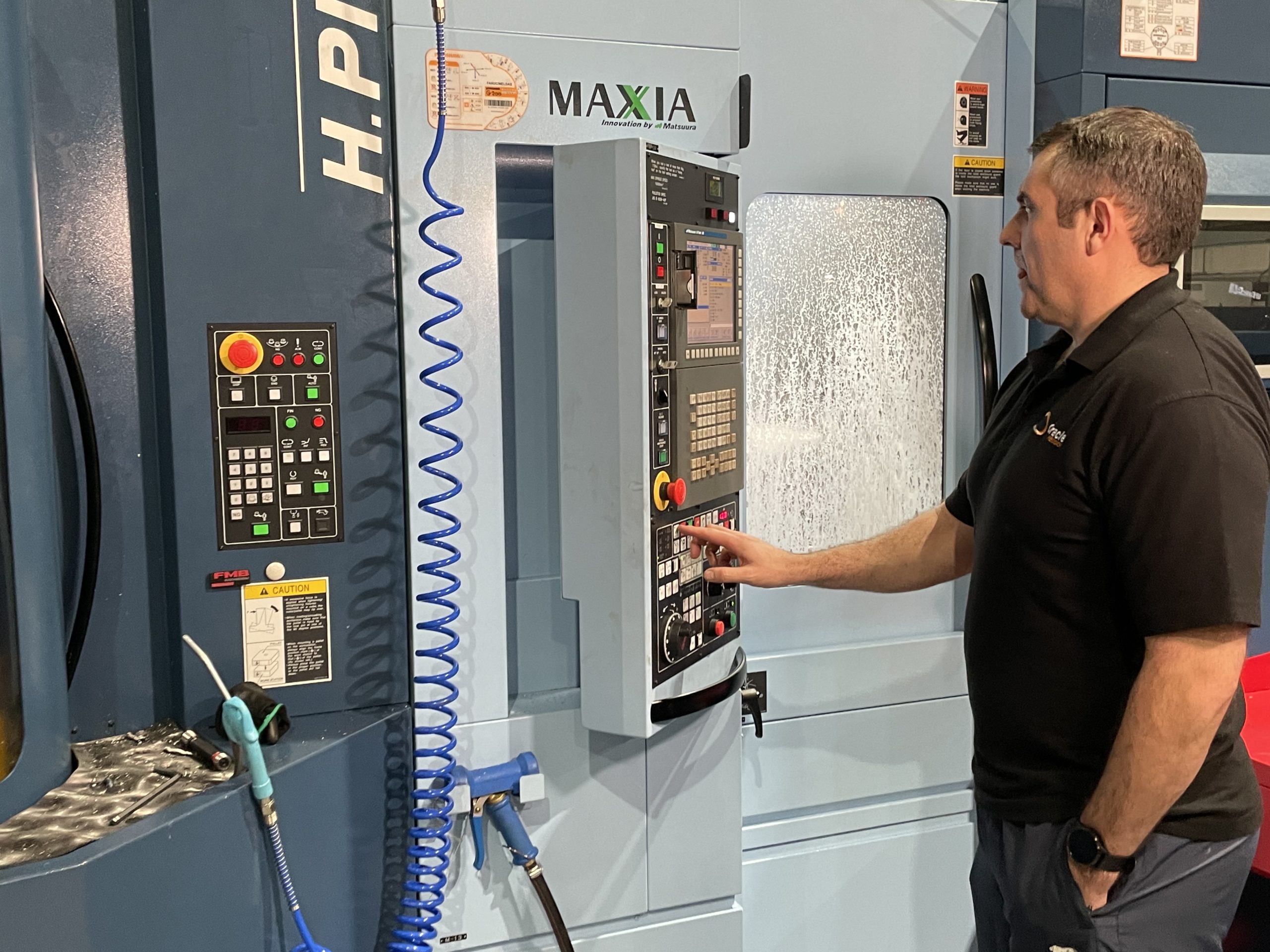
Now approaching its eleventh year in business, Oracle Precision recently invested in an H Plus-300 machining centre from Matsuura. The MTD team visited the Rotherham subcontractor to find out why.
Shaun Palmer Commercial Director at Oracle Precision explains why the company invested in the machine: “Matsuura was certainly at the top of the list when we were selecting possible suitors. In addition to that, they held our hand throughout the technical review, they did the off-line programming and cycle time analysis which has a big bearing on our commercial position. The future for Oracle is to remain close to our suppliers that quite frankly, we need as much as our customers. We provide a solution to our customers problems. So, whether it’s a right now, short-term or long-term strategy for them – when we select machine tool supplier, it has to be a company that is in it for the long run.”
“With Covid, everyone has had to re-analyse where their own business is. We have seen customers present more order visibility than they may have done historically, as they have recognised the importance of the relationship. We have now become very selective over who our customer is and the level of support we provide. By investing in a machine in this climate, what more demonstration of an ongoing relationship can you present than that,” says Shaun.
“By having this machine we have been able to service many more new and existing enquiries. We are serving more enquiries because our productivity and the visibility of our productivity has gone from sketchy, to 30 days to 40 days – and now we can focus right up to the following year where we can accommodate new customers as well as existing. We have survived Brexit and Covid, and we have found we were still turning work away during that period,” says Shaun Palmer Commercial Director at Oracle Precision.
Alluding more specifically to the new Matsuura machine, Co-Director Mr Ryan Taylor: “We went for the H Plus-300 because of the pallet system, the swarf fall away, the efficiency and because most of all we already have Matsuura machinery, so we know the service and backup is something where they can hold our hand with a new piece of equipment. The pallet system is so important for us to create unmanned running. There are 15 pallets on the H Plus-300 and the idea is that we maximise the space per pallet to get as much product on as possible, giving us more unmanned hours and production. This is important to us as we are finding it harder to get the skills. Additionally, to be competitive we have to run around the clock and at weekends without a man at the machine.”
“When we were doing our investigation, horizontal cells were better for swarf evacuation and efficiency because the pallet system. So, one of the biggest reasons we have bought Matsuura machines is they have technology built into the machines, so if a tool breaks at night, the machine can quarantine thejob and fetch the next pallet and carry on with its workload. If it can’t rectify itself, it will send you an email so you can come in and rectify the problem.”
“The job that we have running on the H Plus-300 at the moment requires heavy cuts using 80mm diameter face mills and 40mm diameter porcupine cutters. We are hoping the H Plus-300 will mirror what we are achieving on the MX-330 10-pallet machine with near 100% spindle uptime,” concludes Ryan.