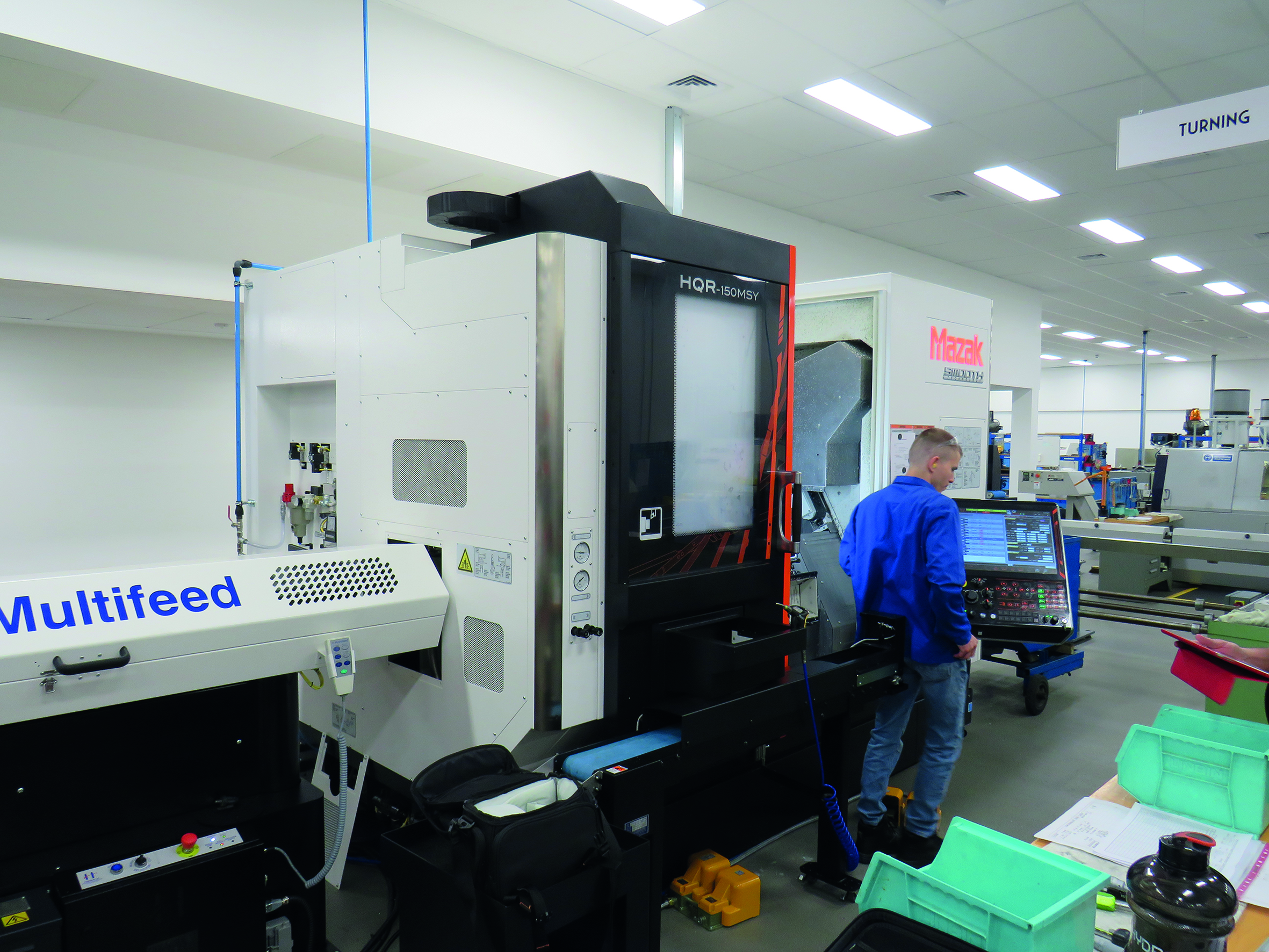
The humble beginnings of Vision Engineering date back to 1958 when Jaguar Racing Team mechanic Rob Freeman developed a borescope for internal inspection of race engine components without the need for disassembly. He subsequently formed the Woking-based company to pursue his interest in optics applied to manufacturing technology.
Wind forward more than 50 years and the company that started off as a specialist optical subcontractor to companies like Rolls-Royce, Vickers and GEC, now employs more than 220 people in the UK, Europe, North America and Asia supplying stereo inspection and optical measurement products around the world. In 2018, the company opened an 84,000sq/ft manufacturing and R&D facility in Surrey and this site is crammed with the latest machine tool innovations that are used for manufacturing its own products as well as offering a subcontract machining service. With machines from Mazak, Kitamura, FANUC, XYZ and Citizen, the finished parts are inspected on Aberlink metrology equipment.
[inlineVideo link=”https://mtd.network/news/mazak-quadrex-wow”]
Speaking about the latest addition, a new Mazak Hyper Quadrex HQR-150MSY, Vision Engineering’s Steve Mead says: “The latest machine we have is the Mazak Hyper Quadrex turning centre. It’s a fantastic machine and it’s given us loads of extra capacity. It has a front loader and a back loader, it can run 16 to 18 hours a day and parts are very accurate; we are really pleased with it.” Referring to the automation of the machine, Steve says: “The machine has a Hydrafeed barfeed unit at one end and the parts catcher at the other end. We wanted a bespoke parts catcher, as we run the machine for so many hours and we have more than one size component go through the machine. Some of the parts and the runs are too large to fit in one container, so we had a device fitted that has an automatic shutter that would crossover to drop parts into the second bin when the first is full.”
Taking a closer look at the machine, MTD spoke with the Mazak Hyper Quadrex operator, Mr Zoltan Bors, he told MTD: “This machine is a twin-spindle double turret machine that works on the X, Y, Z, and C-axes, and it has the latest Smooth control system, which is particularly easy and functional to use. With the Hydrafeed barfeeder, a 5-inch chuck capacity and a bespoke part catcher system, the machine is geared for around-the-clock machining.”
Referring to the flexibility of the machine, Zoltan says: “To demonstrate the flexibility of the Mazak machine, we have a small part here that used to be done on the sliding head machines. It consists of turning, milling and internal and external threading with a 0.5mm pitch, and next to this, we have a larger part that is essentially a milling job. Using the chuck transfer, we can hold our position from front face machining to rear face machining, which is essential, as there are a lot of features that are all tied up to tight tolerances.”
With a bar capacity of 65mm diameter, the bar fed Hyper Quadrex is the epitome of productivity and flexibility, offering simultaneous cutting of two workpieces on front and rear spindles to double productivity for end-users. Incorporating a lower tooling turret with 12 tool capacity and another turret with an additional 12 tool capacity, the flexibility of this machine was a key factor in Vision Engineering making the acquisition. Complementing the flexibility of the machine is a powerful 15kW spindle motor and a work envelope that provides up to 175mm X-axis travel and 580mm in the Z-axis with a 320mm maximum swing.
Mazak installation is the move of a visionary
0:00 / NaN:NaN