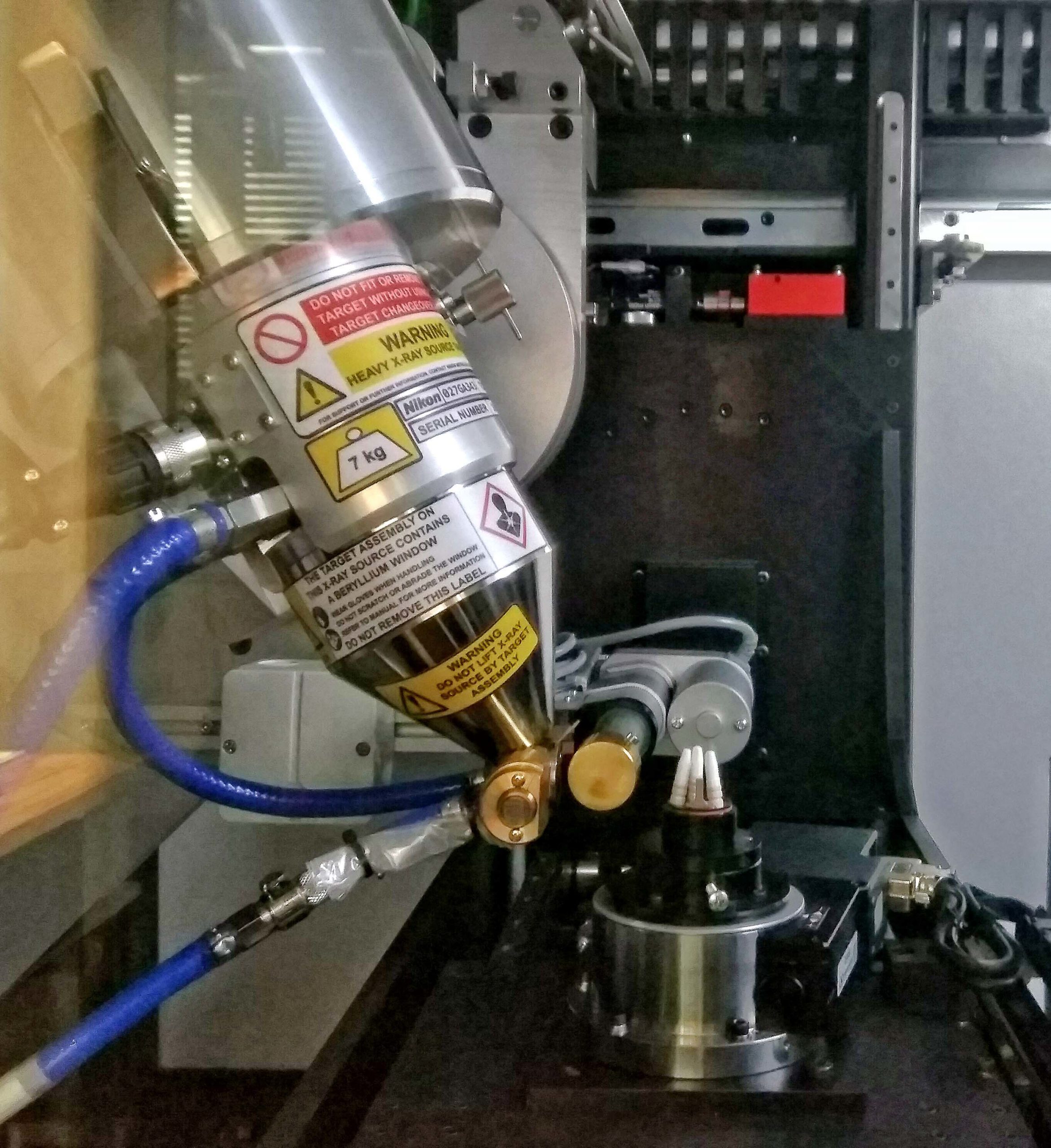
After four years of intensive research, Zürich based Dentalpoint launched a more aesthetic and healthier alternative to the conventional titanium dental implant. The research project led to a biocompatible, metal-free alternative made from ceramic. The ZERAMEX zirconium dioxide two-part implant system includes small and complex features such as internal threads that must undergo extensive inspection to meet dimensional specifications as well as product traceability in compliance with medical device regulations.
Quality control was proving difficult and time-consuming on a CMM, so in 2018, the company invested in an alternative process based on an X-ray computer tomography (CT) system from Nikon Metrology and an inbuilt robotic loading system. The benefits have been enormous.
Not only has the speed of operation and a high degree of automation supported volume production, but it has supported the company right back to the research and development phase of new products. Dentalpoint is considered to have a 3 to 4 year lead in the development of ceramic implants that fully match the attributes of top-end titanium varieties. It manufactures ZERAMEX implants and related ceramic parts at its production centre in Zürich using special technology to process the extremely hard zirconium dioxide.
Benjamin Bernet, the firm’s R&D Project Manager said: “As a certified medical device manufacturer, we are responsible for the quality control of all implants and must make sure that stringent regulations and standards of medical devices are met.”
“Dimensional control of all the products we manufacture is crucial. Our previous production partners mainly used a CMM with a touch probe to take various point measurements of the outer implant geometry as well as the whole inner connection that acts as a counterpart for the screw and the abutment. In contrast, our new in-house production line relies on an automated Nikon Metrology XT H225 ST CT system to control quality more comprehensively through 100% inspection of almost every feature and dimension, despite their small size.”
One of the main issues with the previous metrology method was the lower accuracy with which features could be measured. This was especially the case for small inner geometries such as deep holes and internal threads. Moreover, measurements were often limited to points and 2D paths, as more detailed measurements were very time-consuming. Additionally, there was no possibility over a long period to reanalyse measured parts after delivery or re-assess the patient, as only some datapoints were stored and no point clouds were available for checking 3D surfaces.
The latter restriction was one of the most important reasons for investing in the new CT equipment, according to Mr Bernet, as well as the ability to set up an automated workflow to achieve high inspection productivity and the opportunity to introduce the cobot loading of a full batch of parts into the CT cabinet. The measuring cycle involves the cobot sequentially picking up multiple implants mounted in a plastic (PEEK) holder, transferring it onto the manipulator and after scanning is complete, returning the components to the rack from where they came. The CT machine runs almost 24/7, typically measuring up to 500 implants in 24 hours, with full traceability.
Only one clamping is required for CT scanning, unlike with the previous CMM inspection method. Additionally, all parts are held in identical fixtures that are repeatedly reused. During the subsequent analysis of the data scan, the PEEK vanishes due to the large difference between its density and hence linear attenuation coefficient compared with those of ceramic. A further advantage of the CT measuring cell is its low operating cost. This is credit to the automated cobot loading and the concurrent, fully independent reconstruction of the previous X-ray data, registration, fitting and reporting. Since the process is stable and the CT runs as expected, there is no need for service, maintenance or support. The cell and its software can be configured with scan profiles for simplicity of use by operators. Final reports are easy to interpret and data can be handled with little effort, with part-to-CAD comparison available for detecting tolerance errors and geometric anomalies. Single result files can be generated for a complete batch within the measurement protocol. The acquired metrology data is used to support the mandatory requirements with regards to lot traceability of measurements and also by production line operators to set up machinery and manufacturing parameters. The ability of CT to investigate the interior volume of parts non-destructively means that further analysis could be carried out in the future using the data, such as checking for internal defects or cracks. Mr Bernet is also of the opinion that another huge and often underestimated benefit of X-ray CT is that it can be used in R&D for material research and analysis, failure analysis and functional relationship analysis of assemblies. Furthermore, CT could assist in the development of new implants and tools, open up new horizons and overcome the limitations of new designs.
Mr Bernet concluded: “We opted to invest in the CT inspection solution from Nikon Metrology because the supplier was able to demonstrate the feasibility of its system for fast, effective scanning of our products. This is coupled with comprehensive reporting of results. The final implementation of the process workflow is highly stable and functional. The full 3D data is used to measure features in detail and is stored for traceability. High accuracy is achieved by calibrating the device to a specific scan position, leading to very small measurement errors below one micron when tested on a reference sphere. The installation was efficient and the training, service and helpline are very professional and helpful. In particular, we received great support from Nikon Metrology’s application engineers in developing the process.”