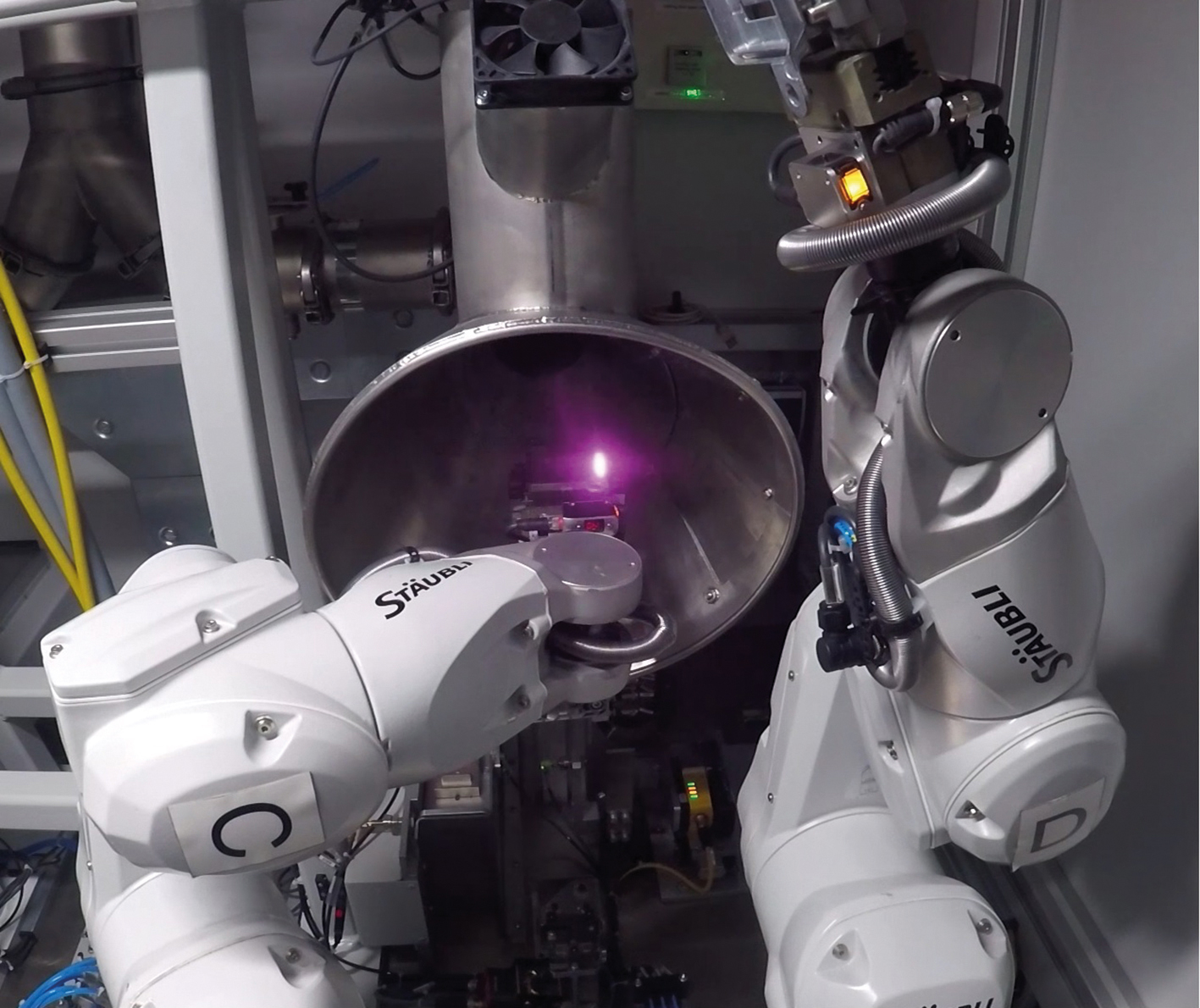
For the implementation of a new laser cleaning process, Vitesco Technologies, formerly the Powertrain Division of Continental was looking for a measuring device to monitor the performance and quality of laser processing in series production. The automotive supplier found a solution with the Bruker Alicona 3D measuring system. In addition to 3D topography measurement, the system offers a new classification software that based on AI, automatically detects ‘OK’ and ‘not OK’ surfaces.
The core of every vehicle is its powertrain system and Vitesco undertakes specialised production of modern powertrain technologies for clean and sustainable mobility. Reducing nitrogen emissions (NOx) can be achieved through intelligent solutions in exhaust gas after-treatment and this also includes the development of NOx exhaust gas sensors that pass through critical process steps in production. A critical step is the cleaning process where a surface is processed using pulsed laser radiation and thus prepared for the following cycles.
‘Technical Cleanliness’ is the area of expertise of Hermann Hämmerl, Senior Process Engineer in the Central Manufacturing Technologies department and he coordinates process development for new technologies through to their introduction in the German automotive supplier’s worldwide network of plants. This also includes ‘searching for methods that allow the process results to be verified.’
In this specific case, Hämmerl was responsible for implementing a new laser cleaning process that is intended to prepare die-cast surfaces for subsequent bonding to the electronics housing of a NOx exhaust gas sensor. The surface produced by laser, has an influence on the durability of the bonding, and 3D measurement technology should help to ensure the long-term function of the sensor in-vehicle operation. In the search for the right measuring method in this newly introduced process, it became apparent there were no suitable measurement methods known for use in production. Eventually, the company found what they were looking for in a Bruker Alicona 3D measuring device with its 3D depth measurement that offers a surface classification software to automatically distinguish between ‘OK’ and ‘not OK’ surfaces.
Detection of smallest surface differences
Even minimal fluctuations in laser processing lead to the smallest changes in the micro surface quality of a die-cast surface. These can have a critical influence on the durability of bonding. In the evaluation of various measuring devices, great importance was therefore attached to the ability to detect even very small differences in roughness. In this way, it can be verified whether specified tolerances are maintained even if process changes are made. Conventional profile-based methods could not sufficiently quantify the specific roughness of the die-cast surface, so Vitesco switched to optical metrology for this application and today uses Bruker Alicona’s technology in series production. The InfiniteFocusSL measuring system detects even the smallest differences in the roughness of the laser-treated die casting surface. Therefore, deviations in the laser cleaning process can be detected quickly and it is possible to react promptly with system parameter adjustments.
Automatic recognition whether ‘OK’ or ‘not OK’
The measuring system offers a further benefit which contributes significantly to the efficiency of the entire process chain. The automation option is based on AI, which automatically distinguishes an ‘OK’ surface from a ‘not OK’ surface. The corresponding evaluation is based on a combination of 2D texture data and 3D topography data, which are analysed during the inspection process. Using a so-called classifier, both positive and negative examples ‘golden samples’ are trained to the measuring system or classification software, which enables the automatic detection of ‘OK’ and ‘not OK’ die-cast parts in near-series monitoring.
The ‘production-suitable’ measuring is robust and offers measuring speed and repeatability for use in production. Additionally, there is a measuring sequence that enables every operator in production to measure without having specific knowledge of the measuring system. Automation is a future-oriented keyword at Vitesco Technologies. Vitesco has already evaluated other Bruker Alicona measuring equipment and it has become apparent that Cobots can be used in the future without restrictions.