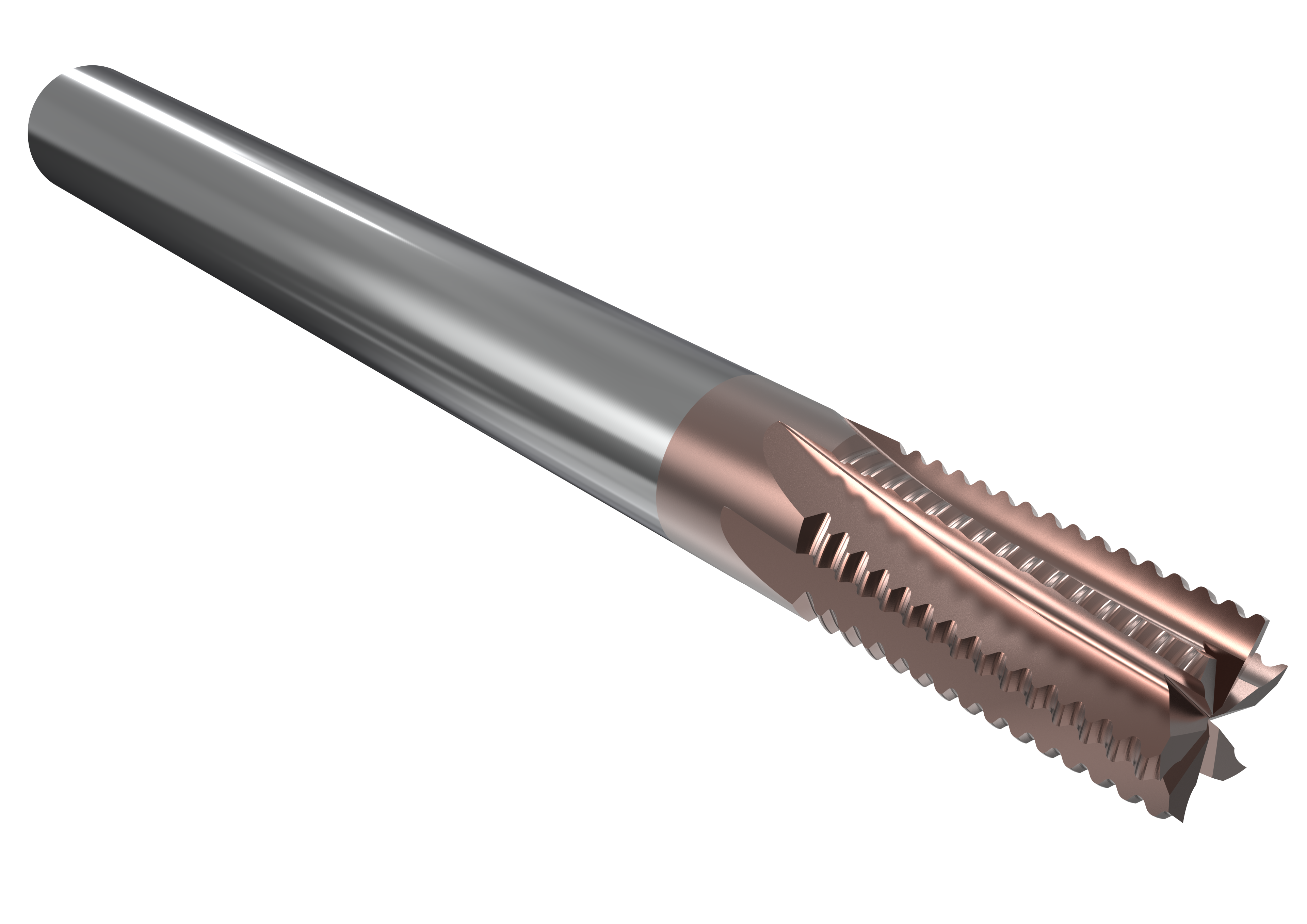
Over the last 12 months, Quickgrind has been developing new tools with clients to create application-specific solutions to some of the most demanding challenges that industry can throw at a manufacturer. The industry is constantly testing the ‘Infinite Possibilities’ slogan of the Tewkesbury cutting tool manufacturer, and every time Quickgrind is breaking the boundaries of convention.
Recently, Quickgrind has encountered several challenges from aerospace, motorsport and F1 companies that require new solutions to existing problems. One customer in the aerospace industry is manufacturing large components from a 40mm thick CFRP (Carbon Fibre Reinforced Polymer) sandwich panel. Initially, Quickgrind was tasked with implementing solid carbide tools on monolithic 10mm CFRP – the challenge for Quickgrind was to retain the same level of productivity, quality and edge finishes whilst reducing tooling costs through the implementation of solid carbide tools to a process that was using high-quality PCD tools.
Commenting upon the new technologies being developed, Quickgrind’s Commercial Manager, Mr Tim Darch says: “At Quickgrind, we realise how large the UK market for high-quality cutting tools has become as customers decide to look for alternatives to poor quality throw-away, off the shelf imported carbide and highly expensive PCD tooling. We are creating a suite of innovative new solutions that can bridge this gap for the industry.”
Clients are quite rightly becoming more discerning as to who they partner with, not just to provide an alternative to single-use PCD tooling, but also to really understand where substantial process improvements can be made, whether that be time, cost, speed or finish. To do that properly requires core understanding of the customers current and future states, married with a deep knowledge of what is possible with carbide tooling. The developments we are doing around CFRP tooling is an extension of our core ethos of constant tooling innovation.
“We are doing this by improving the capabilities and potential of carbide tools without the cost implications of investing in PCD cutting tools. PCD tools have specific benefits and applications and at Quickgrind we realise this, so we also offer a comprehensive range of PCD solutions. However, there is a significant number of manufacturers that may not machine the quantities of CFRP to justify investing in PCD tools – this is where Quickgrind offers an effective solution.”
The Challenge
Quickgrind applied it’s ‘Infinite Possibilities’ approach to work alongside an aerospace OEM to engineer a solution for machining monolithic material. The challenge for Quickgrind was to maintain the machining performance and cycle times of existing PCD cutting tools whilst reducing costs. Easier said than done, the challenge for Quickgrind involved machining the material whilst preventing de-lamination of the CFRP, minimising thermal impact, retaining surface finishes and managing swarf evacuation.
Upon successfully achieving its aims, Quickgrind was then asked to machine the complete sandwich structure. The sandwich panel consisted of an aluminium core encased in two layers of CFRP material.
Quickgrind has developed a proprietary technology that considers all features of the cutting tool from the composition and edge preparation through to the geometry and coatings.
Furthermore, the challenge required plunging, full depth slotting, drilling, pocket machining and processing the perimeter of the parts with a 40mm depth of cut. Achieving all of these processes that also included the machining of six pockets, the Quickgrind solution needed to machine over 11m before any tool change or inspection.
Commenting upon the application, Quickgrind’s Application Support Manager, Mr Mark Aspinall says: “We worked with the client and looked at all the variables that affect the process such as machine tool configuration, spindle power, toolholding, workholding, tool paths and swarf evacuation. Based on these variables and working on a large bed 5-axis gantry-type machine, we developed a series of cutting tools incorporating Quickgrind’s innovative ‘Amrita’ vibration-reducing technology along with various coatings. The Amrita innovation was initially developed for aluminium alloy machining, and we have transferred this technology to machining CFRP. Two of the key challenges with CFRP machining are heat and the opportunity for vibration. The Amrita technology counteracts the impact of vibration when cutting thin and rigid materials like CFRP. This improves tool life and longevity, reduces the risk of delamination and heat build-up and it also improves surface finishes. In this instance, the components have to undergo stringent NDT testing and meet impervious quality conformance frameworks.”
“The brief for Quickgrind was to provide a cost-effective cutting tool for the routing of monolithic material with the ability to plunge, causing no delamination or fibre pullout with little to no changes of the current process being carried out with current PCD tooling, including the feed rate. We achieved this with our 10mm diameter solid carbide tool with an end-cutting geometry and 100mm overall length. What’s more, the tools can all be remanufactured to further reduce costs at our Tewkesbury manufacturing facility,” says Mr Aspinall.
“We have reduced the cost of tooling per part by more than 50% whilst retaining the same machining parameters for this customer. At present, we are undertaking more development work with the Advanced Forming Research Centre (AFRC) in Strathclyde and their customers on CFRP machining. Thus far, the trials with AFRC and our customers have encompassed the machining of 3mm thick CFRP for F1 body panels as well as the machining of hollow CFRP handlebars and cranksets for an elite cycling team. In all examples, the trials have proven successful, and as these groundbreaking innovations evolve from drawing board to finished product, Quickgrind is on-hand with our ‘Infinite Possibilities’ to support the customer every step of the way,” concludes Mr Aspinall.