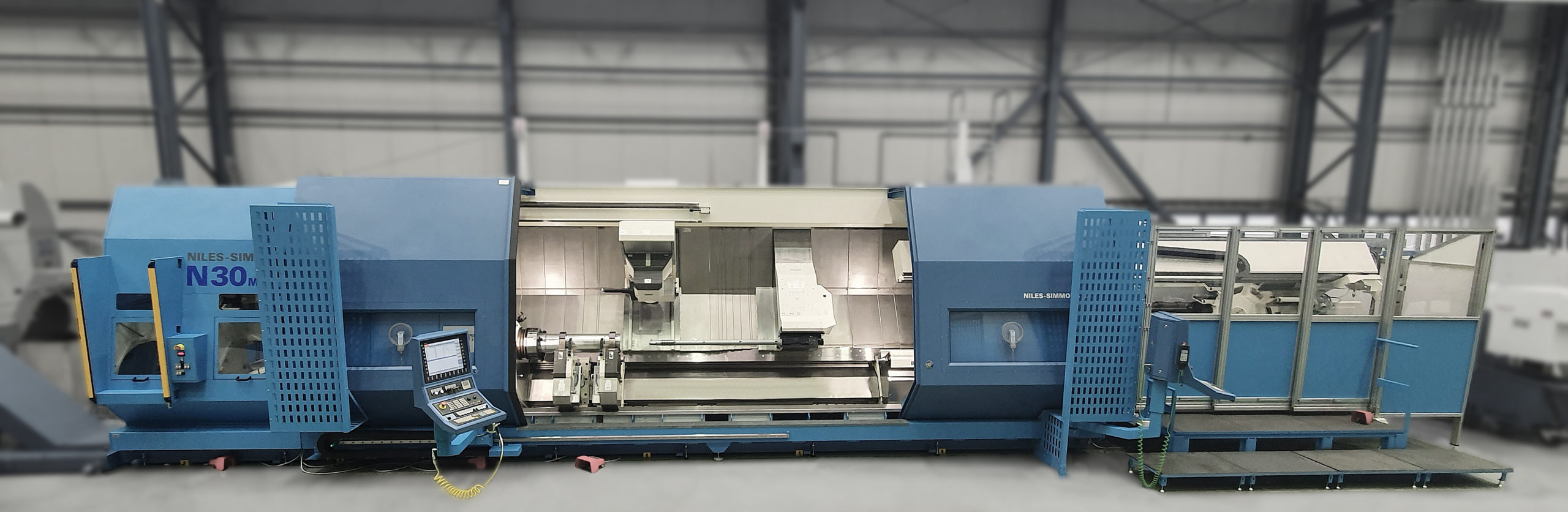
In a world driven by ‘cost-per-part’ production, the demands on complex machining in the aerospace industry is constantly increasing. Niles-Simmons partnered in the UK with McDowell Machining Technologies has developed and introduced its patented and fully automated ‘Center Axis Alignment’ for machining turbine shafts. This technology provides process stability when complete machining complicated, deep hole drilled workpieces and all in-process measurements without manual intervention.
The process aims to exactly adapt the outer contour to the inner contour to achieve uniform wall thickness along the work plane. Suitable for electrically conductive materials from steel through to superalloys and nickel-based alloys, the process is perfect for turbine shafts and other deep-hole drilled parts up to 2m long.
The main advantage is fully automated measurement, alignment and machining of deep-hole drilled workpieces without operator intervention. The process runs within programmed limits and eliminates risky manual operations or error-prone manual measuring processes necessary in conventional machining. This reduces scrap production and improves quality. The integration of all technologies and measuring processes allows cycle times, logistics and handling to be reduced. The measuring method is immune to temperature fluctuations or foreign substances.
This ingenious process is available in the UK from McDowell Machining Technologies and can be conducted on a Niles-Simmons N30MC turning centre purposely configured for this operation with 4.5m between centres and a swing of 780mm. The machine incorporates the main spindle, a turn/mill unit, a boring bar slide, two steady rest slides with a damping unit and adjustable tailstock. The independent tool magazines are available for both the boring bar slide and turn/mill unit. The multi-axis turn/mill unit is located on the main spindle side with 144 tool capacity and to serve the boring bar slide, there are 16 tool positions with a boring bar magazine on the tailstock side. The machine is compatible with boring bars up to 2m long, driven bars, static bars, static boring bars with controllable cutting edges, measuring lances or a cartridge with drive and chuck function. When working in conjunction with the lowerable tailstock that removes the need to retract to a clearance position, the N30MC can machine all types of turbine shafts and eliminates the need for a larger machine.
Capable of turning, milling and drilling to gear hobbing, thread milling and turning, power skiving, 5-axis milling and deep-hole drilling, the machine integrates automated touch probe and optical measurement of tools as well as automatic workpiece probing to attain accuracy greater than 5µm. By integrating all necessary technologies in a single platform, reliable unmanned machining processes can be conducted with complete confidence.
The key feature for shaft centring is the new measuring process. Developed and patented by Niles-Simmons, it uses the eddy current principle to measure the distance between the eddy current sensor and workpiece. This applies non-contact inductive principles to measure through non-conductive materials without influencing the measuring result.
This method is suited for harsh environments by preventing swarf, dirt and cutting fluid from influencing measurement results, any temperature fluctuations are offset by temperature compensation. A special eddy current sensor and evaluation unit from µEpsilon is used to calibrate and measure workpiece-specific properties. This sensor covers a measuring range of up to 9mm with a resolution of less than one micron.
The sensor is mounted at the end of a 2m carbon lance that is integrated into an exchangeable modular measuring cassette. The sensor is positioned using the Z2 & X2 axis and once positioned, the distances between the sensor and the workpiece can be measured at any angle by rotating the workpiece.
The centre point of the measured diameter is calculated from recorded data and any number of centre points can be determined along the longitudinal axis. Knowing the course of the bore, the new centre axis course is calculated to form the basis for machining the new clamping seats of the workpiece to facilitate the new clamping operation. This automated process minimises deviation of the outer contour from the inner contour line to ensure uniform wall thickness.