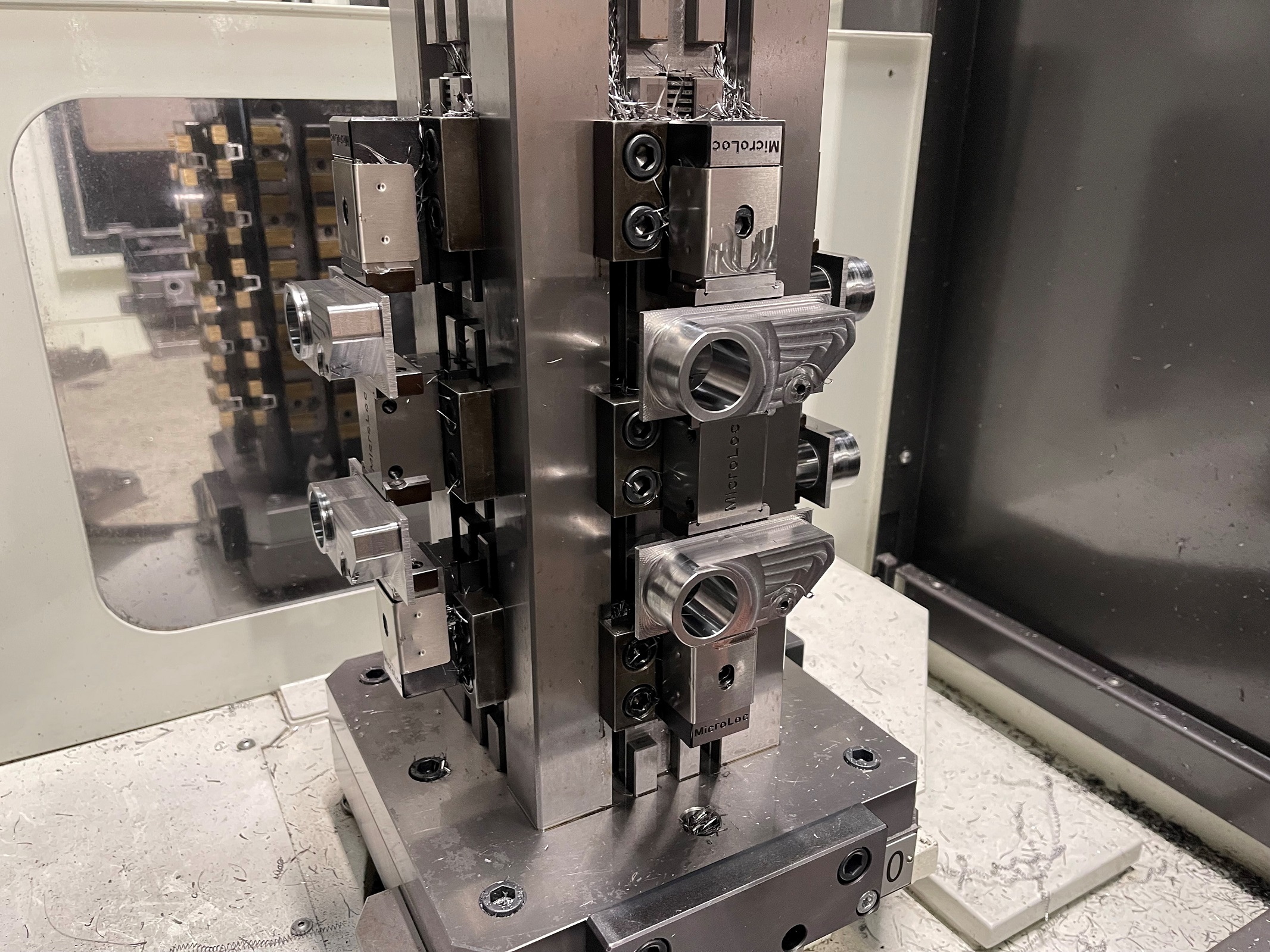
Approaching 20 years in business, Hi-Spec Precision Engineering Ltd has evolved from a small start-up business to an established subcontract manufacturer that has fully embraced the latest CNC and automation technology to drive growth. When the company was having issues with holding tolerance on a boring operation, the Market Overton company visited MACH 2022 to find a solution – it was found on the Horn stand.
Since its inception, Hi-Spec has made a natural progression through manual and CNC machining to 5-axis and high-end CAM, pallet loading and automated machining with capabilities including everything from conventional and CNC machining to grinding, lapping, honing, welding and fabrication, hydraulic pressure testing and assembly.
The workload at Hi-Spec encompasses everything from agriculture and aggregate, construction, motorsport, fluid power and electric guitars. The components at Hi-Spec include hydraulic valves and cylinders through to equipment for the quarry and aggregate industry, producing anything from prototypes and small batches up to production runs of 10,000+. The company is also renowned in the music industry, manufacturing custom precision-crafted electric guitars (www.graingerguitarparts.com).
On a recent project to machine 400 mild steel latch components, Hi-Spec was having an issue holding a 9µm tolerance on a 26mm diameter bore that needed to be machined through a 25mm thick plate. Producing the parts on its 10-pallet Kitamura Mycenter HX250iG horizontal machining centre with a BT30 spindle taper from Dugard, the company was struggling to retain repeatability.
Hi-Spec Precision Engineering Ltd Managing Director, Mr Darren Grainger says: “We were having issues keeping tolerance. We tried two different brands of precision boring heads with a variety of cutting speeds and feeds, but the tolerance would deviate over a batch of eight parts on each tombstone. With a precise and robust workholding configuration on the Kitamura machine that is known to be the epitome of precision, we knew that the cutting tools and the tool set-up was the issue.”
The holemaking process included drilling the mild steel plates to 18mm diameter and then milling the bore to 24.9mm and subsequently applying a high-end boring head to achieve a diameter of 26mm that is tied to a 9µm tolerance.
A visit to MACH 2022
“We decided to find a solution at MACH 2022. We looked around and we recognised that Horn is a leading brand when it comes to holemaking. We discussed the application with Horn’s Steven Kilpin and it was suggested that the URMA reaming system would be a viable solution. In less than a week, the tool with special tolerance inserts for the non-standard hole size was supplied – we were blown away!”
“Steve visited our facility and checked the installation and proved out the speeds, feeds and accuracy. The first thing that stood out for us was the speeds and feeds of these tools. We are running the new Horn URMA system at 2200rpm with a surface speed of 180m/min and a feed rate of 2200mm/min. At these speeds, it is less than two seconds to ream and retract from the hole. The previous systems we tried was taking 18 seconds to feed in and out of the bore, so the Horn system is making an incredible cycle time saving for us.”
The Horn reaming system manufactured in partnership with Urma AG, Switzerland is a modular system that caters for diameters from 7.6 to 200.6mm and it is particularly successful for applications in steel, cast iron, aluminium, titanium and inconel. Commenting upon the application, Horn said: “For this particular application with a 9µm tolerance through bore, we opted for the uncoated cermet grade. One slight issue was the BT30 spindle, as we don’t have a standard adjustable chuck for this. This provided an opportunity to test the relatively new compensation sleeve that allows us to adjust the insert holder runout using four peripheral screws similar to a 4-jaw chuck, to within the recommended 5µm tolerance band. Usually, we would use a run-out adjustable chuck on smaller sizes or integrated adjustable shanks on larger sizes.”
“Another problem we encountered was the lack of through spindle coolant. We would usually insist on high pressure through spindle coolant for this application as our insert holders have coolant holes directed at the cutting edges. However, as the through bore was relatively shallow, flood coolant was the only available option and it seems to be coping well. We were confident that the 9µm tolerance wouldn’t be an issue, as we have previously held tighter limits than this with other customers,” said the Horn engineer.
Providing his take on the situation, Darren continues: “It is always great to have the speed, but if the tool doesn’t last or hold tolerance, it becomes less impressive. So, we needed time to see how the new Horn URMA system was going to perform on a production run. The results have been amazing. Almost a month after installing the system and we have machined over 200 parts – and each one has been checked on our CMM. Undergoing this stringent quality assurance process, we have found that this reamer is still holding size and it fluctuates by no more than 4µm within our 9µm tolerance band. This impressive result is giving us complete process stability and confidence that we can machine these parts at speed whilst demonstrating unwavering precision and repeatability to meet the demands of the customer.”
Equally important to a manufacturer like Hi-Spec is the surface finish that can be achieved, alluding to this, Darren adds: “Despite running at high speeds, the surface finish is still below 0.8µm and the cutting head looks like it’s barely been used. We are always pushing the boundaries of what we can achieve, but this tool has blown us away with its performance, precision and repeatability and exceptional tool life. We really can’t thank Steve from Horn and Roman at URMA enough for sorting out this problematic project for us.”
Concluding on the new tooling installation, Darren says: “We are hoping that this batch of 400 will be the first of many and the job turns into an ongoing project. If this becomes the case, the cycle time savings will be significant as will the tool life savings. Most importantly, the Horn system is giving us confidence that our parts are going to conform to the very tight tolerances on this job whilst delivering a very good surface finish.”