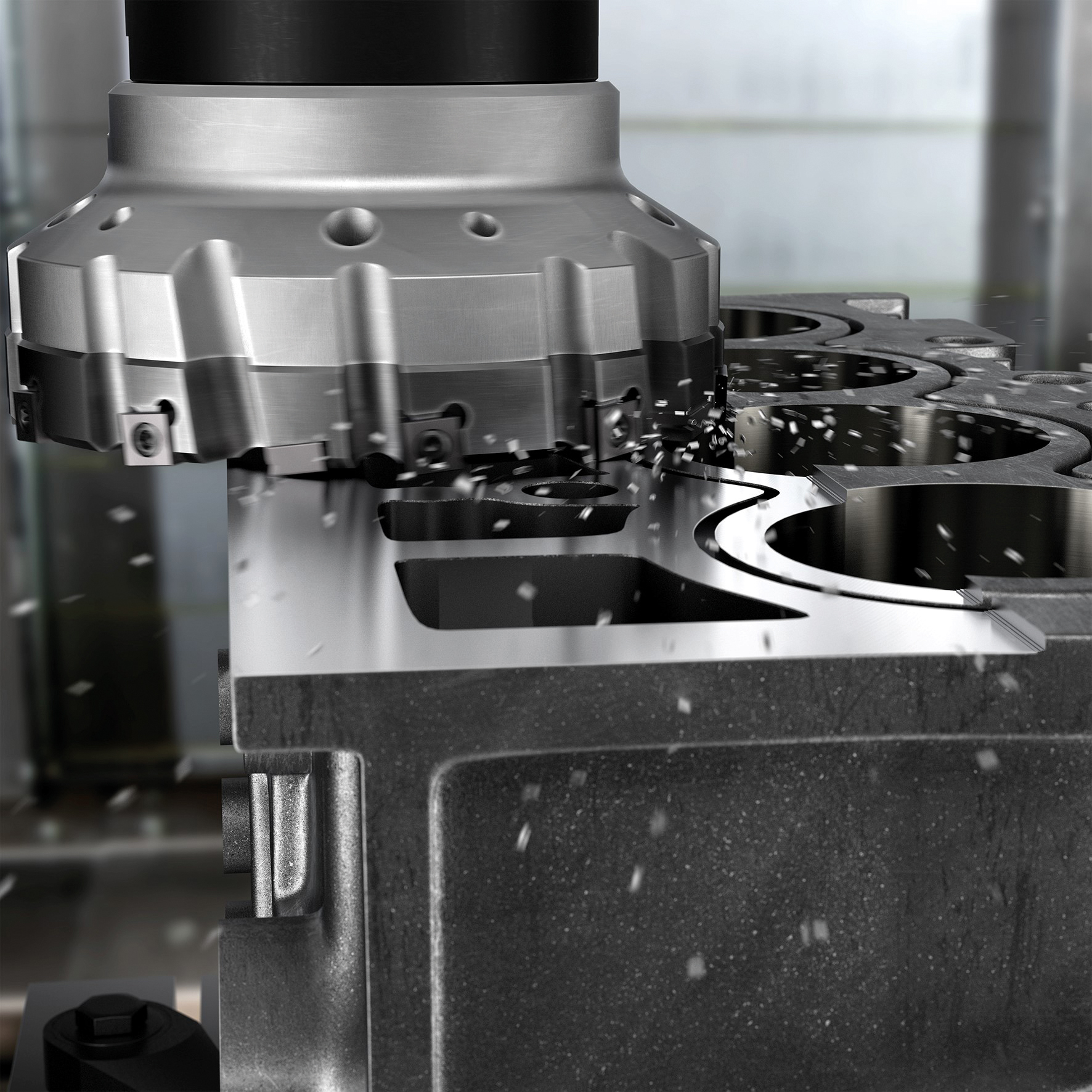
The automotive industry faces a weight dilemma. In 2017, light-duty vehicles manufactured in the US weighed, on average, 4,044 lbs — not always living up to their name. New components and technologies add weight, yet environmental concerns also demand that manufacturers make them lighter. As a lighter material, aluminium can address this, but also presents machining challenges. Here, Eduardo Debone, Global Segment Manager – Automotive at Sandvik Coromant, explores how a single milling cutter might hold the solution.
Aluminium’s use in aviation predates even the first aeroplane as, in the late-1800s, Count Ferdinand crafted the frames of his famous Zeppelin airships from aluminium. Now, aluminium use in automotive engine blocks can provide considerable weight savings and improvements in fuel economy.
Elsewhere in transport, the power train of a European passenger car typically contains around 80kg of aluminium, which makes the engine and gearbox an obvious area for light-weighting. With aluminium increasingly-favoured, machine tool builders require dedicated tooling solutions to work with it.
Component complexity
The cylinder block is the main structure of an engine and is responsible for housing several moving parts that generate power to move the vehicle. For years, the block was made from cast iron alloys but aluminium alloys are now the common choice.
Manufacturing cylinder blocks involves the largest number of machines in automotive production, with complex and tight tolerance processes. Rough and finishing critical components such as cylinder blocks is expensive and time-consuming. It requires several different tools; which means increased setup and coolant to reduce heat during heightened friction machining. An engine’s cylinder head is an equally vital component, often made from aluminium. It conveys air and fuel to the combustion chamber and sits on top of the cylinder block, housing valves, spark plugs and fuel injectors. Aluminium may be lighter than cast iron counterpart, but its also softer. Therefore, poor finishes, burring and irregular tool wear are all common. So, how can automotive manufacturers get beyond these challenges?
A one-shot solution
Sandvik Coromant has found that innovation lies in simplicity. By implementing a single solution, rather than multiple tools for face milling operations, manufacturers can address the many challenges of aluminium. A one-shot milling cutter can provide both roughing and finishing in a single tool and reduce strain on aluminium to achieve higher quality results.
Sandvik Coromant’s solutions include several patented designs like the M5C90 aluminium cutter, part of the M5 product family, designed for the rough and finish face milling of cylinder heads, cylinder blocks and all-aluminium parts within wide cutter engagements, aside from thin-wall parts. The tool can complete the entire process from roughing to finishing, in just one go.
The tool can perform rough and finish milling in just one pass and, in many cases up to 6mm axial depth. We have seen it extend tool life by five times, with a 200% cycle time reduction.
A key feature of the M5 family is its step technology. A series of precise and long-lasting PCD tips arranged in a circular configuration to progressively remove a bit more material, both axially and radially. Also, the last tooth in the tool is a wiper design that provides a superior finish and flatness. The fixed position of the wiper and the teeth also eliminates complex and time-consuming pre-setting procedures. As part of the environmentally friendly quest for better performance, selecting the right materials will be integral to making vehicles lighter. At the same time, the simple approach offered by tools like the M5C90 aluminium cutter offers manufacturers a way to overcome the demands and complexity of machining aluminium. Then, perhaps aluminium can take its rightful place as an antidote to the automotive industry’s weight dilemma.