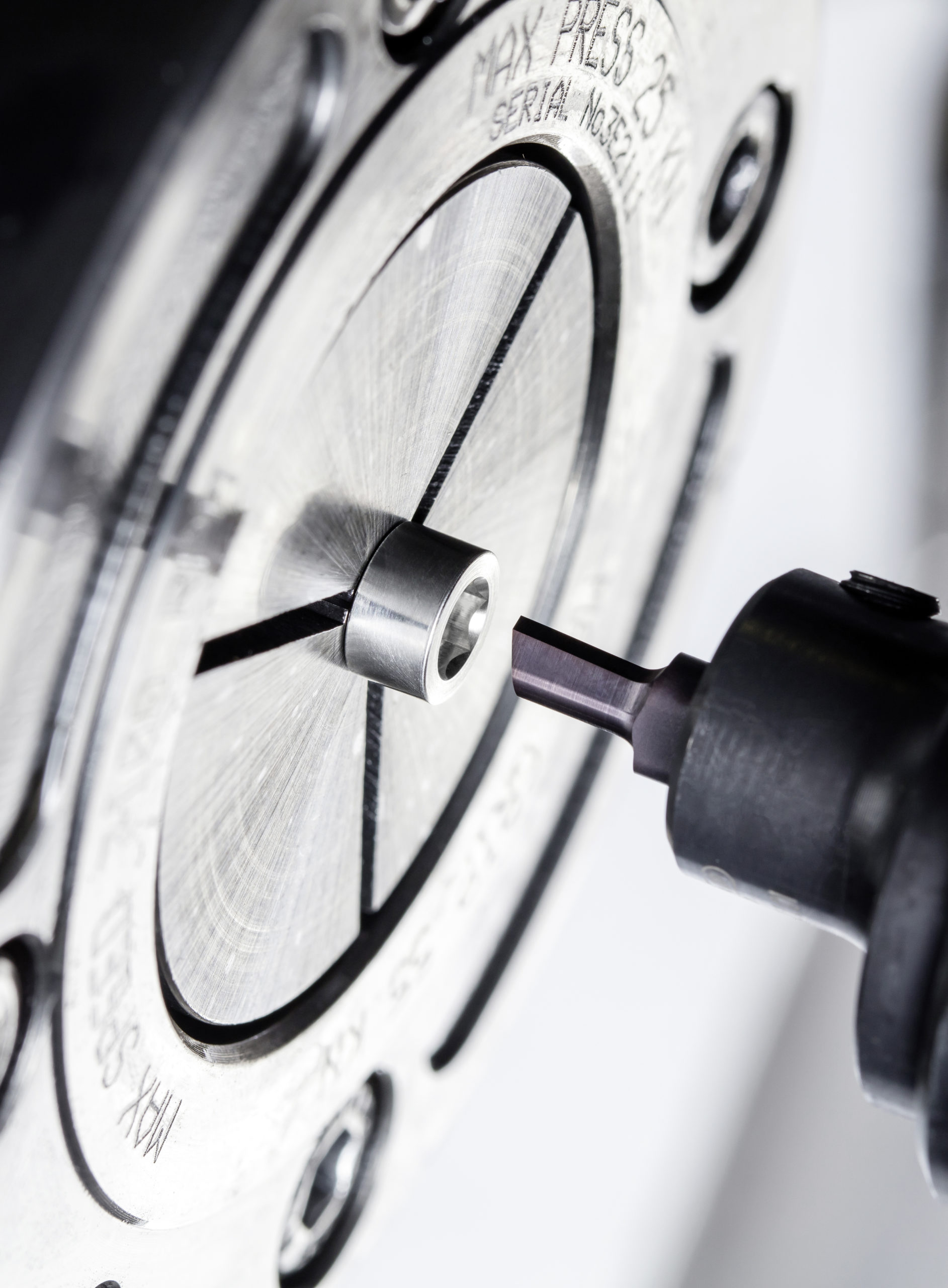
“When machining cobalt-chromium alloys, we demand very high performance from the tool due to the high material costs,” explains Tibor Veres, the Managing Director of Hymec Fertigungstechnik GmbH from Norderstedt near Hamburg. This company relies on tools from Paul Horn GmbH to machine its superalloy components.
The precision tools from Horn are also used for shaping hexagon sockets of implant screws made of cobalt-chromium. Together with Horn’s, Thomas Wassersleben, they transformed this demanding machining task. The company specialises in medical products and demanding low-volume production. Machining materials such as high-strength aluminium and titanium alloys, implant steels and superalloys like cobalt-chromium (CoCr) are part of Hymec’s day-to-day tasks. The range of activities includes the production of precision-engineered components and complete assemblies as well as providing technical advice.
Close collaboration
Hymec has been working with Horn for 30 years. “The cooperation has been outstanding because they always provide a cost-effective solution for our applications,” explains Veres, who is always looking for the best tool solution for his machining tasks.
The screw is an implant and forms part of an artificial knee joint. Hymec manufactures the screws in various widths across the hex flats of 2.5mm, 3.5mm and 5mm. The hexagon socket is machined to a tight tolerance so that the screw sits firmly on the hexagon key during insertion. The surface finish also needs to be of high quality as even small grooves and ridges can be a breeding ground for germs on the 5,000 screws manufactured every year.
Broaching is virtually impossible in series production
“Machining a hexagon in titanium is relatively easy by profile broaching. Broaching in series production in cobalt-chromium is virtually impossible due to its high strength and the tool wear is significant,” says Veres. Due to this, Wassersleben proposed producing the hexagon socket using the shaping process. The method offers high precision and reliability as the cutting geometry and the carbide substrate can be adapted to the material being machined. The first tests quickly discovered the required solution.
The shaping process follows hole drilling with the Horn DD system that drills 4.9mm diameter into the screw head. The drill with internal coolant supply is from the standard range with a geometry designed for stainless steels. The conical base of the blind hole is used as clearance for the shaping tool during machining. Due to the shallow height of the screw head, it was not possible to use an undercut as clearance. The tool moves along a programmed path to break the chips at the end of the flat.
A Supermini N105 performs the shaping of the socket with a width across the flats of 5mm. The infeed of the individual stroke is 0.02mm. After completing a surface, the chuck indexes for machining the next surface. The processing time of the shaping operation is around two minutes on a Mori Seiki lathe. Veres is pleased with the performance: “The cutters are precise and barely any correction is required after a tool change. We are also very happy with the tool life of 100 screws per cutting edge.”
The hardness and toughness of the cobalt-chromium required modifications to the cutting edge geometry, the carbide substrate, the coating, the machining conditions and the coolant. The hard particles in the alloy tend to form crater wear and work hardening of the surface. The cutting edge is sharp and not rounded, as it is for titanium machining, but unlike titanium machining, the wedge angle is of a more stable design. A tough micro-grain grade is used as the carbide substrate. The high material price also places stringent demands on the process reliability of the tools used.
Material for medical technology
Depending on the manufacturer, cobalt-chromium generally consists of 50–90% cobalt, 10–30% chromium and additional alloying components such as molybdenum, tungsten, niobium, manganese or silicon. CoCr is one of the highest performing materials for endoprosthetics. The material is particularly suitable for artificial joints due to its high bio-compatibility and its corrosion resistance.
Screws for endoprosthetics
0:00 / NaN:NaN