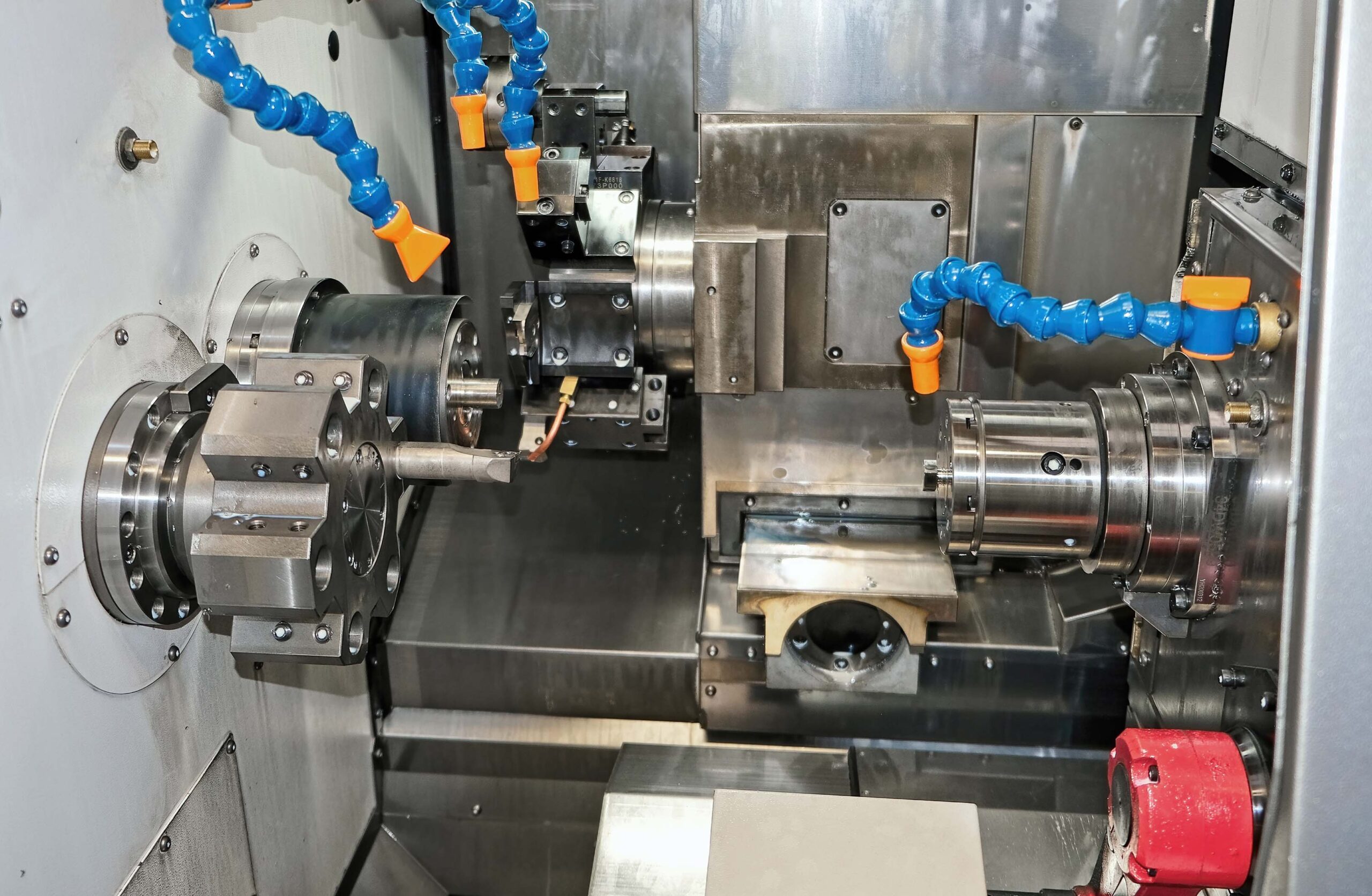
SFC (Europe) manufactures, stocks and supplies safety-critical and high-performance stud bolts, bolts, and nuts in ASTM and ASME grades for onshore, offshore, and subsea applications. They are mainly destined for global energy customers but are also used in the automotive, valve, heat exchanger and pump sectors. The Wolverhampton company has enjoyed impressive growth, from a turnover of £1 million when it was formed in 2013 to £15 million in 2024.
In the early days, the company served mainly the oil and gas, petrochemical, valve and renewable energy sectors, which involved turning batch quantities of anything from five to 500 parts, with the occasional run of 1,500. Then, in 2018, other industries started to show interest in the products, and today, the original markets account for only around half of the manufacturer’s turnover. Some of the more recent customers ask for similar, small to medium quantities, but frequently, they request 50,000 off, forcing SFC (Europe) to change how it viewed its turning and milling equipment.
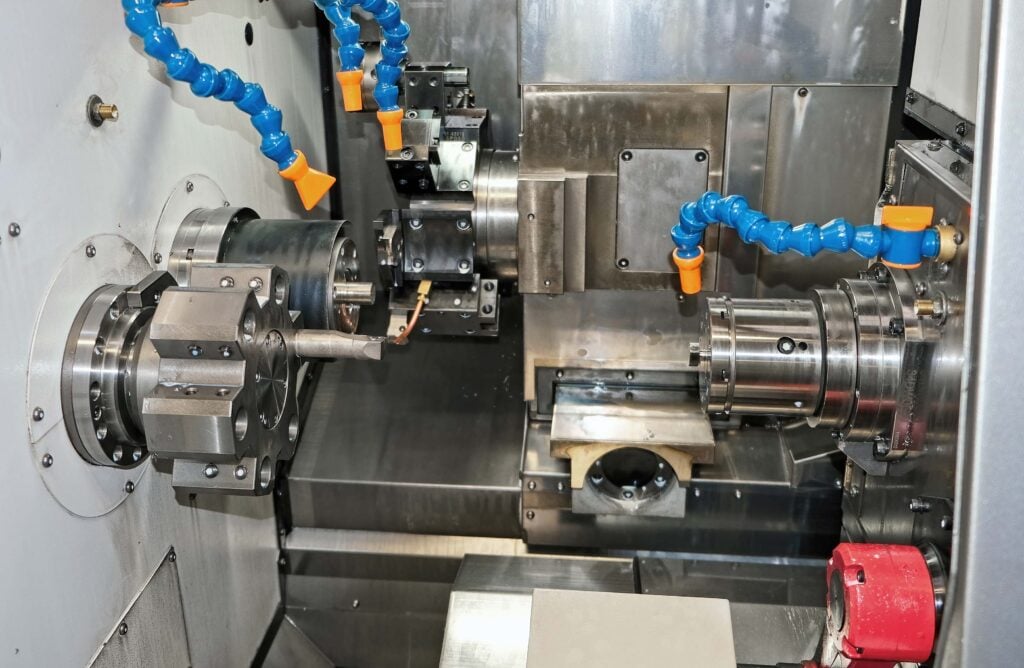
Operations Director Mark Edmonds said: “In the early days, we bought fasteners for stock and sold them worldwide, but within six months, we gained ISO 9001 and started manufacturing products, either to customer specification or international standards.”
“Our machine tool count was boosted in 2016 by acquiring another fastener producer. The capacity was sufficient for the quantities we were producing at the time. Still, a couple of years later, the larger quantities were being ordered by customers, necessitating a rethink.”
Part of the deliberations was shaped by the metals that needed to be machined. Along with carbon steel, they include stainless and superalloyed steel and nickel and titanium alloys. One nickel-copper alloy, Monel K500, is difficult to machine due to its ductility and abrasiveness. Any new turn-milling centre had to be robust enough to process these materials. It also had to be versatile and quick to set up, as urgent short runs were frequently ordered for next-day delivery while long-running jobs were in progress.
Since 2019, Mr Edmonds and his colleagues have been considering sliding-head bar turning owing to its suitability for producing large quantities of components, including unattended overnight. Covid delayed things somewhat, but by mid-2022, SFC (Europe) was ready to invest in new turning centres. It was, however, a pair of fixed-head lathes that was bought, as production staff in the Wolverhampton factory was unfamiliar with operating sliding-head equipment, and management wanted modern, productive lathes that would come on-stream quickly.
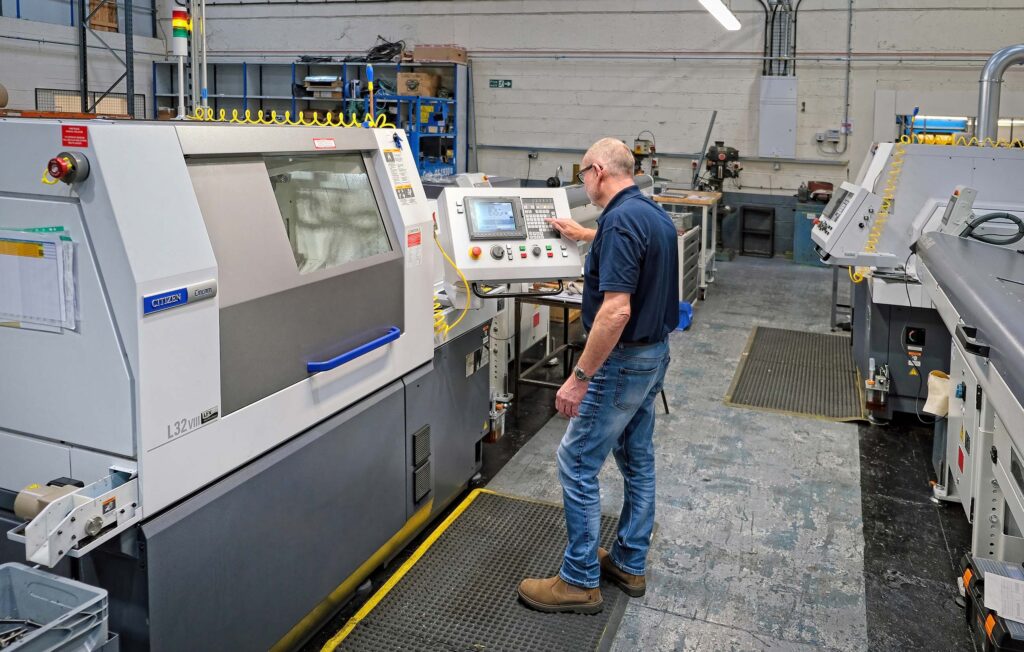
Two identical 7-axis Miyano BNA-42DHY twin-spindle, twin-turret, and bar-fed lathes were duly installed, the manufacturer’s first machines sourced from Citizen Machinery UK. The supplier was chosen after subcontractors within the fastener industry had been consulted, as well as Google, plus Citizen at one of its open houses. Demonstrations at the Brierley Hill Technical Centre, where faster than expected, one-hit cycles were shown to replace three or four separate operations successfully, clinched the deal.
A few years later, SFC (Europe) was ready to revert to introducing sliding-head, bar-fed lathes. The Miyanos had performed so reliably in terms of uptime and accuracy that Mr Edmonds looked no further than Citizen for the supply of two Cincom L32-VIIILFV turn-mill centres. Delivered and commissioned in April 2024, they mainly fulfil orders for higher volumes of parts. As traceability is often essential, the ability to engrave them in-cycle on the fast, nimble machines saves a separate operation and contributes to maximising production output.
The nominally 32 mm bar capacity lathes can machine components from up to 38 mm bar with the guide bush removed, which saves material due to shorter remnant lengths. Accordingly, one L32 is permanently set up without the guide bush for producing parts up to about 2.5 times diameter, while the other has the guide bush in place for turning longer components.
Subscribe to the MTDCNC Newsletter
Subscribe to our Newsletter today!
Stay up to date with the latest industry news and events.
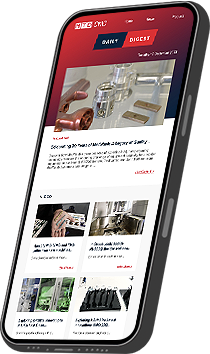