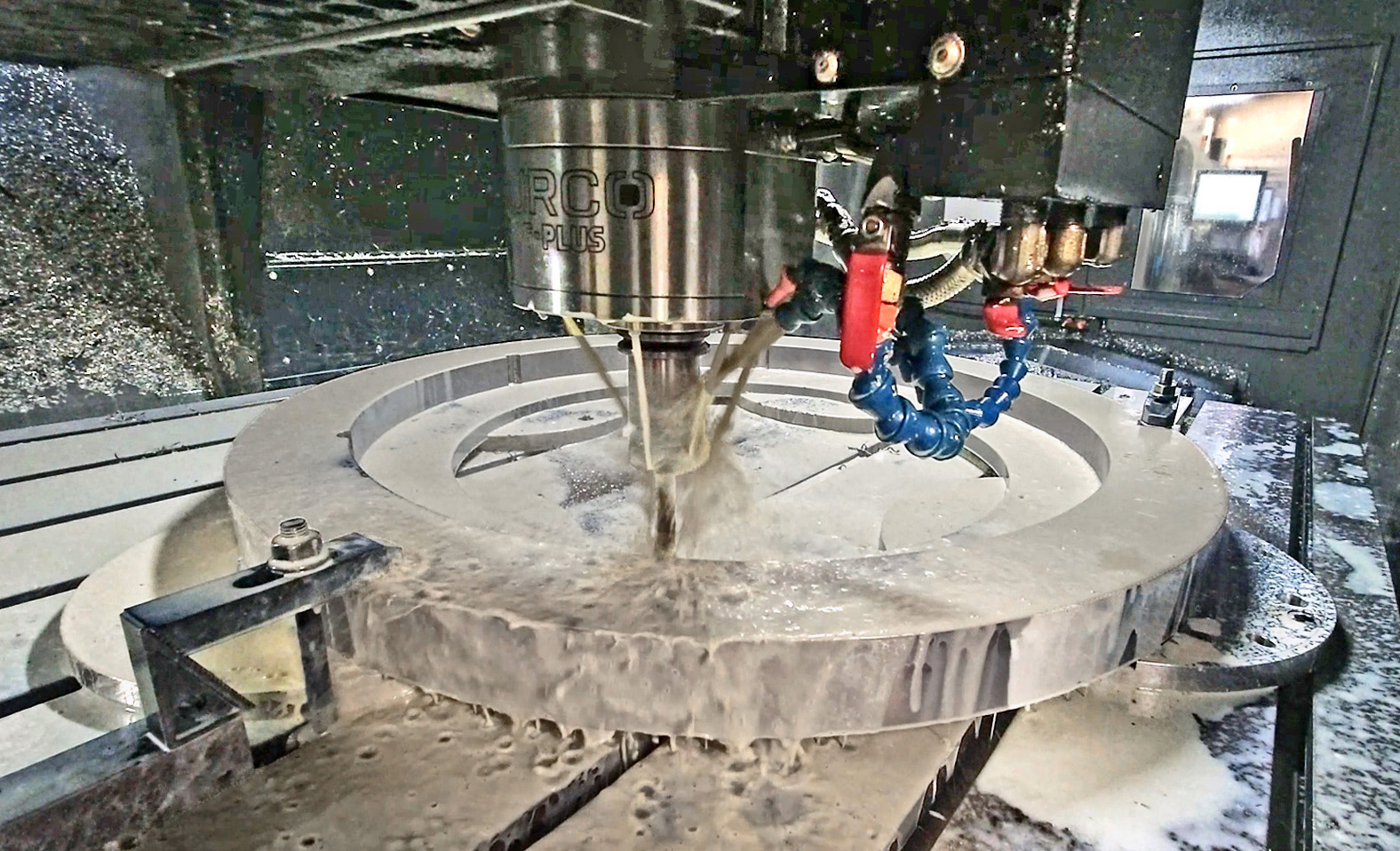
Jones Nuttall Precision Engineering has recently specified a Hurco DCX22i twin-column, bridge-type, VMC with a working volume of 2.2m by 1.7m by 750mm and an eight-tonne table load capacity. This makes the new Hurco the largest item of prismatic machining equipment on the shop floor at the Warrington-based company. The machine is well specified with a 40-station tool magazine, 12,000rpm 18kW spindle and rapids of 32m/min in the X and Y-axes and 24m/min in the Z-axis.
This latest addition to the plant list has considerably expanded the size and range of work the firm can take on. Much of it is carried out by a separate division for Network Rail, London Underground, ScotRail and other well-known names in the rail industry. Repair, overhaul and testing of mechanical/electrical components are a speciality, as well as the manufacture of new components and assemblies to OEM standards and specifications.
Additional prestigious customers include Bombardier, Linde Group and many in the pharmaceutical, energy, oil and gas, petrochemical and defence sectors. Overall, more than 60 employees in the Warrington factory supply more than 30,000 different components to over 250 customers every year. The DCX22i brings to 12 the number of machining centres in use at Jones Nuttall, all of them supplied by Hurco, there being eight VM30i models and other VMCs also in operation. Additionally, a third of the lathes on site are Hurcos, both of them barfed. The TM10 has a 10-inch chuck while the 8-inch chuck TMM8 includes live tooling and a C-axis.
Metals processed include Inconel, titanium alloy, stainless steel, steel, brass, aluminium, copper and even silver. Engineering thermoplastics such as nylon, acetal and PEEK are regularly machined, as well as composites such as Railko, Tufnol, epoxy glass and polyester. Batch sizes range from one-offs to runs over 1,000. Founded in 1971, Jones Nuttall has been dealing with Hurco since 2000, at which time the subcontractor decided to progress from manual tool change mills to machining centres. It opted for Hurco equipment due to the high build quality and spindle power of both the machining centres and lathes.
The manufacturer’s proprietary Max5 control is also a bonus, especially as so many operators are familiar with using it these days. Cutting cycles are prepared quickly using the drop-down, touch-screen menus, which helps ensure economical production if only a few parts are to be produced.
Geoff Brown, a machine operator at Jones Nuttall commented: “Hurco machines are very easy to program, set up and use. The twin-screen control on the DCX helps, as I can program and edit on one screen while the other screen displays the component and toolpath. Programming of all the Hurco machines is the same, so often one operator can run two or three machines.”
The constantly changing demands of the railway industry require Jones Nuttall to adapt accordingly. That is why in addition to subcontract machining the firm has a fabrication department with spot, MIG and TIG welding capabilities, plus arc welding machines, punching equipment and guillotines. Many of the finishing processes are also completed in-house, including shot blasting, powder-coating, painting and varnishing, as well as heat treatment and a range of plating, polishing and anodising processes.