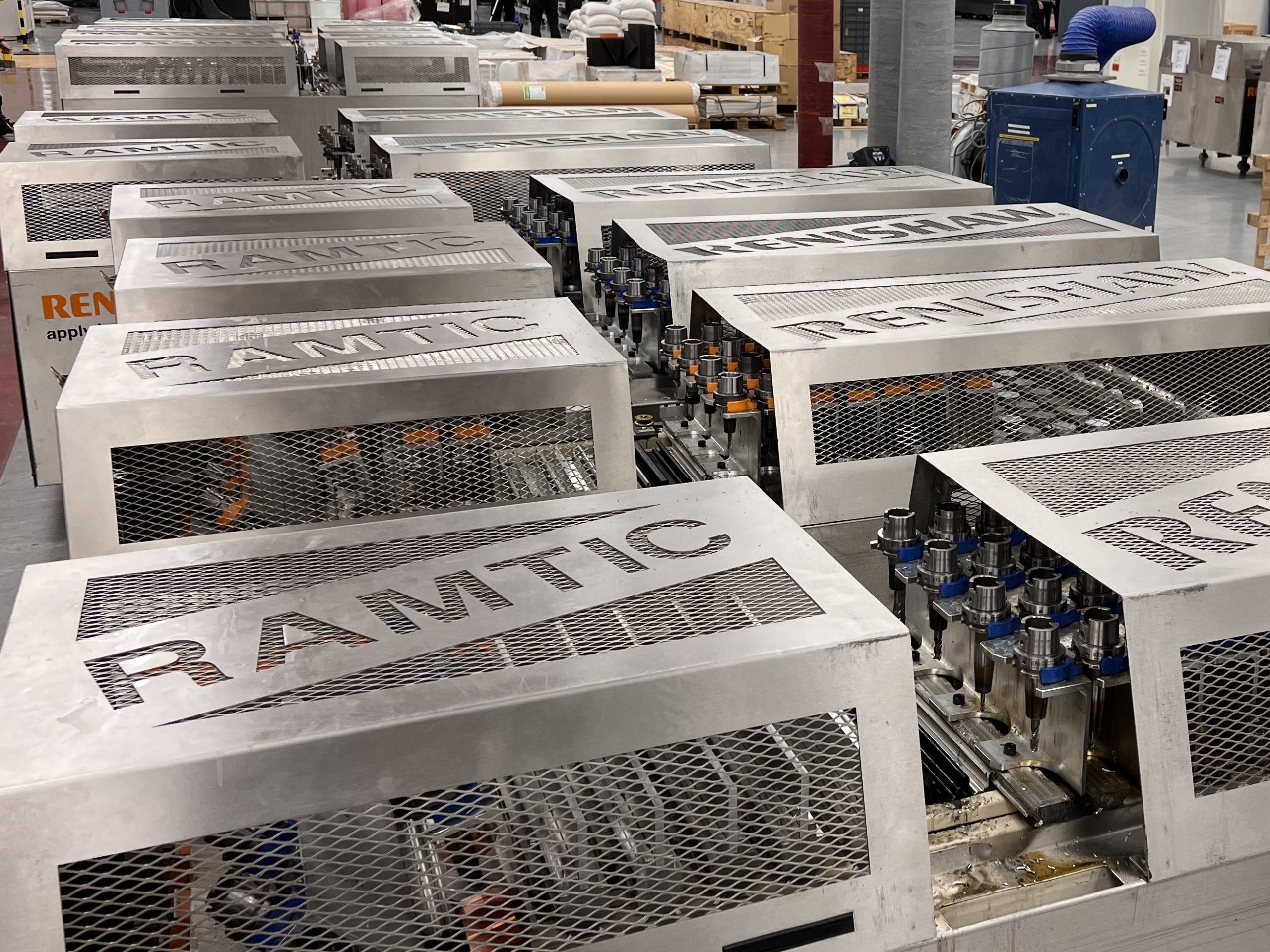
Next month, Renishaw will be celebrating its 50th anniversary. As a FTSE 250 company and one of the UK’s most prominent manufacturing success stories, MTD magazine toured the Renishaw Miskin facility in South Wales and witnessed what can only be classed as the epitome of modern manufacturing. By Rhys Williams
As an apprentice machinist, I served my time in the South Wales valleys and then worked at the Bosch alternator plant near Cardiff. Shortly after the departure of Bosch in 2011, Renishaw acquired the same 193-acre site, and our recent visit was my first opportunity to return to the plant in more than 25 years. The investment made by Renishaw in this manufacturing facility is a sight to behold…
Whilst the original security gatehouse and two production halls with more than 460,000sq/ft remain outwardly similar, the transformation of the internal factory space is a testament to the long-term investment strategy – but Renishaw isn’t a company that stands still. With a colossal steel framework and construction teams currently working on-site erecting two new production halls, evidence of over £50m additional investment is apparent. We spoke with Jonathan Archer, General Manager of Renishaw UK Sales Ltd to find out more.
Investment for future growth and expansion
Discussing the investment, Jonathan told MTD magazine: “Planning permission was granted to increase the capacity of our Miskin site. This underpins our future growth ambitions and helps towards our 2028 Net Zero targets for Scopes 1 & 2 GHG emissions. The Miskin site is used for precision CNC machining, electronics production and final product assembly. It is also the production location for Renishaw’s metal additive manufacturing machines. Work is now underway for two additional production halls and an employee welfare facility. The additional production halls will provide over 380,000sq/ft of manufacturing space – almost doubling our capacity.”
Alluding to the technology planned for the new production halls, Jonathan adds: “Although the details are yet to be determined, the capacity will allow for increased machining operations and the assembly of products already built at the site including our metal additive manufacturing machines.”
The Manufacturing Strategy
The Miskin site produces parts for various probing systems, position encoders, CMM and gauging systems and additive manufacturing machines. As Jonathan says: “All of those components are CNC machined here or in Stonehouse and the final product assembly takes place here in Miskin or at other factories in Gloucestershire and near Dublin in Ireland. Our vertically integrated approach gives us total control of quality and delivery time. Having this control enables us to rapidly adjust our manufacturing capacity in accordance with demand and guarantee continued product supply.”
“A part of our business continuity plan is that we mirror critical manufacturing processes in our other factories. This ensures production capacity and supply of parts and products in any eventuality. We can supply CNC machined parts and any subsequent finishing operations and complete electronics manufacturing from multiple locations.”
Renishaw produces more than 1 million CNC machined parts per month with an average of over 3,500 works orders (machine set-ups), this includes over 2,500 automated CNC operations with zero manual set-up time. Despite the variety of parts produced, the combined machine shops deliver over 80% value-added output with typically less than 1% scrap. This performance is accredited to Renishaw’s ‘Productive Process Pyramid™’ philosophy ensuring consistent output, quality and performance from the CNC processes to enable automation and reduce manual intervention.
With the current Miskin factory expansion, ramping up capacity will undoubtedly send the component volumes to new levels. To accommodate this, the company must have robust CNC processes in place, the Productive Process Pyramid philosophy that controls variation before, during and after machining is the perfect strategy to underpin highly automated production processes.
Discussing this, Jonathan continues: “There is a big shift in manufacturing towards automation. Here at Miskin, with our automated machining capability, we have 4 staff overseeing over 40 machining centres, our goal is to be lean and efficient. We’ve got lots of processes in place, including the RAMTIC system, (Renishaw Automated Milling, Turning and Inspection Centre), which enables us to implement very lean manufacturing with integrated metrology using our own products. We share this approach with our customer base, we listen to our customers to understand their shifting requirements and needs. We show them the things that we do here and that is an enabler for us to provide solutions and help them with their manufacturing challenges.”
“One of the philosophies at Renishaw, the ‘Productive Process Pyramid’ goes back over 20 years. It’s a drive to simplify, standardise and control the CNC machining process, the tooling, the machining set-ups and more. The RAMTIC automated system is a shining example of this philosophy in action.”
RAMTIC is a unique automation system developed specially by Renishaw for their own production needs. The creative solution enables Renishaw staff to firstly pre-set all the cutting tools and raw materials for a product ‘kit’ into fixtures away from the machining centres. The tools and fixtures are loaded onto a unique mobile pallet system called a carousel. This is then transported to an available machining centre and docked in position. Once connected and information loaded into the machine there is no further manual intervention. We’ll look more at this fantastic innovation in more detail in a future issue.
Adding to this, Jonathan says: “We move the RAMTIC carousel to the machine once it’s been kitted offline with tools and material. Swapping these carousels over at the machine takes only half an hour, so we then machine in sequence, multiple part numbers or discrete operations using up to 50 pre-kitted fixtures, these product carousels run for between 15 to 30 hours. All the machine set up, tool set up, process control and verification are carried out without manual intervention, This not only enables significant lights-out machining but also smaller batch sizes matching assembly demand.”
Machining over 1 million parts for a wide range of products each month would be a challenge for any business. So, the various Renishaw product design teams work with manufacturing to create as much commonality as feasibly possible. As Jonathan continues: “We aim to standardise across our new product development process including design for manufacturing, assembly, test, packaging and more to ensure we minimise variation, unnecessary process development and maximise re-use of best practice or known capability wherever possible. That’s been a big part of our ethos for years. This approach has allowed us to increase our capacity, reduce new product development time and to allow us to scale operations when we expanded our machining and assembly capacity to the factory here in Miskin.”
The Productive Process Pyramid™
The philosophy applied by Renishaw features a four-layered, preventative approach to controlling CNC machining processes, it starts with the base-level process foundation then process setting, in-process control and post-process monitoring. For absolutely every element of the process chain, Renishaw has built-in predictable process steps that encompass everything from the machine tool, its environment and equipment such as tooling, work holding, process design and fixtures, as well as the machining strategies and all other potential sources of variation.
Taking an overview of the Renishaw philosophy, Paul Maxted, Director of Industrial Metrology Applications, Renishaw plc told us: “The Pyramid essentially identifies all sources of process variation whether it’s raw materials, the factory environment, any manual processes, or the CNC machine and machining process. It accounts for every stage and what could go wrong with variables such as tool holders, cutting tools, fixtures, alignments and day-to-day conditions. We put the controls in place to keep on top of those variables and manage those.”
When we introduced the RAMTIC process, we identified around 150 different failure modes. We then formulated strategies and have the controls in place to eliminate, compensate or identify causes of variation. This encompassed everything from electronic work instructions to audits and automated checks to make sure we are within acceptable control limits. If we deviate, we can identify and manage the situation. For example, our in-process probing allows us to measure all the variables affecting the physical machining process at its very core. That is effectively managing the failure mode and a broad selection of parameters. This minimises variation across our large population of machines. These measurements can also tell us in detail what, where and when things are affecting process capability.”
Integrating Technology to create valuable solutions.
The beauty of having a world-class manufacturing facility where R&D teams, manufacturing and application engineers can collaborate, develop and test, is that broader customer solutions can be developed and enhanced.
Looking at Renishaw’s relationships with its customers, Jonathan continues: “It’s a part of our DNA, we manufacture both low and high volume, but certainly a high variability of products across both of our manufacturing facilities. We experience the same challenges as our customers. Some customers are very niche, and some manufacture high volumes, but they all rely on CNC machining as a core process. As we ‘practice what we preach’, it gives our customers confidence in Renishaw; we are much more than an equipment supplier. When we bring customers to our facilities and we’re responding to their manufacturing challenges, they take a great deal of confidence away in terms of what they see here and at Stonehouse.”
“As a company, we re-invest somewhere between 13-18% of our sales revenue back into R&D. This is substantial for our industry and important for our future as we continue to apply innovation in all we do.”
Looking at the future product pipeline, Jonathan adds: “I can’t be too specific, but we have roadmaps in place across all our manufacturing technology product groups covering industrial metrology, position measurement and additive manufacturing. Each product group has a roadmap of new technologies, some of which are reasonably short-term and some that are very much in the distant future. It’s a clear part of our strategy to continually invest for our long-term success.”
Discussing product development to sales, Jonathan continues: “We are fortunate that we can develop and trial many of our products internally as well as conduct trials at customer sites before they’re commercially available. It is common for customers to come to us with a part or a manufacturing challenge and ask us to demonstrate time-savings or improvements in the manufacture or measurement of a part or a particular set of features. This instils customer confidence before investing in our technology whether that’s hardware, software or usually both – it’s a kind of try-before-you-buy principle.”
With Renishaw R&D receiving industry feedback from their global sales and marketing teams and having the facility to trial new products internally as well as with test-bed customers, it creates a perfect ecosystem for continuous innovation.
One recent example of the developments tested internally in Renishaw’s manufacturing is the ‘Renishaw Central’ system. This enables accurate, actionable data-driven manufacturing. Renishaw Central is a connectivity and data platform that collects and presents manufacturing process data, allowing users to monitor and update machining and quality control systems. It allows for closed-loop CNC process control using its unique and patented Intelligent Process Control (IPC) software functionality.
Alluding to this, Jonathan says: “Renishaw Central supports manufacturers in their end-to-end manufacturing processes, whether they are subtractive or additive machining. Each process step guides the user through measurement whether that’s on-machine probing, near machine probing using the Equator™ gauging system or CMMs on the shop floor. The end-to-end process provides data that includes information on how the different devices are performing, what is happening, enabling interventions to be made at the right time. Software and this critical process data gives manufacturers insight across the entire process to enable continuous optimisation and improvement. Using our own manufacturing facility to gather process data, analyse and implement improvements gives us invaluable first-hand experience to support and add value.”
“There is a continuous dialogue between our product design groups and our commercial teams globally to consider customer expectations, requirements and challenges feeding our new product pipeline. Our future innovations must address or even exceed the ever-evolving challenges of the industry.”
With the company celebrating its 50th anniversary this year, we’ll be back with Renishaw in the next issue to report on the progress and plans the company is implementing.
Renishaw - 50 and fit for the future
0:00 / NaN:NaN