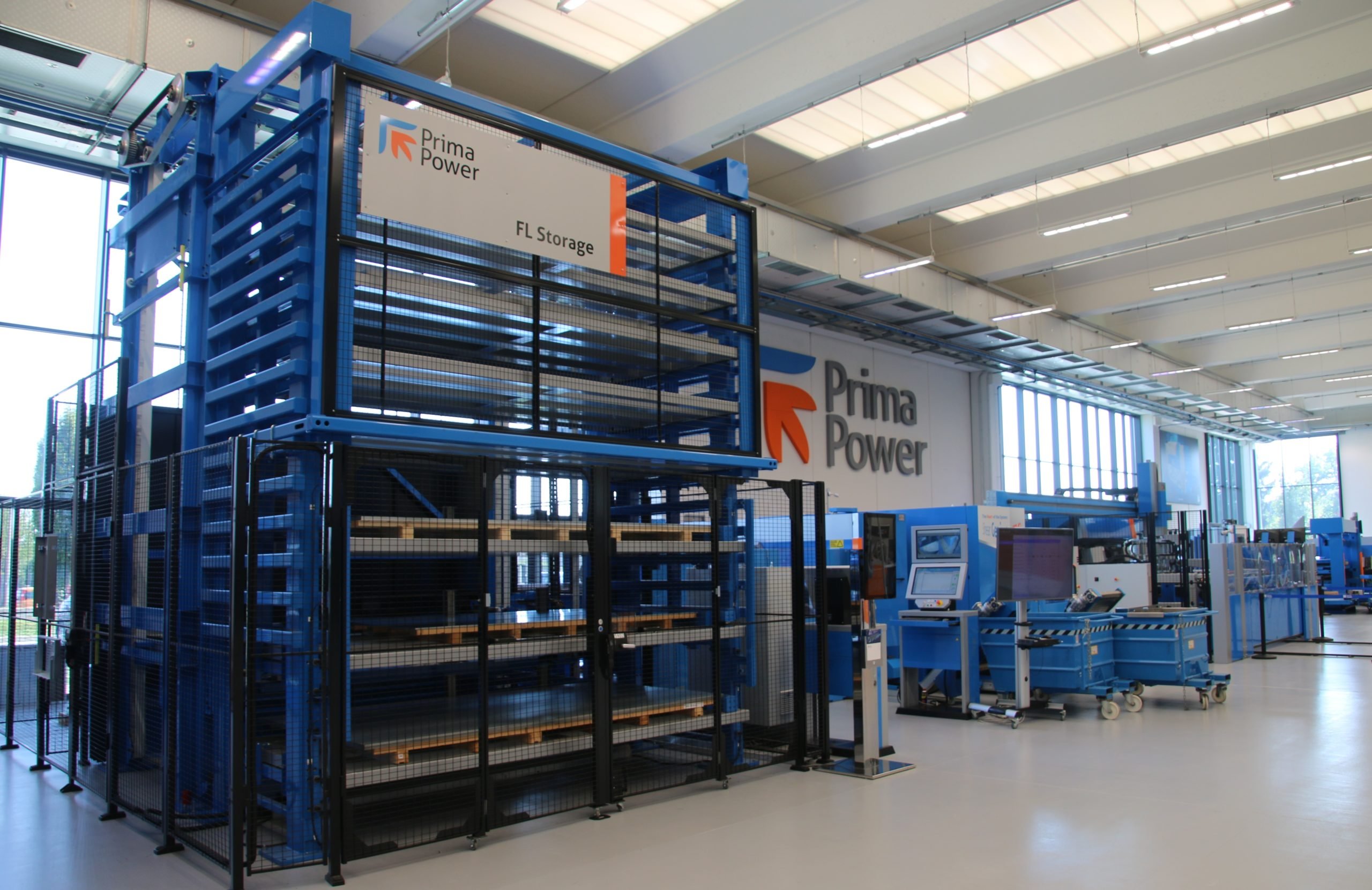
At the height of the summer heatwave, MTD magazine travelled to Prima Power in Turin where the technology was hotter than the weather! The Italian beacon of innovation is home to the HQTC (Headquarters and Technology Centre) and it is here that we witnessed demonstrations of the latest technology and learnt more about the company’s rich history – something that has set the standard in the automotive industry for generations.
As the laser and sheet metal business unit of the Prima Industrie Group which is listed on Milan’s Stock Exchange, Prima Power is a technology trailblazer. It is in an enviable position whereby companies within the Group are specialist manufacturers of mechatronic and optoelectronic systems, automation, software and more – creating complete autonomy over the development and manufacture of its technology. With a product range that encompasses 2D and 3D laser, punching and combined punch/laser and punch/shear machines, press brakes, panel benders, FMS and automation, and software, the company has eight manufacturing facilities spread across Italy, Finland, the USA, and China.
During our visit, we toured the HQTC – a facility that is home to the very latest technology the company has to offer. Not just a showroom, this innovation centre is also a test and demonstration facility where manufacturers from all sectors ‘prove-out’ and optimise their projects, finding the complete solution to their production issues. At the time of the trip, the HQTC presented a diverse range of technologies that included the Laser Next 2141 3D Fiber Laser, the Laser Genius+ 1530 2D Fiber Laser, the Print Sharp 150 powder bed fusion additive machine, the BCe Sharp Panel Bender, the eP-1030 Genius Press Brake and the jaw-dropping PSBB (Punch, Shear, Buffer, Bend). For engineers that cannot afford the time to make a trip to Turin, live video feeds of demonstrations and trials can be undertaken….although such an impressive facility is definitely worth the visit.
On approach to the Turin facility, the modern buildings with an architectural design akin to the style that is synonymous with high-end Italian fashion brands and sports cars meant we were in for a treat – and we weren’t disappointed. The reception displayed the Olympic torches from both the London 2012 and Rio 2016 – both produced on Prima machines and also an aerospace exhaust system, all demonstrating the bending, punching, cutting and forming potential of what we were about to see.
The Technology
With so much to see, it is impossible to discuss the HQTC and the machines within in the detail they deserve – but thankfully you can watch the MTD videos online. Starting with the eP-1030 Genius Press Brake, the 3m 105-tonne machine is the epitome of bringing technology and automation to what has long been a manual process. The O-frame machine with dual-servos provides an even distribution of bend force whilst the Genius element provides tool storage and automatic tool changeovers that make set-ups and changeovers an extremely fast and efficient step. The tool carousel stores 32m of tools, something that can be connected to two machines to reduce floor area, improve automation and create production autonomy. With worldwide skills shortages, power consumption and environmental considerations at the forefront of most business concerns – the eP-1030 ticks all the boxes with its low energy, low maintenance and simplified operation.
Alongside the eP-1030 was the BCe Sharp Panel Bender, a step further into the world of automation with the facility to manually or automatically load/unload sheets. With a control that allows parts to be processed individually, in batches or as kits, the sophistication of the Prima Power TULUS software suite makes programming, simulation, scheduling and storage a breeze for operators of the latest machine in the range.
With additive manufacturing technology increasingly penetrating the manufacturing sector, Prima Additive (the business unit of Prima Industrie Group dedicated to metal additive manufacturing solutions) has made its first 3D printing step with the Print Sharp 150 powder bed fusion (PBF) machine. The Print Sharp 150 utilises a single 300W laser with a layer thickness from 0.02 to 0.12mm that can reach a build volume of 150mm diameter and 160mm height – printing a diverse range of materials from stainless and nickel alloys to copper aluminium and more. With buzzwords like ‘circular economy’ being banded around the industry and more manufacturers conscious of reducing waste and looking at ways to repair failed components, Prima Power has also developed its 3D printing technology to go beyond PBF – offering Direct Energy Deposition (DED) technology.
The DED technology enables manufacturers to additively melt powder to areas of parts where it is needed. This can now be integrated into the company’s Laser Next (LN) Series of 3D Fiber Laser machines – opening a world of opportunity for manufacturers by retrofitting a DED head kit or even a laser welding head to existing fiber laser machines. To witness the potential of the Prima Power laser technology, we were given a demonstration of the Laser Next 2141 3D Fiber Laser. The largest model in the 3D Fiber Laser series, the LN 2141 offers 2.1G of acceleration and 4G on the C-axis. The speed and acceleration are possible due to a lightweight aluminium gantry and carbon fibre laser head that minimises the forces placed upon the structure whilst a synthetic granite base provides stability for a positional accuracy of 0.03mm. The lightweight design ensures the machine requires no floor foundation and the 2.1 by 4.1 by 1.02m work area can be configured into single or split cabins and tables, so one part can be unloaded whilst the machine is processing another part.
The LN 2141 on show demonstrated this concept with a split cabin. On one side was a fixture with the tailgate for a prestigious UK vehicle manufacturer being produced – and in the next cabin was a rotary table set-up. Commenting upon this, Prima Power UK General Manager, Mr Barry Rooney says: “Prima has been at the forefront of laser cutting since the 1970s when we developed the first 3D laser cutting system for the automotive industry. It all began when automotive companies moved to hot forming body panels to increase the strength and safety characteristics of vehicles. In the age of the modern vehicle and particularly EVs, this technology is more prominent than ever for another reason – light weighting.”