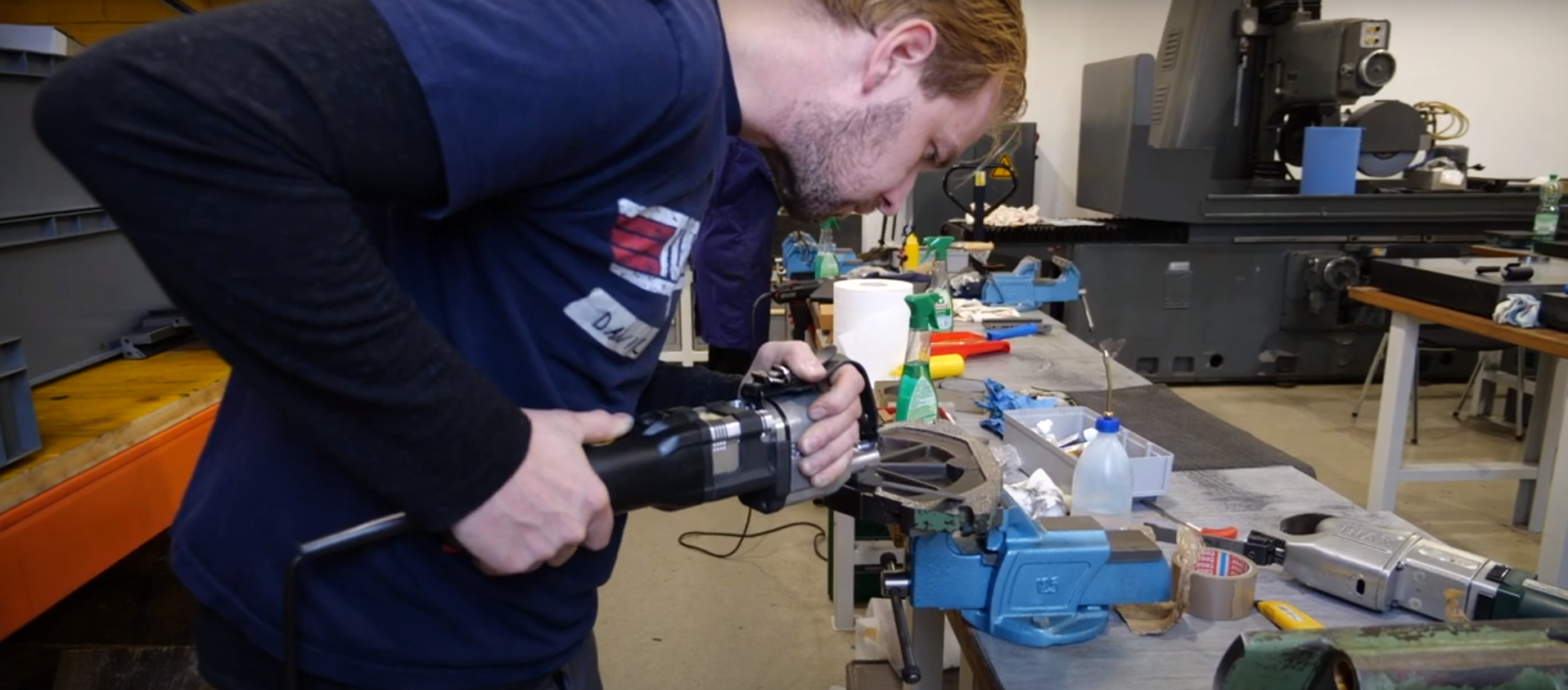
It always makes me wonder when looking at old photos of milling, turning and grinding machines – how did the engineers from that era achieve such a high precision to be able to machine combustion engine blocks, jet engines, and spaceships? Interestingly, most of that accuracy was achieved by our own hands and not the machines or post-cast manual machining methods to increase the accuracy and rigidity of our machines. One of these ancient yet still popular methods is Hand Scraping. By Kasra Mehraky
Hand Scraping is the method for removing tiny bits of metal from a surface using a manual scraping tool. In this article, I am not trying to define or discuss the different methods of hand scraping, but its necessity in machine tools.
Hand scraping is definitely a time and energy-consuming process, as it requires highly skilled labour, which leads to its high cost. But can it be skipped or even overlooked? We have many capable and accurate machines at our disposal nowadays. Can a manual process really improve the accuracy of a ground surface that has been done on a multi-million-pound piece of machinery?
These are the questions that designers, manufacturers and even users of machine tools have to consider when this controversial topic is mentioned in any meeting between the producers and users of machine tools for investing in new machines. There is no simple ‘Yes or No’ answer to these questions. In this article, I will discuss the advantages and disadvantages of this precision method of material removal so that you can decide more efficiently on your new investment.
Firstly, Does Hand Scraping help to achieve more accuracy?
The answer is YES! But it highly relies on the person’s expertise and experience, after all, it’s all done by hand (in the Japanese method, a combination of hands and legs and some dance movements!).
How is it done?
By scraping a milled or ground surface, manufacturers are trying to produce an incredibly flat surface. Since the hands can’t produce an even force on every single point of the surface, the aim is to create a specific number of evenly distributed high and low points on the workpiece surface.
How does Hand Scraping improve machine accuracy?
When the high points from two different scraped parts mate, the contact area between the two can be up to 1.5 times higher than two perfectly ground surfaces. This extra connection between the two surfaces (in our case two parts of the machine tool structure) can channel the machining forces much better to the next structural piece. This will result in much better vibration damping and less chatter.
Excessive vibration in a machine tool can decrease cutting tool life, machine rigidity, machine life, machine accuracy, workpiece surface finish quality, and increase noise. It can also increase energy consumption (spindle overload or the servos trying to maintain the correct position), heat and scrap parts. All effectively resulting in less profit and more costs!
Does everybody need it?
The answer is NO! The majority of the industry will not push their machines to their limits whereby the aforementioned problems take place. The machine’s body should preferably be hand scraped. But if not, we should carefully decide whether it is necessary for the application or not. A hand-scraped machine would be significantly more expensive than a machine that has not been. If your parts require tight tolerances, if you need extreme repeatability, if you make heavy cuts or if you are going for a box guideway machine, then you should definitely choose a machine that has been manually scraped.
Why do box guideways rely on scraped surfaces?
This is due to a phenomenon called ‘Stick-Slip’. This happens when two ground surfaces are mating each other. These parts tend to stick together. This can increase friction, load on the motors and ballscrews. This can cause serious issues in the long term. If you are buying a machine that is using box guideways make sure that at least one side (usually the shorter side) is scraped. The low points on the scraped part make evenly distributed cavities that are perfect for carrying oil and they provide lubrication while suspending the aforementioned ‘stick-slip’ issue.
Do non-scraped box systems exist?
The answer is YES! Some OEMs, especially in China, have been selling machines with box systems that have not been scraped and this can result in extremely costly problems for the user.
How about other types of movements, such as linear guideways?
This is where it gets tricky. I believe that if the surfaces where linear rails and blocks are mounted on the machine are scraped, it improves the surface contact between the structure and these components. Although the tolerance between the block and rail might be higher than the flatness of the surface, scraping still provides better contact, which results in higher rigidity. But, when using linear guideways, hand scraping is less crucial.
What other parts need to be scraped?
All other mating parts, moving or static should be scraped. These parts can be structural surfaces, such as the spindle housing surface, the mating surfaces of the column and bed, and the bearing housings such as the ballscrew nut mounting surface, ballscrew support bearing housings, servo motor holder surface, rotary axis bearing housings and so on. Scraping these parts is arguably more important than any other surface in a machine tool. For instance, in the case of a ballscrew, scraping both of the surfaces on the machine and the bearing housing will prevent material wear, buckling, heat generation, friction and noise.
In conclusion, if hand scraping is done properly, it can increase accuracy, surface finish quality, rigidity, stiffness, component geometry and machine life cycle. However, hand scraping is time and energy consuming and unnecessary for some applications. The key point when looking to purchase a new machine tool is the TCO (Total Cost of Ownership). Even if the price tag of a hand-scraped machine is higher, in the long term, it can guarantee a much better ROI (Return On Investment) and a higher value of TCO, since it is producing fewer scrap parts and generating higher-quality workpieces. Effectively, this results in more money and profit for the end-user.