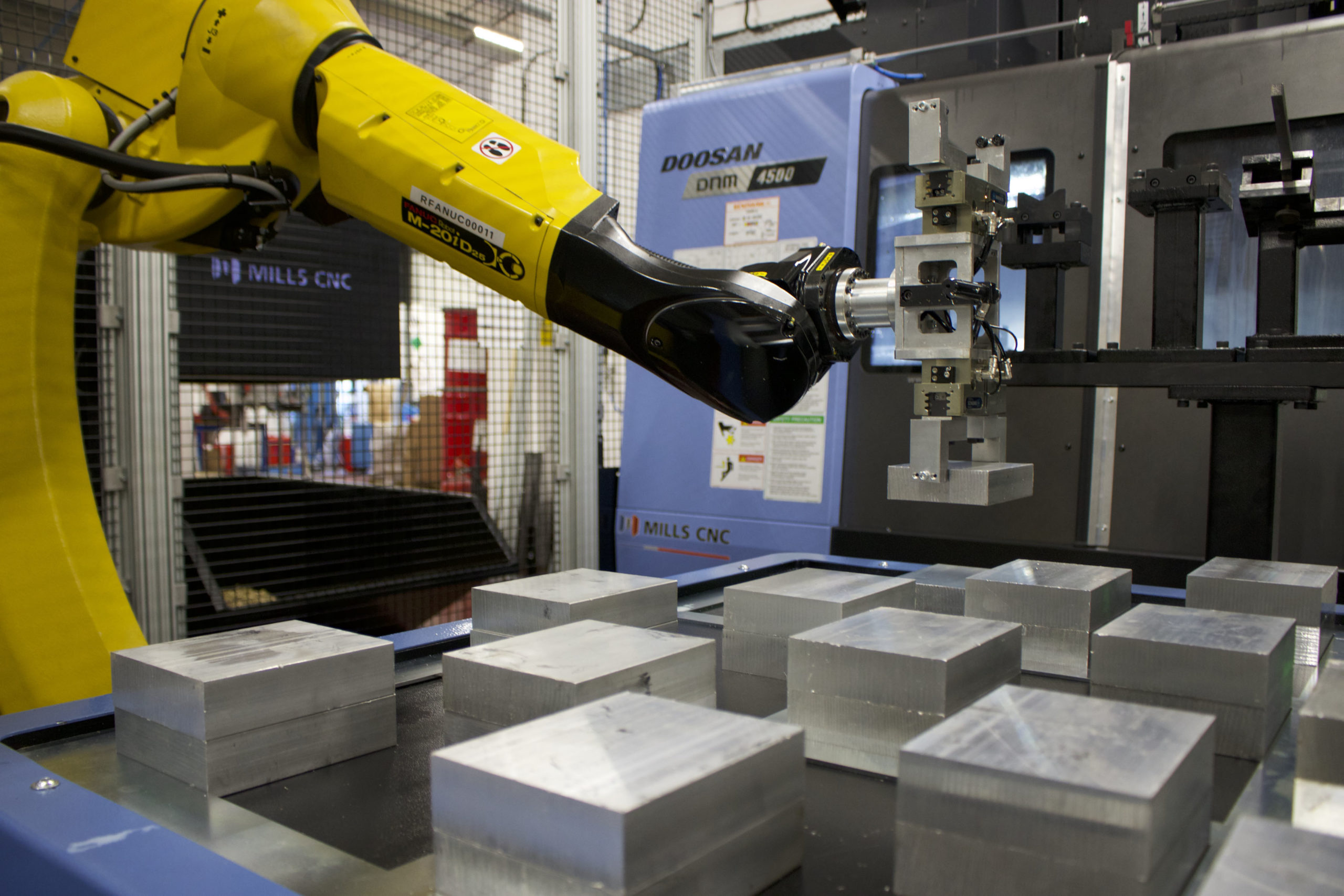
Growth in global demand for its fire protection and fire suppression systems has driven Ardent to invest in a highly customised automated manufacturing cell.
Mills CNC, the distributor of DN Solutions machine tools has recently supplied Ardent Ltd with a cell, installed at Ardent’s facility in Roecliffe, which comprises a Puma 2600SY II multi-tasking sub-spindle, Y-axis lathe and a DNM 4500 high-performance 3-axis VMC integrated with a SYNERGi Sprint robotic automation system.
Since its installation, the cell has been used to machine a range of high-precision, complex components used in the company’s fire suppression systems. These components include brass BSP and Jig valves, supplied as blanks, that is machined in batches using both the Puma lathe and DNM machining centre – and batch-machined aluminium enclosures, machined from solid, on the DNM 4500.
Although the cell was installed in May, its development began several months earlier when worldwide COVID restrictions were being lifted and business was returning to pre-pandemic levels. Explains Paul Newton, Ardent’s Production Manager: “Although the pandemic did hit several sectors where our fire suppression systems and solutions are used, we were confident that it was only a matter of time before they ‘bounced back’. This, combined with a dramatic increase in demand from a growing number of mining customers, located primarily in Africa, who use heavy-duty excavators, bulldozers, loaders and crushers resulted in us reviewing the capacity and capabilities of our operations.”
Ardent’s existing machining resources comprised a Puma 2600SY lathe and a VMC. Operating, in effect, as standalone machines the company’s valve components were first machined on the lathe before being manually transferred to the machining centre for finishing.
Although the process worked it was not as efficient as it could be. The over-reliance on manual intervention was costly and created ‘dead time’, increased overall part cycle times and the cost per part. It was a similar situation with the machining of the enclosures, with machine shop staff having to be on hand to load and unload the parts manually.
The automation requirement
Focused on ramping up the machining of its valves and enclosures, Ardent required an automation solution to achieve unattended, lights-out production. The new automation cell comprises a new Puma 2600SY lathe and a DNM 4500 VMC. The automation element is provided by a heavily customised SYNERGi Sprint system comprising a Fanuc industrial robot and a grid plate to hold the brass blanks and aluminium billets. A robot linear rail, running between the Puma lathe and the DNM machining centre, enables the robot to service both machines.
Says Paul Newton: “As required, the cell is inherently flexible. “The Puma lathe, for example, is an integral part of the cell when machining our valve components but can also operate independently as a standalone chucking or bar-fed turning centre when the cell is being used to machine enclosures.”
The cell enables Ardent to either machine 63 valves or 12 enclosures at a time with minimal human intervention and is a significant improvement over what the company’s previous machining methods could produce.