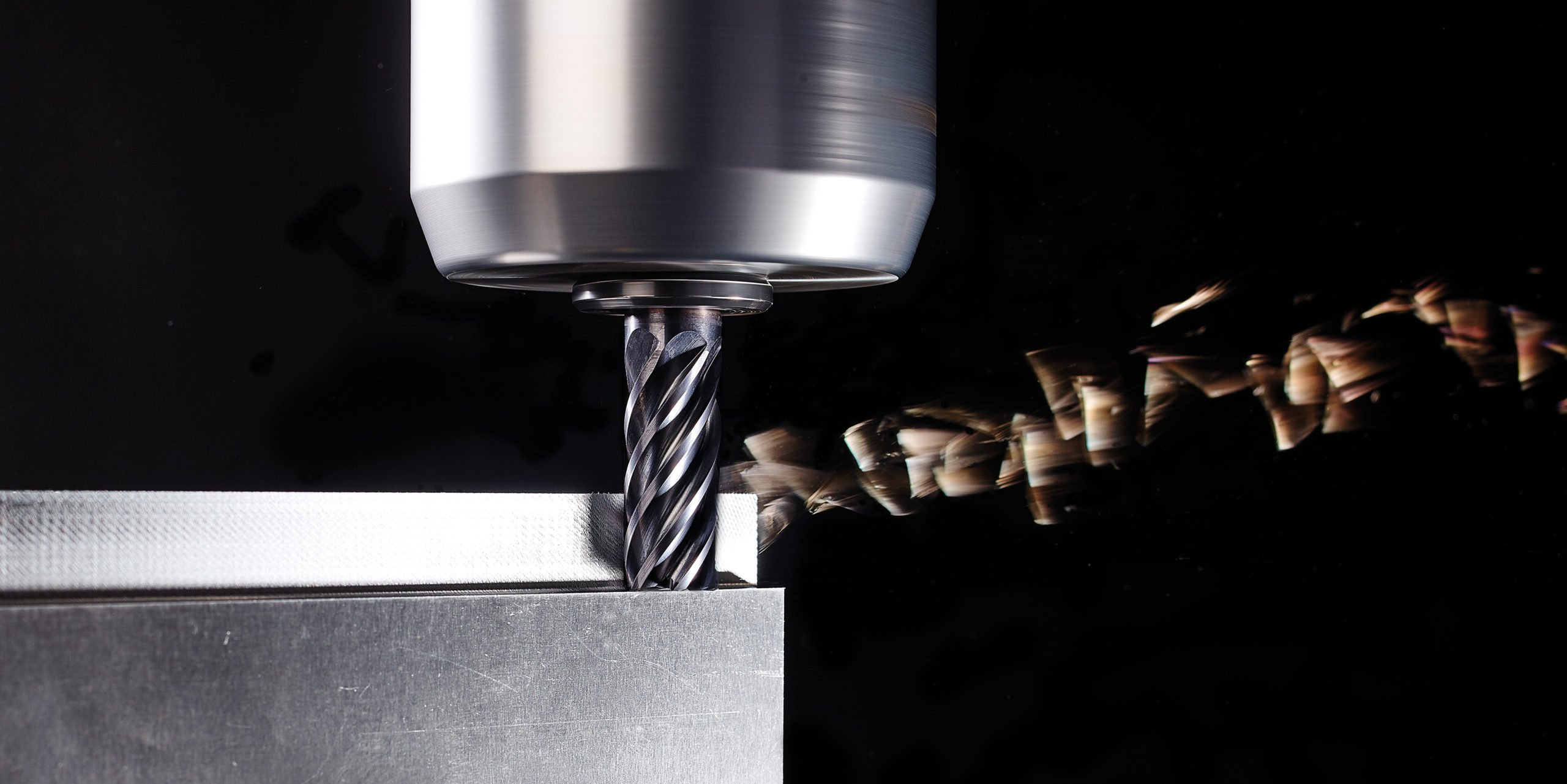
Kennametal recently delivered a seminar on rough machining strategies in the aerospace sector. The masterclass presentation gave a comprehensive overview on the production of structural components, ‘buy to fly’ ratios, machining strategies, the importance of effective tool holding and of course, the most suitable tooling products from the Kennametal stable to achieve maximum Material Removal Rates (MRR). With the industry facing significant challenges and a laser-like focus on cost reductions, MTD magazine wanted to find out more.
With more than 50% of attendees being manufacturers of either aero structures or assemblies, the informative presentation from Kennametal’s Mr Werner Penkert, Global Manager of our Future-Solutions Engineering team and Dr Adrien Cellier, a leading member of Kennametal’s aerospace solutions engineering team delivered some interesting insights.
The objective of the seminar was to highlight the best and fastest route from an aerospace forging to a finished structural component and the role cutting tool technology plays in reducing production times and costs. To emphasise this, the first point of note was the relevance of the ‘fly-to-buy’ ratio, which refers to the weight of the raw material purchased compared to the weight of the final part and the associated costs. Alluding to ‘tremendous’ metal removal with a 10X buy-to-fly ratio, Kennametal highlighted a 4.5 tonne helicopter rotor that as a finished machined component weighs in at 450kg and also a titanium structural beam that starts life as a 3.6 tonne casting and finishes as a 360kg machined part.
With structural components being manufactured from high strength steel and titanium alloys, the cutting tool industry has to not only meet the challenges of extremely high MRR, but also the torque requirements placed upon the machine tool. The higher the torque requirements, the greater the stress on both the cutting tool and the tool holder that is the conduit between the spindle and the cutting edge. Recognising the extreme stresses placed throughout the spindle, toolholder and subsequently the cutting tool, Kennametal has launched its new KM4X spindle system.
Labelled as the new generation in spindle interface and toolholders, the KM4X incorporates a number of innovative features. This includes three contact faces and an evenly distributed clamping force that demonstrates extraordinary rigidity and dampening capability. The simple design allows front loaded spindle configurations and a wide adaptability that is suitable for everything from low speed and high torque applications through to high speed, low torque processing – credit to the system being balanced.
Despite this speed and torque variation, the KM4X interface can achieve performance with particularly small bending deformation. Under testing on a 12,000rpm machine with 37kW of grunt, a HSK63A toolholder can maintain a clamping force of 18kN whereas the new Kennametal KM4X retains a clamping force beyond 47kN, more than double the industry standard configuration. The difference for HSK100A and HSK125A configurations is equally impressive. The impact of a solid clamping foundation can have a profound impact upon tool life, MRR, surface finishes and overall productivity and throughput – facts that both Dr Adrien Cellier and Werner Penkert were keen to emphasise. Looking specifically at the cutting tools, Kennametal has a multitude of solutions for the aerospace industry, but this seminar focused particularly on the 5720 series of aluminium machining cutters for high-speed slot and copy milling in aluminium, the high-speed HARVI III solid carbide milling for semi-finish and finishing operations on titanium alloys, and of course the impressive HARVI Ultra 8X helical milling cutter.
The HARVI Ultra 8X helical milling cutter plays an important role in the roughing of titanium structural parts and it is claimed to take Kennametal to the next level of performance through its highly engineered technology. As a quick overview, HARVI Ultra 8X incorporates new chip flute enhancements for improved swarf evacuation, optimised coolant nozzles that have a number of orifice sizes to allow fine-tuning of the coolant flow and most importantly, eight cutting edges to provide a lower cost per edge when compared to competitor products.
With enhanced chip gullets for MRR, enhanced coolant nozzles and increased cutting edges that is the result of the very best in design, leveraged from both Kennametal and Stellram, the HARVI Ultra 8X is a game changer for the aero structure sector. As you would expect, the HARVI Ultra 8X is available with a number of diameters (50. 63 and 80mm), lengths and interface variations and this also extends to the insert shape, geometry, design, corner radii and extensive grade availability – something than now includes the latest KCSM40 cutting grade.
Demonstrating the capabilities through the seminar, Dr Adrien Cellier and Werner Penkert provided field test results that certainly raised the eyebrows. Running the new HARVI Ultra 8X at a cutting depth (ae) of 76.2mm and a radial cut (ae) of 25.4mm with a cutting speed (vc) of 47.3m/min, the HARVI Ultra 8X with a 0.8mm insert radius tore through titanium at a MRR rate of 329cm3/min.
In another demonstration of the ferocity of the new HARVI Ultra 8X, a slotting field test on a 5-spindle Cincinnati XT machining titanium (Ti6Al4V) with a HSK 125A back-end ran at a cutting depth (ae) of 47.5mm and a radial cut (ae) of 76.2mm with a cutting speed (vc) of 47.3m/min to achieve a MRR of 426cm3/min with minimal insert wear and a very quiet running noise. Pushing the envelope further, the second slotting test cut ran at almost identical parameters except for doubling the cutting depth to 95mm, which subsequently increased the MRR to 536cm3/min.
The seminar continued the theme of MRR with both indexable and solid carbide milling lines before moving toward the complete engineered solution and what Kennametal can offer the end user. The experts enlightened seminar attendees on the complete package that encompasses everything from process definition and tool selection through to CAM strategies, performance comparisons and estimations, cutting data, torque and power validation, cost per part analysis and even tool design and costing management. We’ll be taking a look at other Kennametal innovations in future issues of MTD magazine.