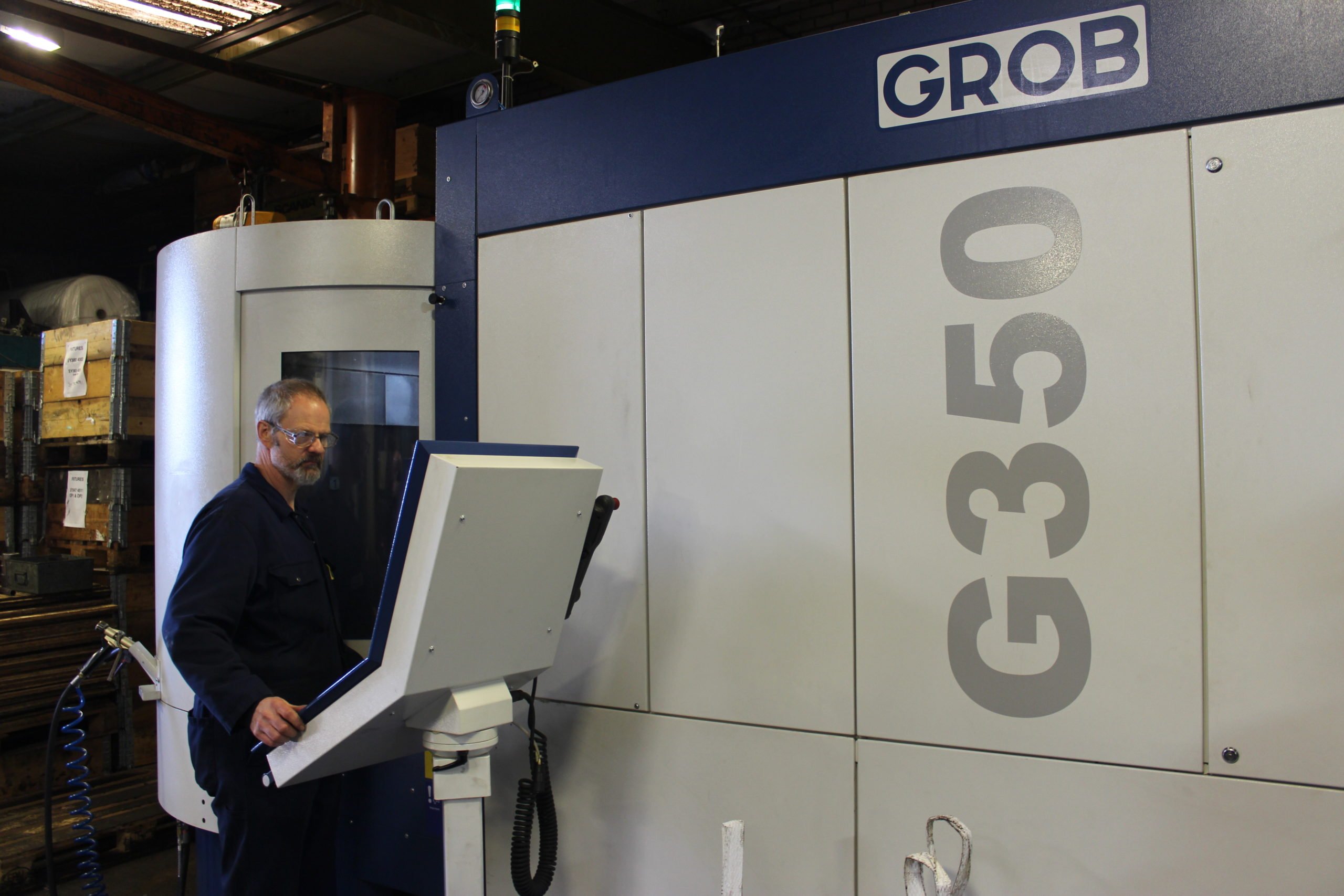
At the start of the new year, Wolverhampton-based Luff Engineering installed a twin-pallet 5-axis GROB G350 machining centre to enhance its capacity and add to its already impressive plant list. However, high-end machine tools require equally capable cutting tool solutions – and this is where ZCC Cutting Tools stepped into the equation. MTDCNC visited Luff Engineering to find out more.
As a subcontracting company that was founded over 15 years ago, Luff Engineering machines a lot of cast iron components for foundries as well as mild steel, stainless, aluminium, acetal and many more material types in small to medium volumes. The workload at Luff is always an interesting mix. Taking a look into the new GROB G350 horizontal machining centre investment, our MTD reporter notices a high feed indexable insert end mill inside the machine. Commenting upon this Luff Engineering’s Mr Jason McDonnell says: “Although we have used other high feed systems in the past, we got in touch with ZCC after watching an MTDCNC video. Dave Wilshire from ZCC kindly called upon us and the result is several ZCC high feed systems on our GROB machine. We have one high feed cutter machining cast iron and another one doing a small EN3B part.”
“From our experience, the ZCC tools are very good. Dave from ZCC came in to see us when I was having a few teething problems and he put me on the right path. Since that day, I still haven’t turned the inserts around in the cutting tool yet. It may be early days, but we have done more than 200 components and the high feed tool has probably done more than 10 hours of machining without an insert index.”
Looking at other experiences with the ZCC cutting tools, Mr McDonnell says: “We also bought a larger high feed system for cast-iron machining, but we haven’t had the opportunity to use this too much yet. Additionally, we have a 32mm diameter end mill system and the cost per edge has been very competitive. The ZCC tools are certainly a premium brand at mainstream prices. The introduction of the few tools that we have bought from ZCC has certainly whetted my appetite to buy more. I’m sure that ZCC will help us reduce our cutting tool costs and cycle times too.”
From an application perspective, Mr McDonnell says: “ZCC has been very knowledgeable, and Dave Wilshire has been very helpful. When you have been machining for a long time, you don’t just go by speeds and feeds – you listen to the sound of the machine as well. When Dave from ZCC came in, he tweaked a few things, and the machine performs better and it sounds better – time will certainly tell how much extra tool life we will get.”
Supporting the performance parameters of the new cutting tools is the dynamics of the new GROB G350 horizontal machining centre. Referring to this, Mr McDonnell states: “I love the high dynamics of the GROB machine, and I always thought the machines would be too expensive to buy, but I was pleasantly surprised when I received the quote. We already have 5-axis machines and horizontal spindle machines, but the facility for the GROB G350 to machine parts upside down enables gravity to take its natural course of action with the swarf. With swarf falling away from the workpiece, we have found that we are not re-cutting our chips and our tool life has improved considerably.” When combining this with the ZCC tools, the West Midlands company is destined to witness impressive results as both the ZCC cutting tools and GROB machining centre become a focal point of production at Luff Engineering.