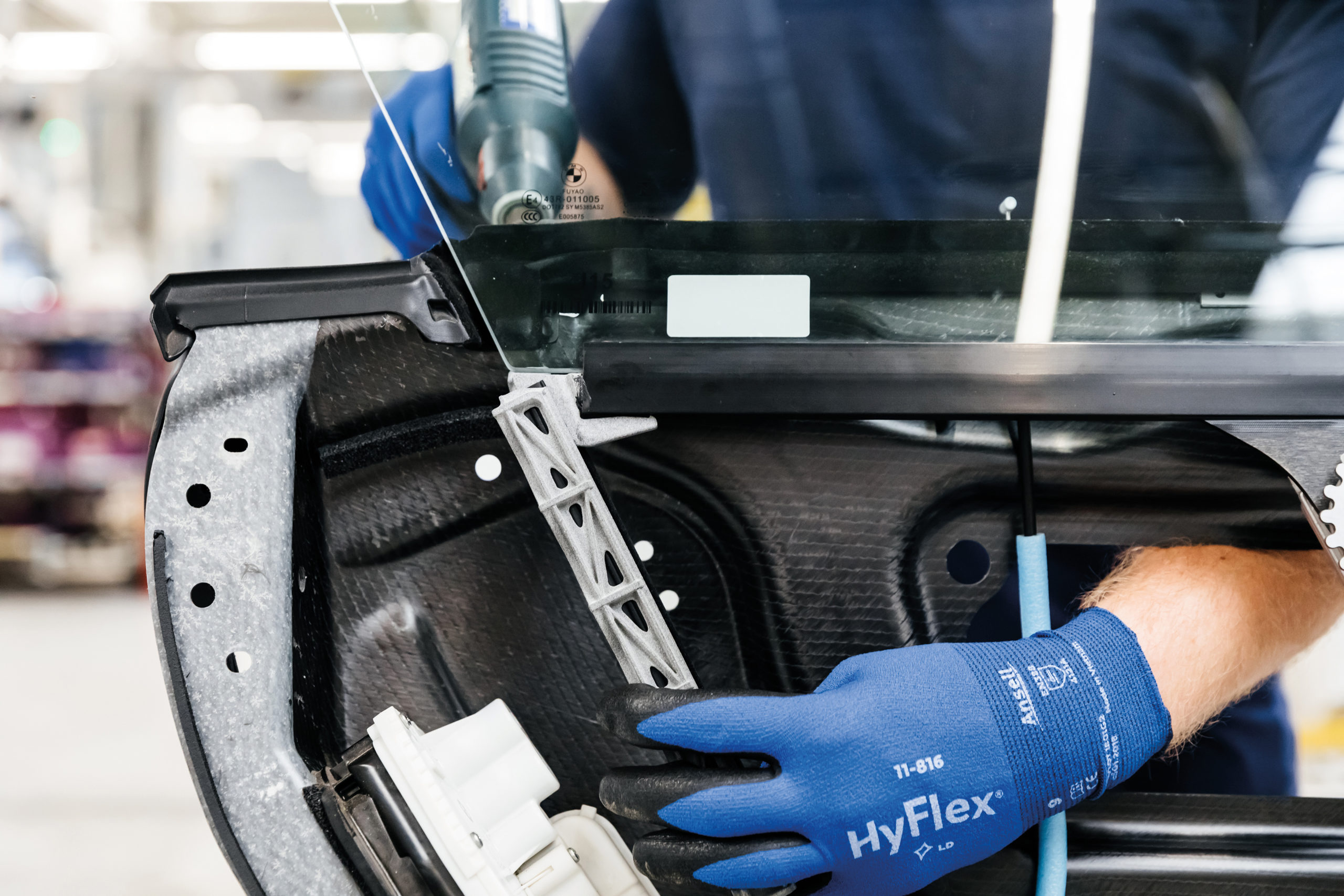
Having been entrenched in 3D printing and additive manufacturing (AM) for over 26 years, Dr Phil Reeves has a wide-ranging expertise and experience of the industry. In the first interview with Tanya Weaver, Phil discussed the barriers to AM; here he reveals adoption trends across various industries as well as discussing machine trends, especially those built for specific applications.
Today the use of additive manufacturing (AM) features in almost every industry. But as Phil Reeves stressed in the first article in this series, before adopting this technology users must consider how it will add value to the business.
“The question manufacturers should be asking is whether by using an AM machine they could cost-effectively redesign their product to give the customer a better product? A better heat exchanger, a better fuel injector, a better part of a pump – whatever that object is the question is whether it can be made better using the AM process and that’s where you get the business value of AM,” says Reeves.
There are industries where AM is creating such value and the one that is leading the pack is aerospace. An aircraft features thousands of parts, some of which are more suitable for the AM process and there is a lot of opportunities to use the technology to create these parts, especially in the engine. “Aircraft engines feature thousands of highly complex and high-value parts that are typically made of very expensive, exotic materials. All of these things play into the hands of 3D printing,” says Reeves.
However, not all parts of the engine are suitable for the AM process. In an engine, there is a hierarchy of complexity from static cold parts, static hot parts, dynamic cold parts to dynamic hot parts. The initial use of AM was for static cold parts, which are metal parts that are typically found on the outside of engines that don’t move and never get hot. For instance, inspection hatches and small manifolds for pumping oil and fuel.
Moving to inside the engine, there are static hot parts, which still don’t move but do get hot. For instance, these could be heat tiles and injector nozzles. Then the dynamic cold parts do move in that they rotate but they’re not at the hot end of the engine. An example is the fan blades produced by GE, which are made of composite but the very tip of them is 3D printed in titanium.
Whilst the three above are suitable for the AM process, there are currently no hot dynamic parts that can be 3D printed as yet. These are parts that are spinning rapidly inside the engine and are getting very hot in the process. Currently, most of these parts are cast using special alloys.
“There is certainly a lot of opportunities to use additive in the production of these parts but always the manufacture has to ask, what value does AM bring and does it improve upon what parts you have already? For instance, with the heat tiles, the reason why AM is used is because the geometry is complex and by creating a part with this design complexity allows for a really good heat transfer across the part. So they’re using the design complexity to make a better heat tile and so the value is through the design,” explains Reeves.
Alongside aerospace is the space industry, which has also been using AM for many years and several additive parts have made their way into space. The advantage of using AM for these applications is that it’s very low volume, incredibly high-value parts that can be optimised to reduce weight, which has a huge impact on a space mission when considering that it costs £20,000 to send just one kilogram into space. “Every satellite that goes into space is rammed full of technology so if AM can be used to reduce the weight of the satellite infrastructure so even more technology can be packed, that is where the value lies,” says Reeves.
Next, is the medical industry, which is also rather established in its use of AM, particularly in the dental industry and for the manufacture of hearing aids, which have been 3D printed for years. “A market that is continually growing is medical implants, for instance – spinal, hips, knees, cranial, facial and so on. With the geometric complexity that can be achieved with AM means that the implant can be personalised for the patient and so offers a better implant,” describes Reeves.
With the automotive industry, although there are many applications that AM could potentially be used for, according to Reeves the economics of using it for part production only really makes sense for high-performance vehicles. For instance, Koenigsegg’s hypercars feature better-performing turbochargers whilst BMW’s i8 hybrid-electric supercar features several 3D printed parts including a fixture for the soft-top that has been printed in aluminium as well as a nylon window guide rail.
“Car manufacturing is the absolute opposite of AM as it’s all about producing parts for the lowest possible cost, and if something can be made in a modular fashion that is then shared among hundreds of different car platforms, all the better. Whereas AM is about low volume, high value and being highly customised,” he says.
The sector that is really grasping the opportunities of AM is the oil and gas and marine industries. The parts needed for both large and small-scale applications from hydraulic systems to thrusters play to AM’s strengths in that they are very low volume, highly complex and high-value parts. “A lot of the equipment used in these marine applications are made from the same alloys that are used in aerospace to make jet engine parts, which makes it easily transferable into oil and gas,” says Reeves.
The last sector is the rail industry, which is also seeing a lot more interest in AM. Taking cues from aerospace, which has been using AM to create low volume parts for its cabin interiors, the rail sector is starting to follow suit. For instance, rolling stock provider Angel Trains has started to 3D print replacement parts for passenger-facing parts on Chiltern Railways train interiors such as grab handles on top of seats. Angel Trains claims that it is currently working on producing more AM parts that are compliant with rail industry standards.
Alongside these industries that are adopting AM, there are now increasingly machines coming to market that are built for specific applications within these industries. “Historically, when the AM industry started, machine manufacturers were producing generic machines as they didn’t know what people were going to use them for other than prototyping. What’s happening now is we’re getting this divergence of machines where there are still generic machines that feature flexible technology but also machines that are dedicated to certain applications,” says Reeves.
An example of this is 3D Systems’ ProJet 6000, which is a specifically designed 3D printer for hearing aid production. Similarly, there are 3D printers that are only used to print dental models, such as dentures. For instance, Formlabs launched Formlabs Dental, a dentistry-centric printer called Form 3b that uses stereolithography (SLA) to create parts – from crowns and bridges to surgical guides, custom mouth guards and dentures – using dental resins.
“Another machine trend is the integration of 3D printers with other machine tools. This means that a CNC machine and an additive machine will be working together. The additive machine will be in a cell with a robot depositing material and the CNC machine will then be machining material. The aim is to make the workflow more automated because at the moment it’s still very manual,” says Reeves.
A machine manufacturer that has launched such an integrated system is Carbon 3D that has launched a 3D printer that integrates with a robot and washing system called Smart Part Washer, which is optimised to speed up post-processing. “It’s really very clever. There is an RFID tag inside the build platform, which the machine reads before it starts building the part. The robot then comes along, reads the RFID tag, takes the part out, knows what part its got, take it to the washing system where the washing system reads the RFID tag, works out how to wash the part, and then the part pops out the end. Then that build platform goes back the machine and it’s all completely integral,” he describes.
But, of course, regardless of the machine being used, it all comes back to the value and business benefits that can be achieved through the use of AM. As Reeves says, machine vendors tend to shout more about their technology but don’t always reveal what the benefit of using it is and the value that it provides to the user.