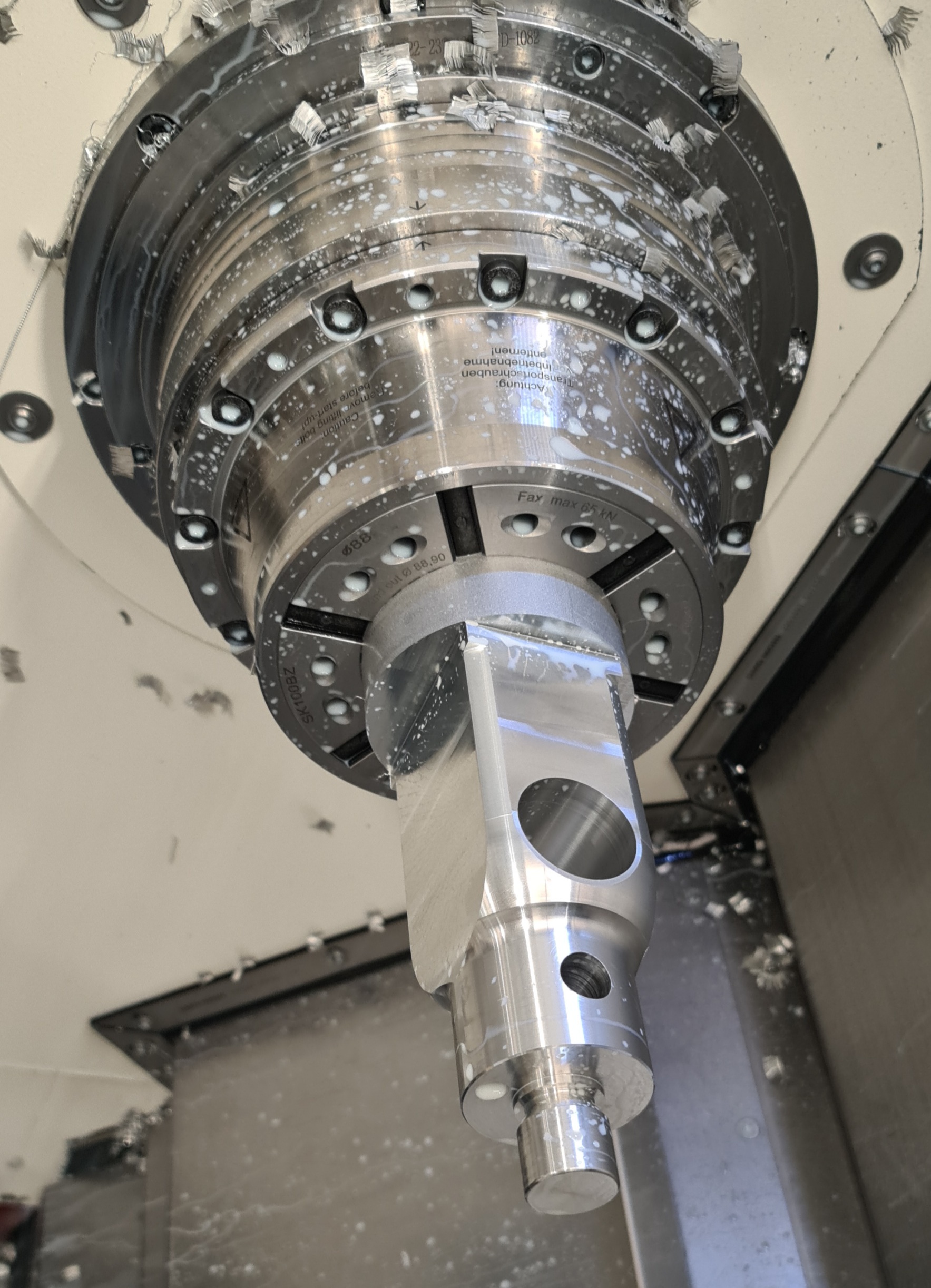
Like all subcontract manufacturers, Milturn Precision Engineering Ltd has to deal with the market pressures of being cost-competitive and having the ability to get high-quality parts out of the door. Claiming to be one of the UK’s first companies to achieve ISO: 9001 – 2015, quality has always been at the forefront for Milturn, but to balance quality and productivity, the subcontractor has just invested in a complete manufacturing cell that centres around a DMG MORI CTX beta 1250TC turn/mill centre. MTD went along to find out more…
Milturn is a subcontractor that has a comprehensive plant list, its own anodising plant and TAG Quality systems that have been in place for more than a decade. The result is a company that serves a wide variety of industries with quality components delivered on time with the versatility to undertake the manufacture of everything from prototypes to batch work. However, the company recently found itself under increasing capacity pressure – this issue was somewhat compounded by a monthly order of 60 aluminium movie lens components that required almost one hour of machining per part. Whilst the one hour of machining time wasn’t an issue, the three turning and three milling operations with a set-up time of 6 hours was an issue. Also, an issue was that with 30 holes tapped at M1.6 to M2.5, there were occasional tap breakages that would result in the scrapping of a part.
Reviewing the marketplace, the solution was to invest in a manufacturing cell with a DMG MORI CTX beta 1250TC turning centre at the heart of it. The cell with the DMG integrated Automation Station provides robot loading and unloading as well as a tray for storing billets and finished parts whilst a barfeed sits at the rear of the machine for parts that are suited to barfeeding. This immediately resolved the situation, taking the process from six operations to one.
Commenting up the purchase of the DMG MORI cell and the situation that instigated the purchase, Milturn’s Development Engineer, Mr Daniel Rushton says: “The long-term customer has a consistent order for the 60 Cine lens components per month, which is part of circa 2500 parts produced monthly for them. As a complex part with six operations on various machines, this extra demand was absorbing more of our capacity and time – we approached a number of machine tool vendors, but DMG MORI were the one that stepped up with the perfect solution. We supplied DMG MORI with billets, drawings and our requirements and they engineered a fully automated solution.”
The DMG MORI CTX beta 1250TC turning centre incorporates a powerful yet compact 20,000rpm HSK milling spindle, linear scales, an 80-tool carousel, liquid-cooled spindles and axes plus 1470mm between centres. The entire cell also incorporates the DMG MORI robotic loading and unloading station, a Hydrafeed barfeeding system and a 5S lean manufacturing environment from Hoffmann that completes the cell. For those of us less familiar with the acronyms and methodologies, 5S incorporates five core steps – sort, set in order, shine, standardise and sustain. Inside the work area resides a SMW chuck with gripper jaws on the main spindle for clamping billets. The DMG MORI robot transfers parts from op one on the main spindle to op two on the sub-spindle where a Hainbuch expanding mandrel clamps the internal diameter for finish machining. Milturn has even invested in the Hirt-Line series of coolant hoses from Floyd Automatic Tooling that are manufactured from stainless steel, proving extremely rigid and robust for ‘lights-out’ production.
The new cell has only been installed for a matter of months, but it has proven transformative for the Hinckley based business. In the first 8-weeks since the DMG MORI turn/mill solution arrived, Milturn had not changed its finishing inserts in its cutting tools. This was down to several factors. Firstly, Milturn had opted to change its cutting tool supplier to Hoffmann with the cutting tool integrator providing all cutting tools for the lens project. Secondly, the process stability of the DMG MORI machine with rigid toolholding set-ups provides the platform for improved machining performance.
Highlighting this, Daniel continues: “The DMG machine allows us to approach each process differently. For example, with a more stable set-up, we can threadmill the 30 holes that are either M1.6 or M2 in each lens part without breaking a tap. Previously, we would break a tap on every batch of parts and it was easier to scrap the part than spark EDM the broken tap from the part, re-set and re-machine it. From a general tooling perspective, we can only hit particular features of the lens part so hard, as much of the machining is around thin-wall areas. On finishing cycles the tool life has increased hugely – in fact, some of our finish turning inserts had not been turned around in the first couple of months of machining. Hoffmann has not only provided a complete suite of high-quality thread mills, drills, turning and milling tools – they also helped with the 5S system with storage solutions that makes every tool easily accessible for the operator.”
The Hoffmann 5S system that was designed by Milturn is an integral component in the cell. It includes all the cutting tools, tool holders and shrink-fit holders with HSK63 back-ends, the shrink fit system, tool pre-setters and even the metrology equipment that are all organised in an efficient flow-based system with cabinets and drawer units for storage. Prior to the installation of the cell, machinists at Milturn would have had to have taken components not only from one machine to another but also to the inspection department in between each process. Take into account the multitude of cutting tools used on various machines – and the time savings outside the machine are evident.
Improved Productivity
With the thin-walled complex aluminium lens component, the DMG MORI CTX has reduced the cycle time from around 50+minutes per part to 45minutes. However, the overall cycle time was never the primary focus of the cell. As Daniel continues: “For us, this project was about reducing the six hours of set-up time and the capacity the job was absorbing throughout the machine shop. We have now consolidated this capacity into a single machine, freeing up capacity throughout the machine shop and eliminating long set-up times. The parts are now made in one hit on the DMG machine, which also improves process reliability. We have a lot of features that have to be within +/-6 or 7 microns and the concentricity on the thin-walled areas has tight tolerances too. This part is all about one-hit machining with high precision.
Of course, another key factor is the automation capabilities of the cell. “Instead of tying up multiple machines, the DMG MORI CTX can now process the parts around the clock. We can load up to 24 of the 4 3/4-inch diameter aluminium billets on the automation table and the robot will automatically collect a billet, load the machine and unload when the part is complete. This provides up to 18 hours of unmanned machining, which significantly reduces our lead-times on the lens parts.”
What’s next?
The cell now turns the batch of optical parts out in a matter of days not weeks, giving Milturn capacity throughout the workshop as well as on its new investment. Commenting upon this, Daniel continues: “This lens component is just one of a family of parts and with the added capacity and capability, we can offer the customer the capacity to take on all the other parts. We have already taken on work from new customers that we may have previously turned away. We have just taken on a project to machine more than 200 complex parts for a new customer that wanted to re-shore work from overseas. With a cycle time of more than 2 hours per part, we have successfully machined the first batch of parts and we are now in line for more work from this company. This highlights how the capabilities of the DMG machine coupled with its automation is giving us the ability to machine all types of challenging parts with unmanned efficiency. We haven’t found a part that we couldn’t make on this machine yet.”
“As well as looking for more complex work to take on, the next step in our strategy is to re-engineer existing legacy work to produce the parts faster to reduce lead times, costs and increase capacity for our existing customers and potential new ones,” concludes Daniel.