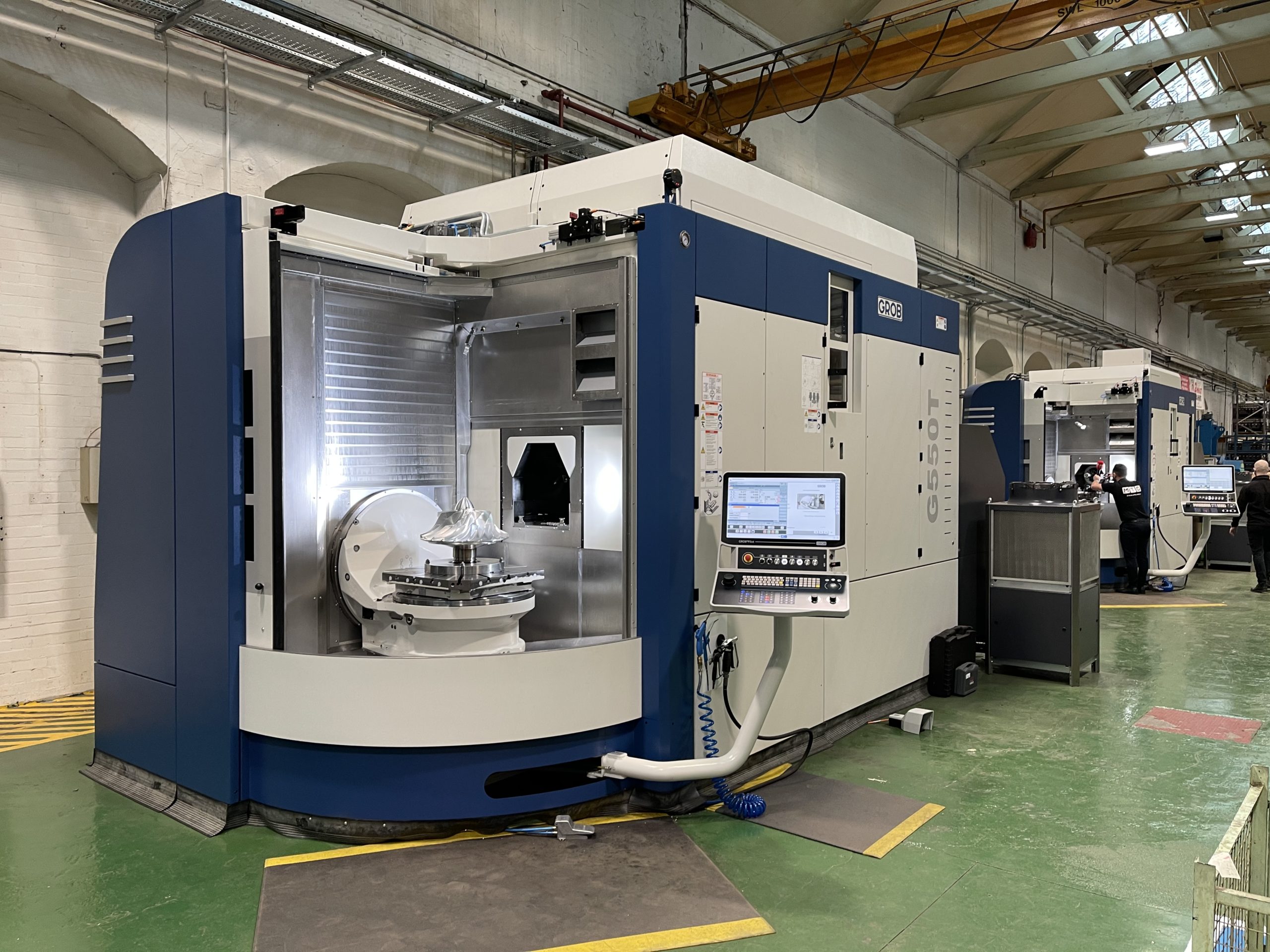
As a turbocharger manufacturer for the power generation and marine sectors, Napier Turbochargers produces the complete system from the rotating equipment, compressors, inlets and outlets and the casings. To improve productivity, the company has recently invested in two GROB machining centres – MTDCNC travelled to Napier Turbochargers headquarters in Lincoln to find out more.
The aim for Napier is to generate market-leading pressure ratios to provide customers with more power and efficiency than ever whilst lowering fuel consumption and emissions. This involves exceptional levels of innovation as well as an ability to machine everything from aluminium and inconel through to steel, castings and much more.
Discussing how components were made before the arrival of the new GROB G550T and GROB G350T machines, Dan Severn from Napier Turbochargers says: “We were doing milling and turning with a total of nine operations and the GROB machines have enabled us to reduce that to 6 operations. This is due to the flexibility the machine gives us with the mill/turn option. This gives us a lot of savings across the board on tooling, processes, operations – everything.”
Alluding to the decision-making process behind buying the GROB machines, Dan says: “We set ourselves pretty ambitious goals of where we wanted to get to. We reached out to a lot of the big manufacturers, and we also picked up the GROB leaflet at a ‘Seco Innovation’ event a couple of years ago. We had the leaflets in the office for some time and we eventually contacted GROB, an engineer visited us on-site and we discussed what we wanted to achieve. From there it snowballed, we soon had the applications guy on-site and then I visited the company to look at the GROB G550T.”
Discussing an impeller that is being machined on the GROB, Dan continues: “The impeller is immensely critical to the overall turbocharger and performance. This means that from a machine tool, we are looking for high accuracy and high-performance machine tools – and GROB fits very well. The ability to turn and mill on the same machine really was a lightbulb moment when we were looking at the machine. Turning is not just a bolt-on it is a fundamental aspect of the machine. With the GROB G350T and G550T, we can cover a lot of different size parts and the options of the machines are limitless. The machines are flexible, so if the product range changes, we can turn any feature that we like and we can part probe very accurately – the flexibility that GROB gives us is immense.”
Taking a closer look at the 5-axis machines with turning capability, Matthew Harrison, a fourth-year technical apprentice at Napier Turbochargers says: “Our greatest driver for investing in these machines was cycle time reduction and improved flow and efficiency. The machines had to be quick and efficient, but they also had to maintain the micron level accuracy that we chase. For example, the impellers we machine were previously done in nine operations, and this is now down to 6. This is credit to the machines being able to amalgamate certain operations and actually remove some operations from the process flow. This has resulted in set up reductions in the aluminium 2816A forgings, we would like to produce the parts in fewer operations, but there are restrictions such as movement of the material. So, we have to rough the components and let them move, and then tie in all the dimensions for finish machining.”
Commenting on how much of a game-changer the 5-axis machining with turning capability is, Matthew Harrison continues: “It has given us a massive flexibility improvement. The existing equipment was stand-alone machining centres and turning centres but bringing all that together in one machine and reducing set up times has been amazing. As for the simultaneous 5-axis capabilities, we have some pretty solid limitations on how we can machine parts, but the rigidity of the GROB machines and the spindle is second to none. During the process of installing machines, we have also moved to a new software platform for programming. This has introduced us to new process cycles, so it has been a little bit of a steep learning curve – but we are certainly getting there.
“The service and backup throughout have been absolutely faultless. From the initial conversation through to the arrival of the machines, the GROB guys have been amazing,” concludes Dan Severn.