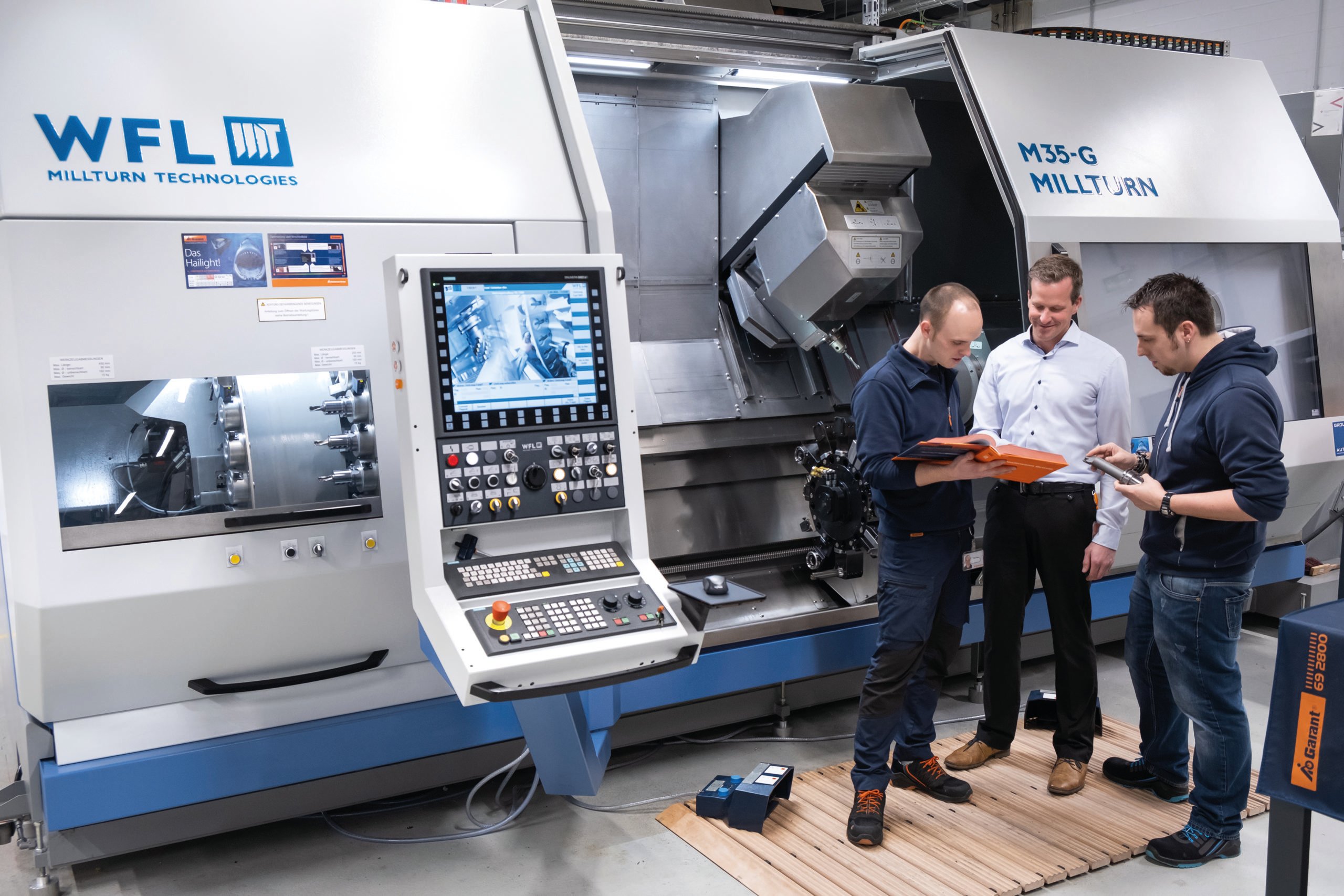
With over 4,000 employees and an extensive range of tools and equipment, the Hoffmann Group is a major player in the industry. In 2019, parent company, Hoffmann SE installed its first WFL Millturn machining centre. This machine takes on a highly unconventional role as rather than producing components, it is used to test and optimise tools.
“We don’t make tools in this department, they are developed in conjunction with suppliers,” explains Dr Jens Rossaint, Engineering Director, responsible for the quality management of products developed for the catalogue. The orange ‘tool bible’ has been published since 1978 and is available in 18 languages and is now backed by an eShop.
There is a process for including a product in the catalogue. Firstly, the company defines what the tool should be able to do, draw up a specification and integrate technical ideas. Then there is a tendering process and suppliers are narrowed to a shortlist. They then manufacture prototype tools. This is followed by testing, a comparison with competitor products and benchmarking. The tools are then continuously developed by the supplier. After testing, the new tools gradually enter the catalogue. “We mainly sell standard tools. But we do offer a few special tools too,” summarises Rossaint.
The Technology Center that opened in Munich in September has been equipped with extensive measurement and testing equipment, demonstration and training facilities. Ultimately, the question is why might a tool be good or bad? The structure allows conclusions to be drawn about tool performance. “We’re not interested in trial and error, instead we want to take a targeted approach to development and optimisation,” explains Rossaint.
If customers want to see tools live in action, they can sign up for this through field sales and an appointment is arranged. In the Technology Center visitors can see everything live in action on the machine. The training sessions always include a practical component, and this is where the new WFL Millturn takes centre stage.
In addition to the turning-boring-milling unit with B and Y-axis, the counter spindle machine is also equipped with a tool turret on the lower system. This means the machine can perform simultaneous turning on both spindles and perform 4-axis turning on one spindle. Five-axis machining is also possible with the turning-boring-milling unit and the C-axis. Thanks to a steady rest on the tool turret and a tailstock function for the counter spindle and tool turret, longer shaft components can also be machined. Transfer to the counter spindle means that parts can be fully machined in just one clamping operation.
Making anything possible
The Hoffmann Group also needed to test as many different tools and technologies as possible. It was also important that newly developed tools could be tested. “It’s a huge advantage to be able to test large inserts without immediately bringing the machine to its knees. The flexible clamping options mean that we can also use larger diameters with ease to extend tests and obtain more data. With the WFL, we can now perfectly test HSK-63 turning tools and thereby optimise our portfolio. The B-axis is also a huge plus during turning, as we have great flexibility for adjusting the entering angle. When our field sales staff come back with various customer requests, we can reproduce practically any situation, from VDI40 on the tool turret to any tool in the turning-boring-milling unit at any possible angle. The milling spindle was designed for 16,000rpm, so we are also well equipped for future requirements.” Since the start of 2020, almost 400 customers have visited the machine. The field sales staff also take frequent advantage of practical testing opportunities with customers.