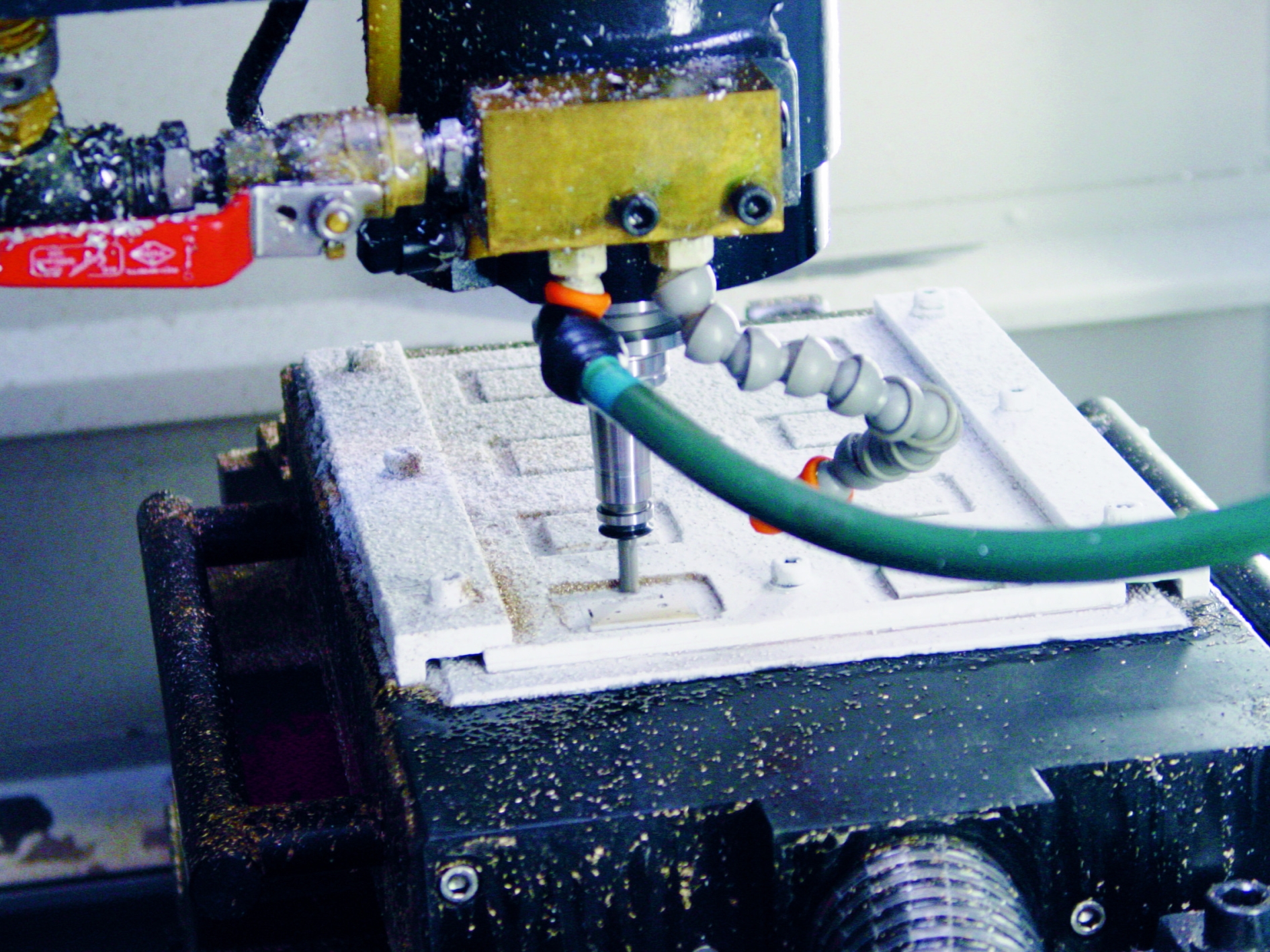
Workholding solutions for components that would be seemingly impossible to fixture any other way are now solved by the Triag triGEL range of freeze clamping plates that are now available from REM Systems.
Freeze clamping is a clamping technique that is primarily used for bulky parts made of metal, most mineral materials as well as engineering plastics. When using the triGEL system, cold gas is run through the worktable cables and cooled to the working temperature of -8oC.
The workpieces and the worktable are coated with a fine water film, which clamps the parts in place after freezing for approximately 60 seconds. The process is reversed to loosen the workpieces. The device functions as a heating pump that allows the thawing point to be reached quickly to release the workpieces.
Fixturing with ice is a physical phenomenon that many of us have experienced. Taking hold of a metal handrail in the winter when the temperature is below zero, you can suddenly find your hand stuck to the rail, a perfect example. This same phenomenon is used by ice clamping devices and there are two different methods of achieving the necessary cooling of the machine table or working surface. First is the Peltier Effect for thermoelectric refrigeration, and the second is the use of a cooling medium such as those commonly applied within a deep freezer. In this second method, the latent heat of evaporation of the cooling medium (for example R4040 that has no greenhouse effect) contained in a closed coolant circuit is used. The cold gas passes through a labyrinth of channels in the machine table, bringing its temperature below zero.
Managing Director, Ian Holbeche, explains: “The second method is significantly more powerful, and that is why Triag applies this technique within its triGEL system. At 2N/mm2 the adhesive strength is up to 20 times greater than that achieved by vacuum clamping. And, since there are no clamping forces applied to the workpiece there is no stress transferred, so even semi-flexible parts can be machined to very tight tolerances.”
Both the machine table and workpieces are covered with a fine film of water using a water atomizer. This causes the workpiece to stick to the machine table within approximately 15 to 60 seconds. The process is reversed to release the workpieces with the triGEL operating much like a heat pump, so the dew point is reached very quickly to release workpieces.
For parts with a flat surface, the thickness of the film of water or ice is negligibly small. Components with irregular geometry can be frozen solid in a water bath before being fixed to the worktable. All metallic and most mineral materials, as well as many engineering plastics, can be clamped in this way.
“Ice clamping was once confined to use in the watchmaking and jewellery industries,” says Ian Holbeche. “Now, with standard table sizes ranging from 100mm up to 500 by 550mm, the Triag triGEL range can extend its application into medical device and implant technology through to general precision engineering.”
Triag’s triGEL system consists of two interconnected elements, the table and the control cabinet. The workholding table is made from thermo-conductive materials such as aluminium and copper. The refrigerating gas R4040 circulates inside the standard-sized or custom-made tables.
Contained in the control cabinet is the compressor and heat exchanger, thermostatic control for freezing and the reheating process, including the system to maintain a pre-set temperature for holding the parts during the machining cycle. The electrical safety circuitry with control lights ensures the workholding process is fully functioning, as well as the interface to the machine control system for process monitoring and control.