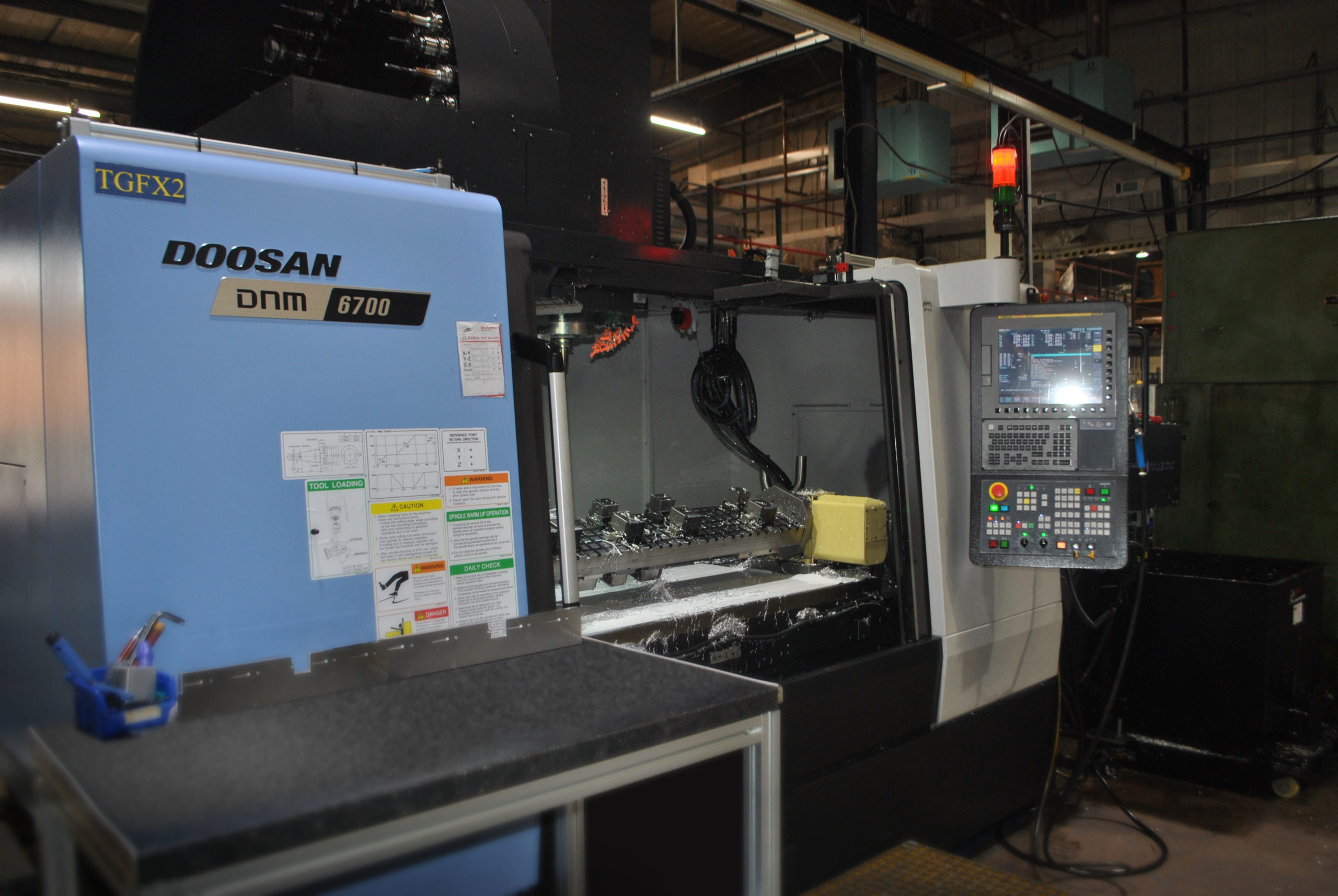
In the last four years, HepcoMotion has installed six new Doosan/DN Solutions machine tools from Mills CNC to strengthen the company’s in-house machining capacity.
Mills CNC supplied HepcoMotion, a leading manufacturer of linear motion systems that is part of the Hepco Group of companies with six new Fanuc-controlled CNC machine tools. The machines comprise five DNM VMCs and this includes four DNM 6700 models where two are extra-long bed variants. These are accompanied by a DNM 5700 as well as a VT 1100M VTL with driven tooling.
The machines have been installed at the company’s Headquarters in Tiverton, which has a 4,800sq/m production facility with approximately 40 CNC machine tools organised into discrete production cells for the respective milling, turning and grinding technologies. The Tiverton site also boasts a sizeable assembly operation, a heat treatment facility, a dedicated ring cell and a linear slide processing line. It is here that cutting, straightening, chemical blacking and grinding operations are undertaken.
Taking a closer look at the company, HepcoMotion’s Engineering Manager Mr Ryan Berry says: “We are a vertically-integrated, self-sufficient company. Controlling the methods and means of production in-house helps make us more agile, cost-competitive, productive and better able to meet the needs of our domestic and overseas customers.”
With its linear and rotary guide systems that feature the company’s innovative V-Guide technology, HepcoMotion is a world leader in linear motion technology that is utilised by specialist machine builders, systems integrators and end-users across a wide range of industry sectors.
As Ryan Berry continues: “We are always looking to improve and regularly monitor and benchmark against KPIs to identify areas within our manufacturing processes that need to be strengthened. When and where issues are identified, we act quickly and decisively to address them – investing in new technology as required.”
To help meet the growing worldwide demand for its linear motion technology solutions, HepcoMotion made its first investment in Doosan machine tools from Mills CNC in 2019. As Ryan adds: “We needed to increase our in-house milling capacity and capabilities, primarily to machine high-accuracy aluminium components used in our linear motion systems. We also needed to upgrade our ring cell where we machine large-diameter circular rings for our PR2 curved rail and track systems. These are made from steel and stainless steel plate and forgings. Although we had not previously invested in Doosan machine tools from Mills CNC, we knew that both the machines and the company had a good reputation in the market. As part of our decision-making process, we approached Mills with our requirements and were introduced to technical, applications and service staff within their organisation as well as having technical presentations on the machine tool solutions recommended. In this instance, a DNM 6700XL for our milling department and a VT 1100M vertical turning lathe for the ring cell.”
The DNM 6700XL is a rigidly built, large-capacity 3-axis VMC equipped with a BT40 spindle that has an 18.5kW 12,000rpm spindle motor. To meet HepcoMotion’s specific production requirements, the machine was supplied with through-spindle-coolant capability, a 4th-axis interface and Renishaw probing systems.
Says Ryan Berry: “The DNM 6700XL has a good-sized worktable with an extended X-axis stroke that enables us to machine large and/or multiple smaller parts in one set-up. The integration of a 4th-axis rotary table has increased our flexibility and, as a consequence improved productivity.”
Such has been the reliability and high performance of its first DNM machine, acquired back in 2019, that the company has subsequently invested in another four DNM machines in the last three years. These include models with 4th/5th-axis units and one with linear scales.
Discussing the VT 1100M large-capacity 32” chuck vertical turning lathe, Ryan continues: “The VT 1100M has helped improve part accuracies and increase our process reliability. The driven tooling capability means we can mill ID and OD features quickly in one set-up without having to transfer parts between machines.”
The six Doosan/DN Solutions’ machines installed at HepcoMotion’s machine shop are in constant use, operating 24/7, machining components in a range of batch sizes from prototype up to 500-off. Mills has also supplied a sister company, Braintree Precision Components (BPC) in Essex, with three turning centres over the last nine years, further cementing its preferred partner status with the group.