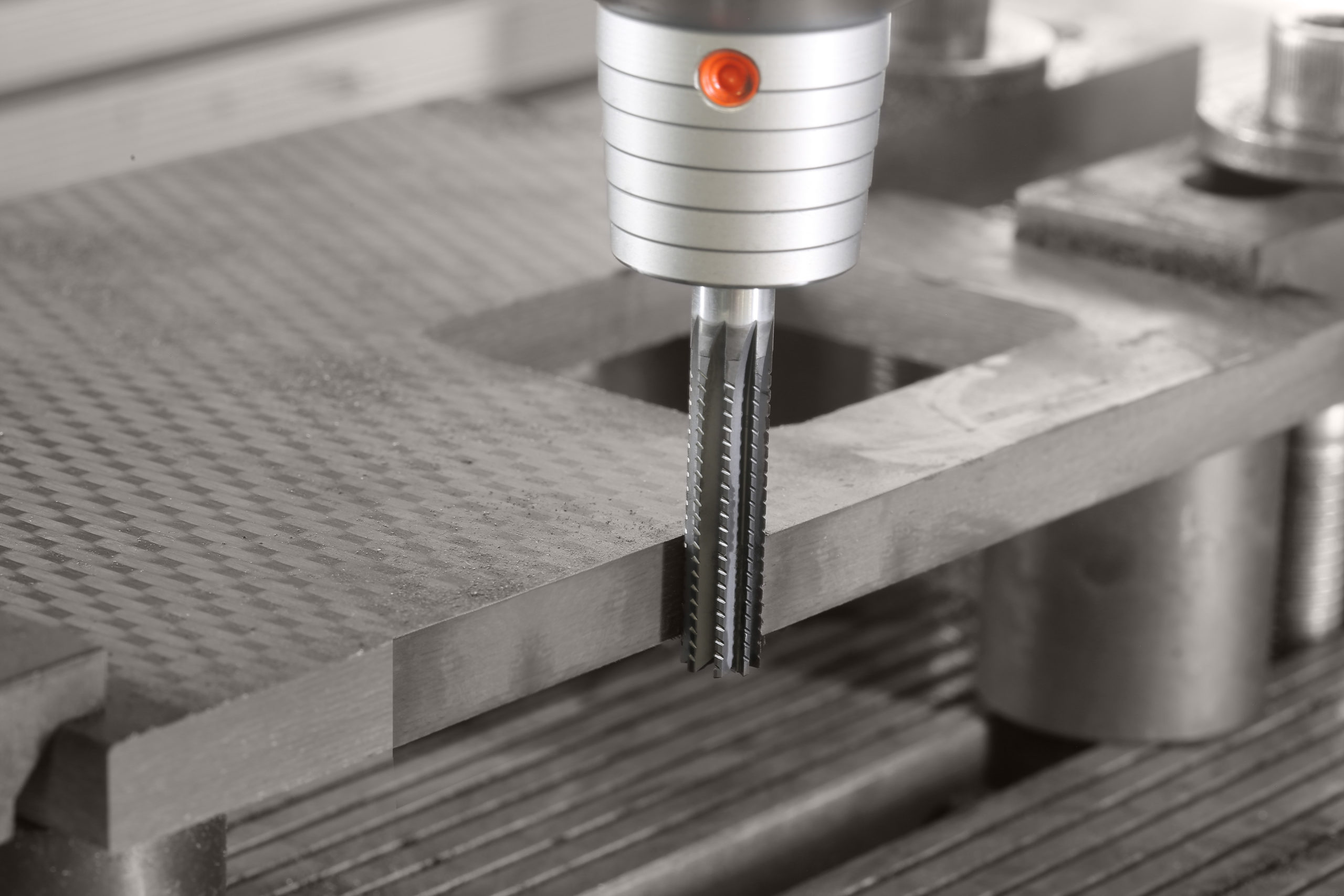
Machining structural aerospace components from CFRP materials for OEMs and the respective Tier 1 supply chain is, without doubt, an amphitheatre of gladiatorial battles for cutting tool manufacturers and their products. The cutting tools and the application engineers testing the tools are challenged with some of the most abrasive materials known to the industry, a factor compounded by extreme heat generation, potential vibration, risk of component delamination and moreover, the extensive running hours and material removal rate requirements.
Luckily for one Tier 1 manufacturer, they have been working closely with MAPAL for more than 10 years. So, when it came to the machining of a structural wing component, it turned to the Rugby-based cutting tool manufacturer for a solution. On the particular component, the aerospace company was previously applying an end mill from an alternate cutting tool manufacturer. The result was poor tool life, delamination of the CFRP material and an inconsistent tool life performance that resulted in customer having diminishing confidence regarding process reliability.
The application in question required rough and finish machining on the edge of large structural aircraft parts with a material thickness that varies from 10 to 20mm on numerous edges along a length of more than 17m. For the customer, the key objective was to eliminate delamination which was proving problematic with poor surface edges creating a requirement for secondary hand finishing. As with all aerospace components, quality is non-negotiable and the structural parts undergo non-destructive testing (NDT) after machining.
The prominent aerospace manufacturer introduced MAPAL Technical Sales Engineer, Mr Tad Forys to the component and enlightened the MAPAL engineer of the respective challenges with the part. Tad recommended the application of the MAPAL OptiMill Composite Speed Plus range of diamond coated solid carbide end mills – the results have proven nothing short of miraculous compared to the previous process.
The components are machined on a new type of lightweight robotic portable machine system that uses Parallel Kinematics Machining (PKM). This type of robot travels on rails, a factor that offers tremendous machining flexibility which can be compromised when compared to extremely robust traditional machining platforms. Recommending the MAPAL OptiMill Composite Speed Plus range, the MAPAL engineer was confident the new 8-flute tool would perform well. This is credit to the new high-performance substrate combined with a reinforced core diameter that increases the tool strength by more than 50% when compared to previous tools. Furthermore, the new tool has an optimised groove profile that ensures fast, reliable removal of dust and heat, even when undertaking extremely high-volume material removal rates. These factors are complemented by the innovative new cutting-edge geometry that has been optimised for use on materials such as CFRP.
As MAPAL’s, Technical Sales Engineer, Mr Tad Forys says: “Prior to the introduction of the new 16mm diameter OptiMill, the end-user was applying a PCD brazed tip tool.Unfortunately this tool was resulting in both poor tool life and component delamination. What we have been able to do with the new tool is rough machine the CFRP structural part at a 6mm radial depth of cut and then undertake a 2mm radial depth of cut finishing pass with varying cut depths from 10 to 20mm around the edge of the parts.”
“We have been machining the parts at speeds of 150 to 270m/min with a feed per tooth from 0.02mm to 0.04mm. This variation is dependent upon whether we are heavy rough machining or undertaking finishing passes. MAPAL has a reputation for exceeding expectations on some of the most difficult materials and applications known to industry – and for this aerospace manufacturer, we have proven our technology once again.”