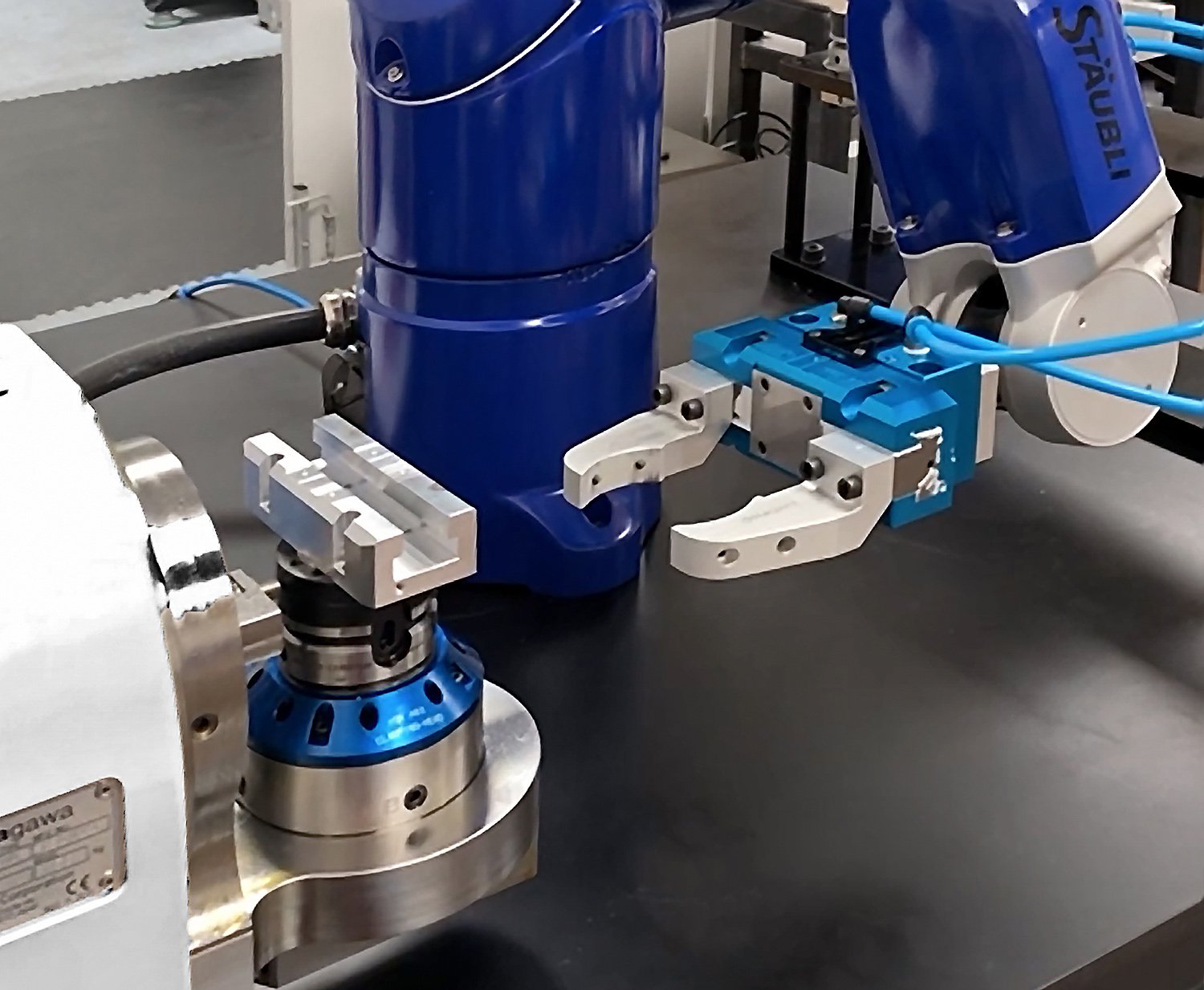
The UK manufacturing sector is behind its competitors in Europe, the US and the Far East when it comes to the introduction of automation in its factories. There is no lack of knowledge, just equipment adoption on the shop floor.
1st Machine Tool Accessories (1st MTA) is a keen advocate of automating machine tools to achieve savings through unattended operation. However, the company stresses that big investment in expensive robotics is not a prerequisite for success in smaller factories. The correct equipment for an application could be as simple as employing hydraulic rather than manual clamping to actuate jaw closure; using a rotary table to add a fourth or fifth axis to a 3-axis machining centre or choosing a full-length bar magazine rather than a short barfeed to automate a lathe.
Whether producing prismatic or rotational components, return on investment (ROI) in such relatively inexpensive automation equipment can be surprisingly rapid. On lathes, for example, there may simply be a need for improved accuracy and repeatability. This can be achieved by upgrading a power chuck or installing a collet chuck. It could also mean using special jaws on a standard chuck or utilising one with non-standard features such as a long jaw stroke.
It could be that a quick-change chuck is more suitable or consideration could be given to a special workholding chuck dedicated to a family of parts. The range of chucks manufactured by Kitagawa covers all of these requirements.
For workholding on vertical or horizontal-spindle machining centres, quick-change systems can be single or multiple and fitted on a rotating axis, allowing multiple sides of one or more components to be accessed by the cutter. Parts can be secured on zero-point plates such as those made by V-Tech. They enable components to be loaded quickly to minimise spindle downtime and maximise productivity.
Multiple clamping arrangements for longer machine running times and less loading times are available from Chick workholding. For use on dedicated 5-axis machining centres, vices from the German company Best are recommended, as they grip on very little material to expose the maximum surface area for milling and drilling in a single cycle.
If an application calls for a magnetic workholding solution, systems are available in various sizes from Walmag, from small, single magnetic plates to large plates covering a complete machine bed. They are equally suitable for securing parts on grinding machines and may also be used for applications other than on machine tools.
If automated clamping is required, one option includes a hydraulically actuated, low-profile workholding solution from Finnish manufacturer OK-VISE. For example, multi-rail clamps are small in size, yet they exert a force up to 150kN and the clamps are designed to fit between workpieces and take little space on the fastening base.
Rotary tables add extra CNC axes
As stated, manufacturers can produce parts cost-effectively with single-hit machining. An additional rotary axis is versatile and can be used horizontally or vertically to provide either a rotational motion or a tilt axis for positioning a part. Options include compound tables to turn a 3-axis VMC into a 5-axis machine, elevated clamping tables, small footprint and high-speed tables, and large through-bore models as well as multi-spindle rotary and tilting tables with accessories for automatic loading. Kitagawa offers all of these options.
The latest range to be introduced is the MK Series, it has two models that add a fourth CNC axis. The larger MK250 has 1,000Nm pneumatically actuated clamping and can support a component or tooling column to a maximum load of 250kg horizontally. If a Kitagawa tail spindle with integral clamp is added for securing the load between centres, clamping torque increases to 1,600Nm.
A turning centre can be automated with a short barfeed, but it may be worth considering replacing it with a full-length bar magazine, as is routinely fitted to a sliding-head lathe. 1st MTA contends that repeatedly feeding short bar into a lathe constantly costs the user money, whereas a more productive, full-length alternative constantly saves money. A quick calculation is sufficient to confirm this.
The ROI on full-length barfeed models is all too often overlooked and substantial savings could be made over a short period by feeding long stock. Lathes equipped with such magazines keep production running for longer unattended periods. Barfeeds manufactured by Iemca are fast to set up when changing the bar size, as they accept a wide range of stock diameters without having to fit another guide channel. The latest Maestro 80 model accepts bar from 10 to 80mm and offers changeover in 30 seconds, minimising loss of production.