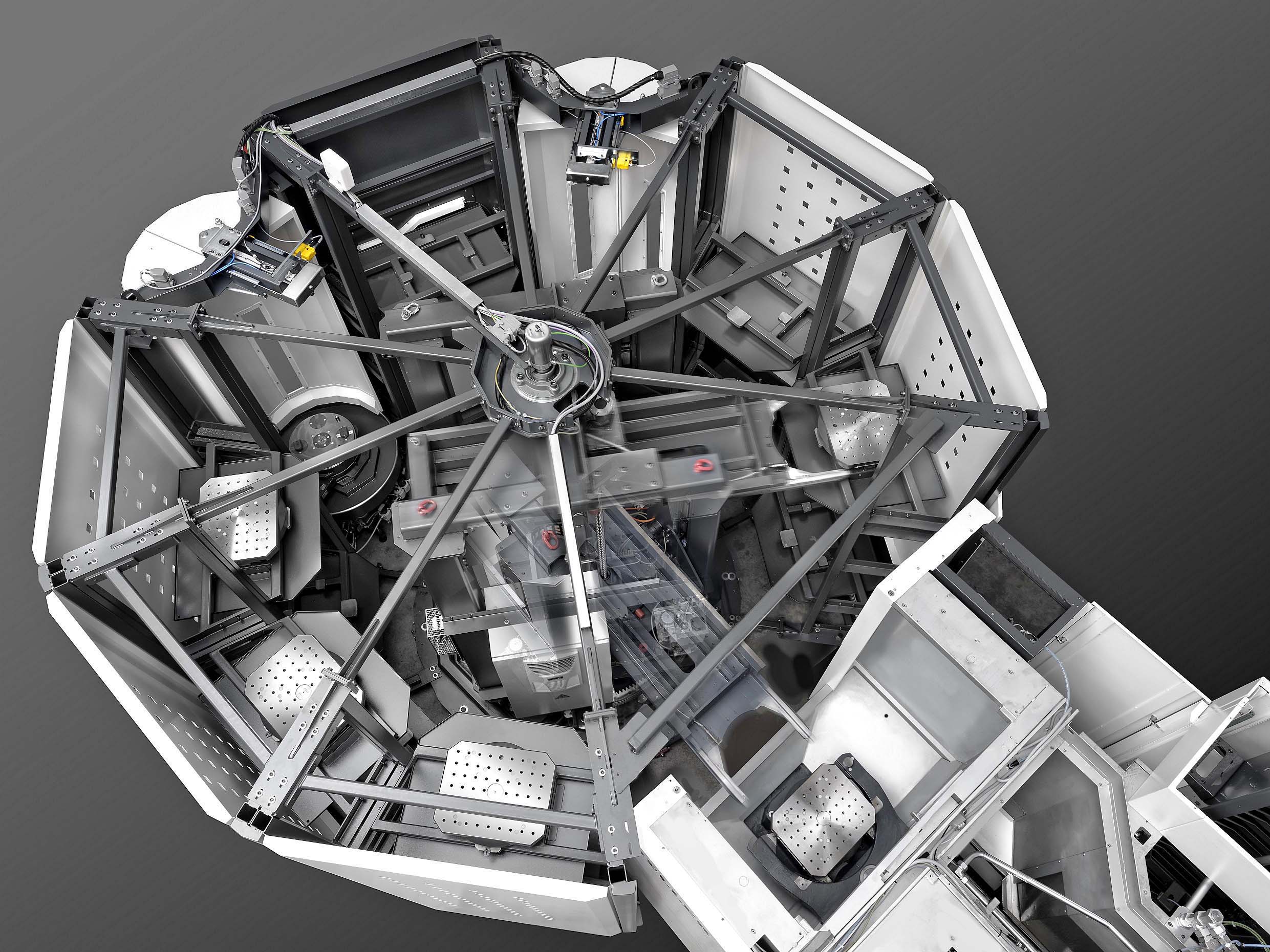
German-owned Heller Machine Tools whose factory in Redditch produces selected 4-axis and 5-axis horizontal machining centres will stress at MACH 2024 that this facility places it in an excellent position to provide customers with an elevated level of applications and service support. Celebrating its 50th anniversary in 2024, it is also a global competence centre within the group for top-level turnkey projects.
360-degree solutions is Heller’s name for its pre and post-sales services. Based on this principle, it provides users with solutions to maximise machine availability and productivity, helping them to produce parts reliably and at a competitive cost per part.
The holistic Heller service includes time studies which are accurate to ±5%, evaluation of requisite workholding, consideration of automation and unmanned running requirements, built-in chillers for cooling the machine elements if they are required to achieve tolerance, tool life monitoring and broken tool detection.
A particular focus at the show will be Heller’s ability to supply turnkey cells for highly efficient machining of tough titanium and nickel superalloys, notably in the aerospace industry. In this connection, the machine manufacturer will stress the considerable range of different spindles that it manufactures in-house to suit a vast range of applications.

For example, the HMC on the stand will be an HF 3500 second-generation 5-axis model for which it is possible to select a DC (dynamic cutting) universal direct-drive motor spindle, rated at either HSK-A63 16,000rpm 56kW 180Nm or HSK-A100 12,000rpm 45kW 400Nm. There is also a PC (power cutting) spindle rated at HSK-A100 10,000rpm 45kW 360Nm and an HSK-A100 13,000rpm 45kW 228Nm SC (speed cutting) spindle. Two further options with an HSK-A63 interface are rated at 12,000rpm 45kW 228Nm (PC) and 18,000rpm 45kW 103Nm (SC).
The 5-axis machine has a 710 by 750 by 710mm working volume. In this case, the machine will be exhibited without a DDT (Direct Drive Turning) rotary table and spindle locking function for turning tools.
To raise cutting performance, the Gen 2 design has a short distance between spindle nose and the centreline of the 225-degree swivelling trunnion and is available with twin motors and ballscrew drives for moving the trunnion/rotary table in the Z-axis, with position feedback via linear scales. The high-end PRO package offers more than 1G acceleration in all linear axes.
Engineers will be on the stand to discuss the benefits of the new F 6000 5-axis mill/turn machining centre launched by Heller at the last EMO trade show, held in Hannover. It has been designed from the ground up following extensive research carried out amongst the manufacturer’s customer base.
Highlights of the new generation include new swivelling heads with integrated motor spindles d and an optional direct-drive torque table for carrying out in-cycle turning operations. A pallet changer is included, enabling easy integration later on of a rotary or linear pallet storage system.
To ensure that all of the above benefits are maximised in production, Heller’s design engineers have focused on clear and easy operation, as well as good accessibility to all work areas. Operation is simplified by the new Siemens Sinumerik ONE control, which is fitted as standard, and the convenient control unit in panel design with a 24-inch touch screen. At the same time, better access to the work area and the optional new SETUP-Assist software make it easier to prepare for the next machining process.
The main purpose of automated manufacturing in production centres is the reduction of idle times to optimise system availability. For this purpose, Heller offers proprietary automation solutions that can be optimally combined with its HMCs.
Featured at MACH 2024 will be Heller4Industry, the group’s worldwide drive towards integration of its machine tools and controls into the Industry 4.0 environment. Within the multi-faceted portfolio is the HELLER4Services interface, which focuses on the transparency of digital manufacturing and maintenance. The module forms the basis for evaluating machine data and statistics to reduce downtimes. Additionally, visualisation of specific information such as status displays of axes and spindles enables a user to predict wear and implement preventive maintenance.
Subscribe to the MTDCNC Newsletter
Subscribe to our Newsletter today!
Stay up to date with the latest industry news and events.
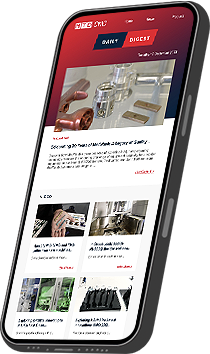