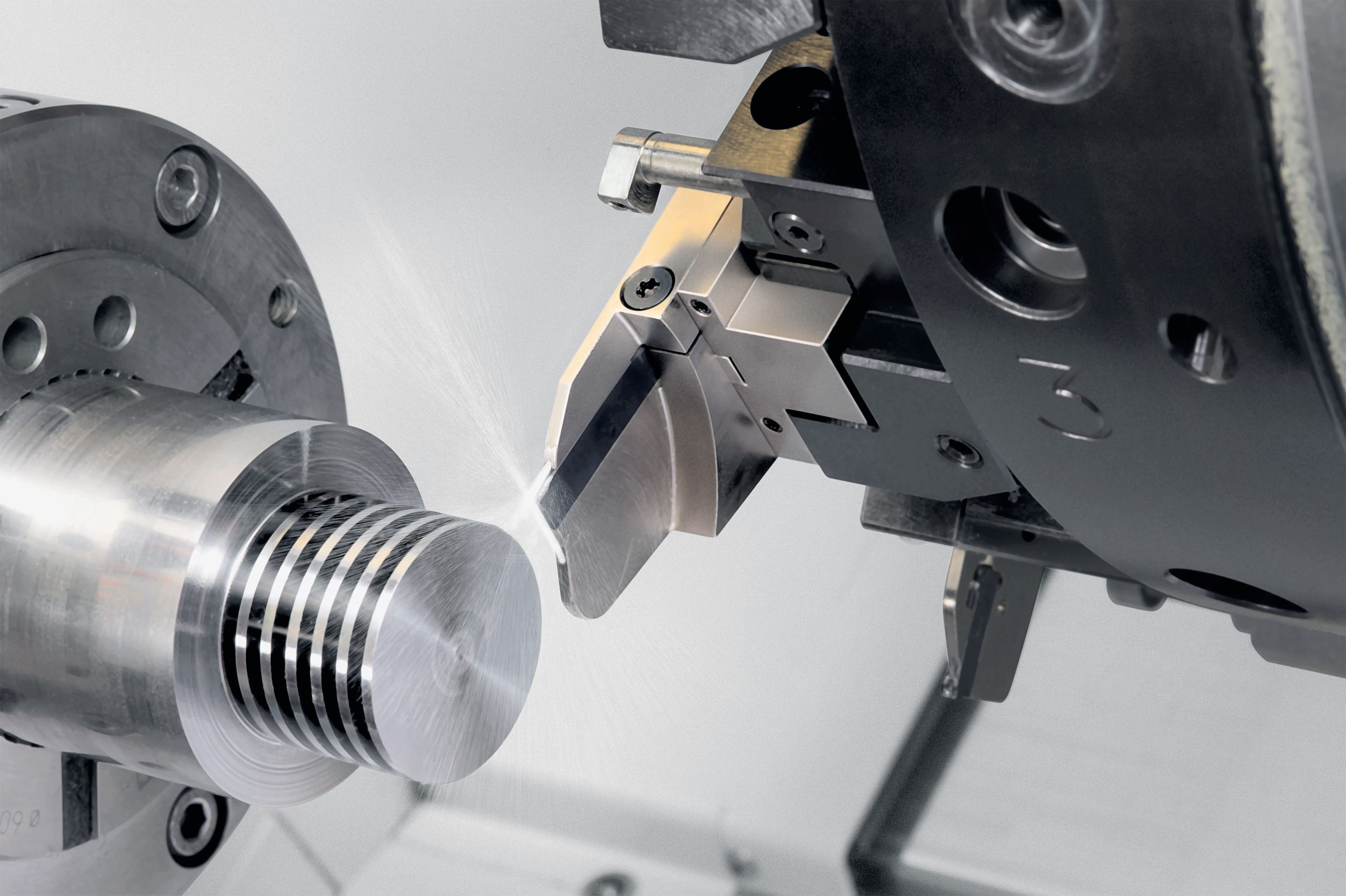
Parting off and grooving are demanding turning operations. Many parameters determine the result. In addition to the rigidity of the machine, feed rate and cutting speed, the parting-off and grooving tool are decisive factors governing the quality and efficiency of the operation. If you ignore the diversity of materials, blades and holders, it will quickly become very costly.
With parting off – the devil is in the detail. There is so much to be considered in this turning operation. After all, it plays a decisive role at the end of the turning process – after the added value has already been invested in the workpiece. In addition to feed rate and cutting speed, groove width and cutting depth, chip evacuation is one of the factors that requires particular attention.
Diversity reflects application experience
Anyone who underestimates the complexity of grooving and only uses individual parameters for their decisions will pay dearly. This also applies to parting-off and profile grooving. Suppliers with application experience, consultancy expertise and fast-response service can boost processes and productivity by upwards of 400%.
Family-owned Arno offers parting-off and grooving systems with a diversity that reflects the company’s vast experience. The double-edged SA grooving system with groove widths of 1.5 to 10mm is suitable for cutting depths of up to 140mm diameter. Together with many modules, holders and blades, the parting-off tool is always optimally adapted to the situation. Arno offers a wide range of machine-related flange-mounted holders for many machine brands.
Stability and low vibrations
Users can choose from six geometries, seven coatings and two solid carbide substrates to achieve the best possible results. The SA grooving system is adapted to steel, stainless steel, aluminium or difficult to machine materials. It ensures an uninterrupted cut for applications that require optimum chip-breaking geometry.
Chips tend to build up and jam in the groove, especially at parting-off. This is compensated for by using the right geometry. It also produces high-quality parting-off surfaces, as the system works with low vibration due to its high stability, regardless of the feed rate and cutting speed.
For grooving applications and Swiss-type machining, the manufacturer recommends the flexible solution of its SE groove turning system. As it is highly stable, it achieves perfect results despite high lateral forces. The SE system allows users to part off, even if workpieces have a large radius. This is shown by groove widths of 2 to 6mm and cutting depths of 12 to 21mm. Other features include its easy handling and long service life. Here, too, seven geometries demonstrate the manufacturer’s broad experience with materials and requirements. Users can also order precision-ground inserts for SA and SE systems with an aluminium geometry, or sintered inserts with geometries suited to many materials.
Arno has developed a third tool for small diameters. The three-edged ATS system can be used by turning operators for a wide range of short, precise grooves. ATS offers a large cutting depth of 6.5mm. Groove widths start at a very narrow 0.8mm and extend to 6mm. When it comes to profile grooving inserts, contours up to 20mm long can be mirrored on one insert.
Think about the processes, not just the products
Some tool manufacturers will also find custom and application solutions to improve processes and increase productivity. Here, Arno presents products that demonstrate precisely this philosophy – such as its AWL/AFC quick-change tooling system. The two-part carrier tools make for quick tool changes that even unskilled personnel can easily perform safely.