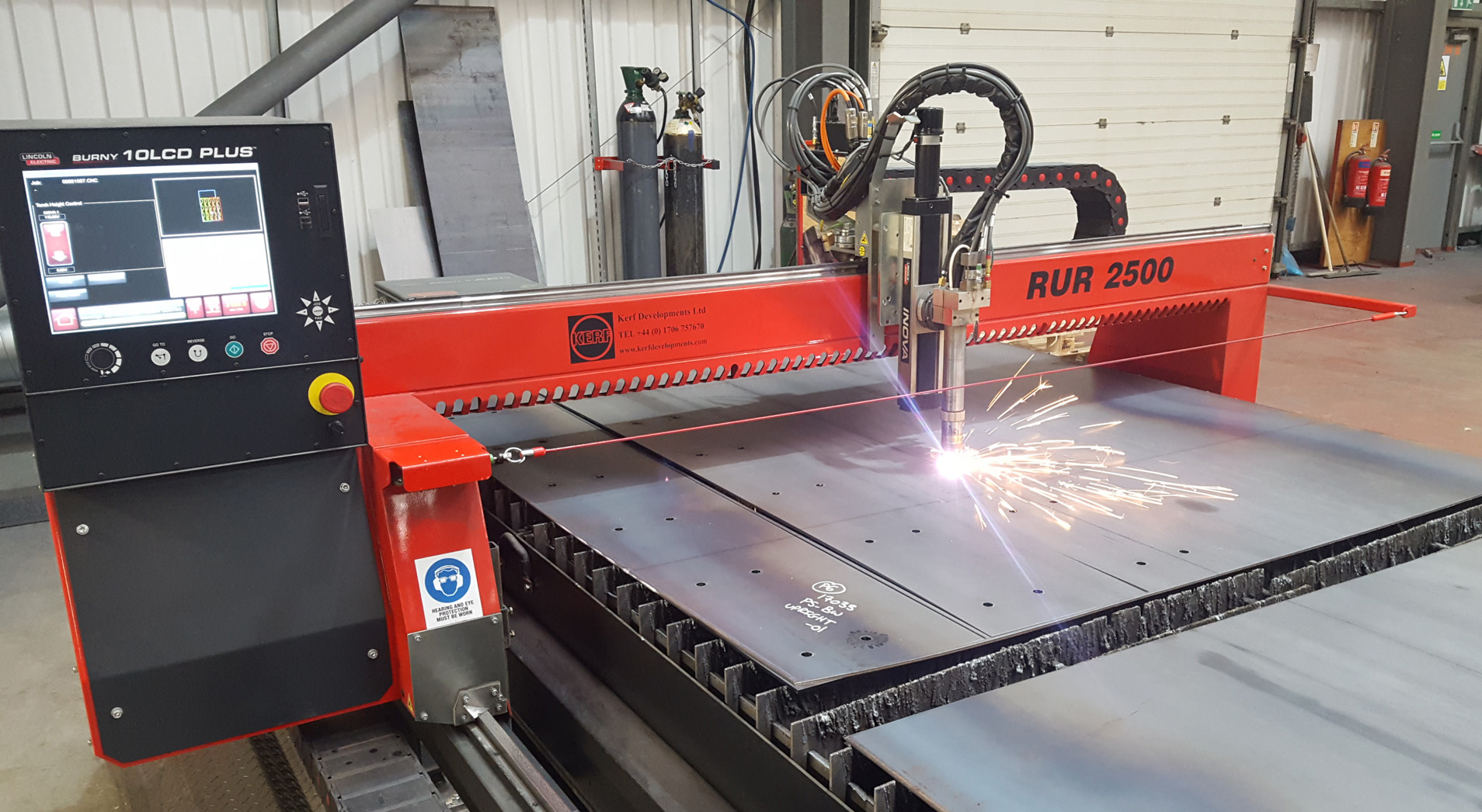
In Hall 17 on Stand 309, Kerf Developments will present a mix of cost-efficient high technology cutting solutions. At MACH, Kerf will expect its RUR2500P high definition plasma cutting machine to create a spark of attraction.
With its UltraSharp cutting technology, the machine is suitable for subcontract profilers, fabricators, structural steel, construction, rail and heavy engineering professionals. It combines both speed and precision with the consistently high cut quality and the lowest possible cost of manufacture. The RUR incorporates a rigid frame design that is ultrasonically stress relieved and this robust build quality and precision cutting has made the RUR2500P a popular choice for heavy industry sectors. The RUR2500P has a cut width of 2m and the modular design permits table dimensions to be tailored to the demands of the user.
Alongside the RUR2500P, will be the new Fineline 300 Plasma unit from Lincoln Electric that incorporates Advanced Piercing Technology and a new Watermist system. The Fineline 300HD delivers exceptional cut quality when cutting. Designed to allow full user control from a single interface, customers can change plasma current and gas pressures for better cut quality. With a small 38mm diameter 300A torch, the FineLine 300HD minimises secondary processing with its new Magnum PRO LC300M torch. Working with the UltraSharp 2.0, plasma current controls are all synchronised to control motion, gas flow, cut speeds and height control.
The FineLine 300HD also includes Advanced Process Control, an advanced piercing system that provides highly repeatable hole cutting. The FineLine 300HD also introduces a new water injection system that improves performance on stainless and aluminium. The watermist system improves the cut quality on aluminium by using water as the secondary gas to control the atmosphere in the cutting zone. The result is repeatable perpendicular edges, clean and precisely finished cuts, dross, smoke, and dust reduction as well as significantly reduced running costs. By reducing the heat zone, the water system improves the definition of corners, reduces bevels, and delivers a lower cost per cutting metre.
Also making its debut, the new Optima 216 waterjet cutting machine features a 2 by 1.6m cutting table that will appeal to manufacturers with limited floor areas that require a solution to undertake everything from one-off and general jobbing work through to batch production.