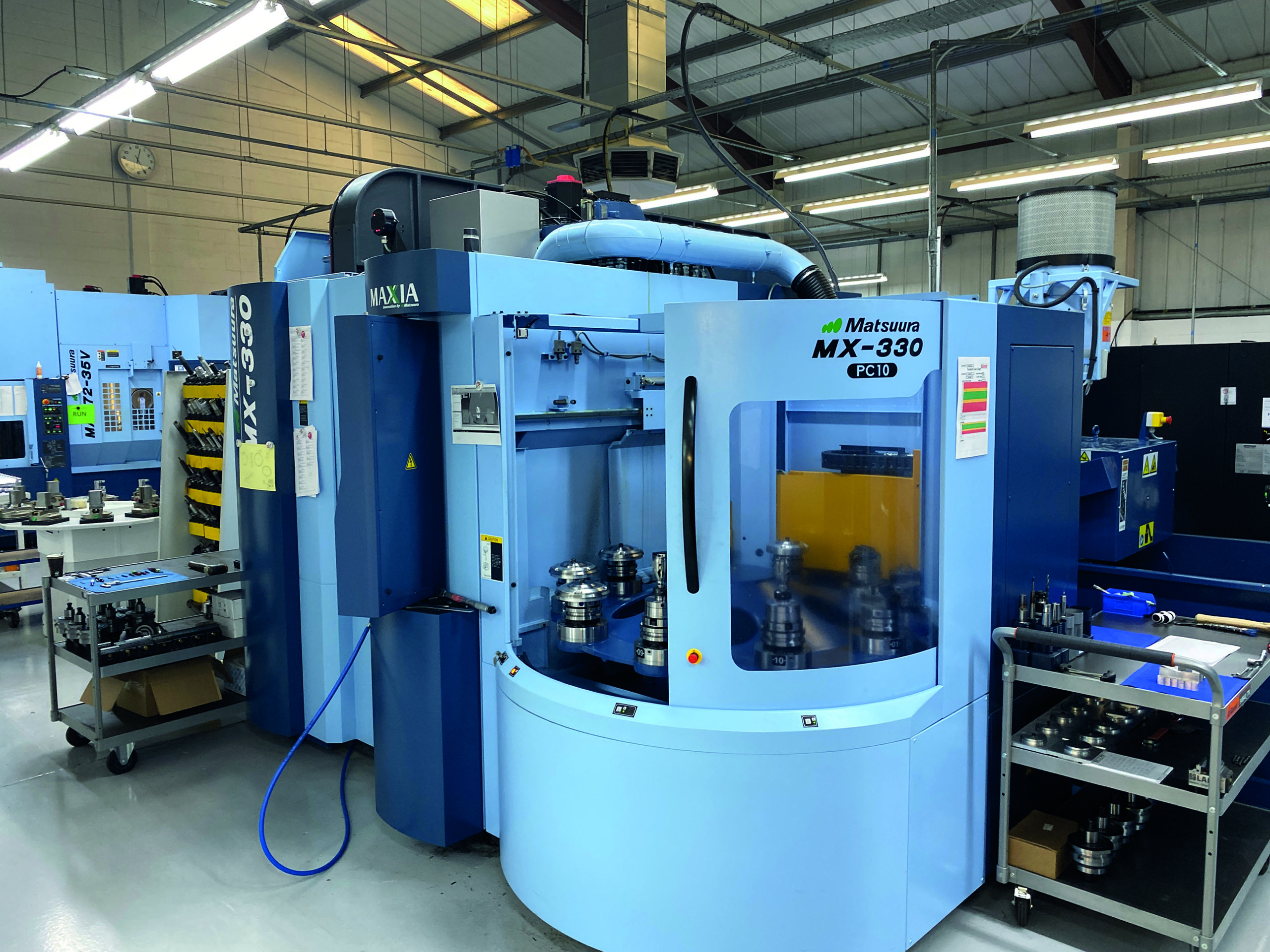
When MP Engineering (UK) Ltd opened its doors for business in 1981, the Leicestershire company was initially set up as a toolroom. In the 1990’s the company evolved to CNC machining and that is when the focus shifted to high-quality machined components in a short lead time. Almost 30 years later, the philosophy of being agile, fast and having the capability to machine complex parts is still in place – something that sets this company apart from its rivals.
With a customer base that boasts world-renowned aerospace and motorsport brands such as Ricardo, Royal Enfield, AMG Motorsport, Rolls-Royce, Safran, Ferrari and many more, the 40 employee company based in Hinckley has invested in high-end machine tools from companies like Matsuura, DMG MORI, Bridgeport, Doosan, Haas, Mazak and Colchester. The latest spending spree has included four Matsuura MX330 PC10 machines in the last two years, which is adding to the 5-axis MAM72-35V 32 pallet machines already on site.
Son of the company founder and the current Production Director, Mr Jason Poole told MTD magazine: “In the last eight years, we have been using the MAM machining centres and they really took our business to a different level. The machines gave us a shift that wasn’t there before. We were previously running a 10-hour day shift, the MAM72-35V machines now run all night long. We are witnessing upwards of 90% spindle uptime.”
“We are producing highly complex 5-axis components that are down to micron precision levels. The Matsuura machines have refrigeration units that enable us to maintain these tight tolerances around the clock. Rather than have one man running one machine or a number of machines, the way we operate here is that each programmer/operator will take the model from the customer and then program that on our CAM package. From there, the operator will own that job all the way through to getting the finished component off the machine,” says Mr Poole.
With regards to lights out running, Mr Poole says: “We have CCTV cameras, this allows the programmers to have a look at what is going on with their jobs. The guys can dial in via an App and they can see if there is ever a problem, rectify it and keep the spindle turning. The beauty of the MAM72-35V machines is that you can be programming and setting up parts whilst the machine is running.”
Why the MX330?
With the MAM72-35V machines being such a hit at MP Engineering, MTD magazine asked why the company opted for the MX330? Mr Poole continued: “The MX330 PC10 sits well within our business for our Formula One work. This is because with F1, we see much smaller batches than we do with aerospace work. The machine also has a much smaller footprint than the MAM72-35V, and we really are stretched for space.”
“The MX330 PC10 machines will run in the same fashion as the existing machines, we can even take a pallet from the MAM72-35V and drop it into one of the MX330’s. The machine has a smaller footprint and a lower price point, but you are not getting any less of a machine. The MX330 PC10 machines have the same intelligent software and systems that simplify around the clock running.”
Alluding to the ‘intelligence’ of the machines and the pallet selection process, MP Engineering’s, Ben Hayward told MTD: “We have a pallet manager on the CNC that identifies the pallet numbers and the schedule numbers, which allows you to change workflow. Finally, you have the option of the ‘reserve’ pallet whereby if you load a pallet, but you don’t want to run it at night, it will put it in reserve until you command otherwise. At the end of the working day, you can easily select the overnight running order of the pallets.”
When asked what would happen if a situation arose like a broken tool, Ben Hayward said: “This all depends on your individual set up. We have the machine set up, so if a tool breaks it stops the programme. You can configure it whereby if you get a broken tool, it will remove the pallet and put the next pallet in with the next job. The next job will subsequently run up to the point where it may need the broken tool. If subsequent jobs do not require that broken tool, then the parts will be completed.”
“There is also software that will monitor tool breakages, the ‘intelligence’ will tell the machine which tools are required for each pallet. From this, the machine will run pallets that do not require the broken tools.”