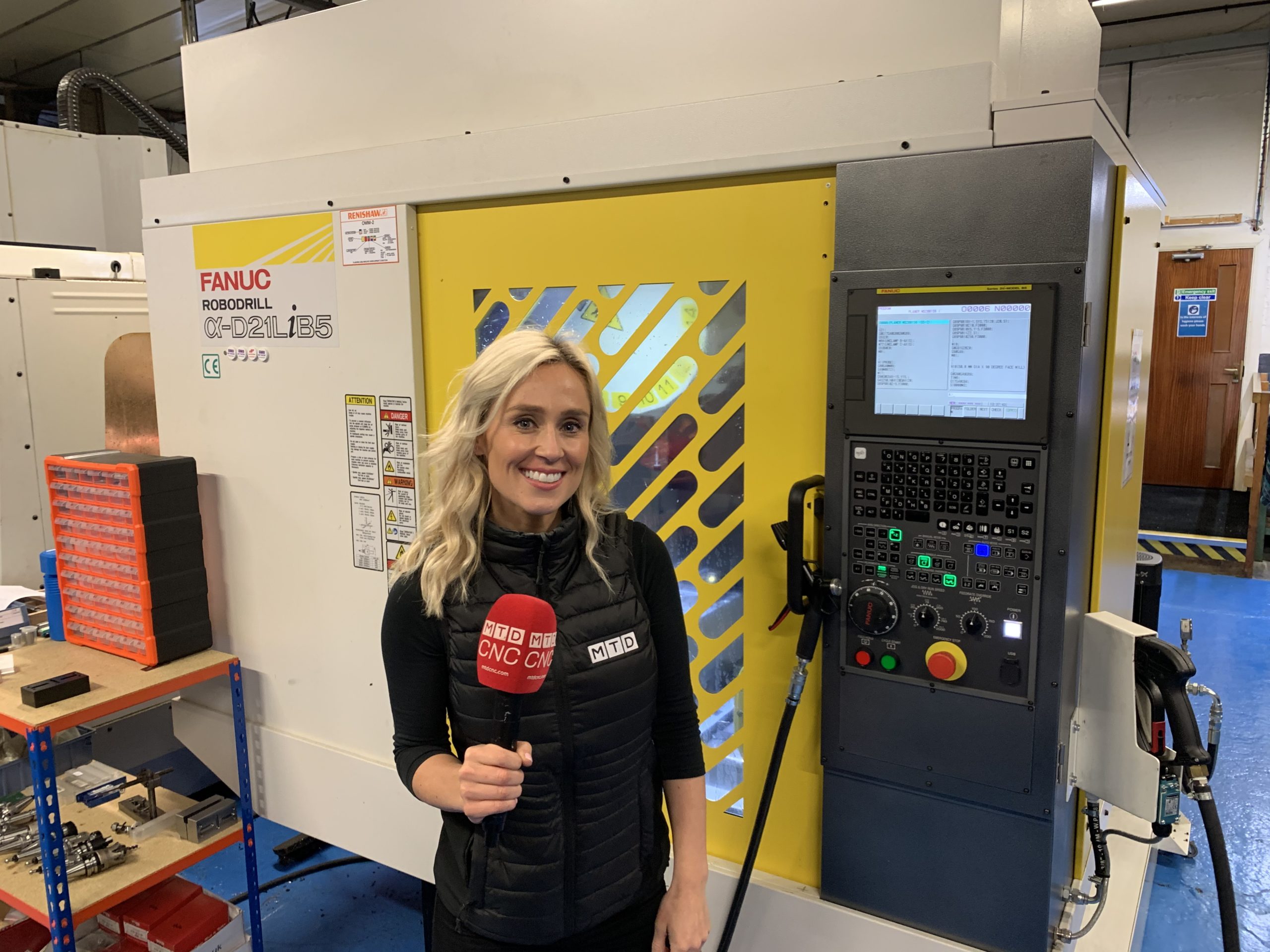
Located in Salisbury, Apsley Precision Engineering Ltd recently installed a new FANUC ROBODRILL D21LiB5 machining centre. MTDCNC travelled to Wiltshire to find out why this subcontract manufacturer with a plant list that includes Miyano, Doosan, XYZ, HAAS, Brother and Matsuura, made the most recent acquisition in a brand that is new to the company.
Established in 1984, Apsley Precision manufactures everything from prototypes to high-volume production for the defence, medical, oil and gas, aerospace and scientific industries. Commenting on why the company purchased the FANUC ROBODRILL, Peter Aymes from Apsley Precision Engineering Ltd says: “We saw the ROBODRILL on the MTD website and it sparked my interest with the high spindle speeds that it can achieve, as we wanted to improve our productivity.”
Looking at why the company invested specifically in the ROBODRILL D21LiB5, Peter says: “It’s got a very large table when compared to some of the other machines that we have. So, it gives us plenty of flexibility on the size of the components that we can run, it has high spindle speeds and we can integrate a 5-axis unit with it as well.”
Alluding to the rigidity of the machine for such a compact machining centre, Peter says: “There are always concerns around BT30 spindle machines being a little ‘lighter duty’ and we do have some other BT 30 machines, which we have had some impressive results on. However, the FANUC ROBODRILL has the BIG PLUS spindle (BBT30) which gives the machine even more rigidity, so we have been able to work the machine particularly hard. We have been machining all types of materials such as plastics and aluminium, which are fairly light-duty and we are getting productivity savings of 30% and more. We have also been machining stainless steel and alloy steels on the machine as well.”
“The machine is so much more than a drill/tap machine, as we can machine pretty much everything we can produce on our BT40 machines without any reduction in productivity or output. If anything, the FANUC is going faster than our other machines. The bulk of our machining is in aluminium and we are getting around 30% savings on aluminium machining. I have gone out to some customers offering them a price improvement, as we have been able to achieve these savings on almost every job that runs on the FANUC ROBODRILL.”
With such high material removal rates, Peter comments upon the chip evacuation of the FANUC ROBODRILL, saying: “It has been very good. We don’t have a swarf management system on the machine but the flood coolant has more than adequately removed all the chips from the work area.”
With a 21 tool carousel, Apsley Precision has machine tools with more tools in the carousel as well as other machines with a similar number of tools to the FANUC. Referring to this, Peter states: “What we find on this machine is that the through coolant spindle means that you don’t have to double-up on tools on the machine. There are also new tooling solutions out there that allow you to cater for two or three operations in a single tool. I am very impressed with the high-speed spindle. The 24,000rpm really gives us an advantage over some of the other machines that we have. The main benefit of this is essentially the cycle time reductions. When comparing a 24,000rpm spindle to 12,000rpm spindle, we may get the same feed per tooth on the cutting tool, but you are doubling how fast you can move around the machine and this shortens the cycle times immediately.”
“We also have conversational programming through the 31i-B5 CNC control unit and that has been very easy to pick up. Additionally, we have a spindle probe on the machine. This provides a massive advantage for setting jobs up, as we can ensure the jobs are always in the right position when we start our programs.”
In conclusion, Peter says: “It’s a great machine with a small footprint. It is very robust, it’s very rigid and it cuts all materials and it is nailing every job we have put on it so far.”