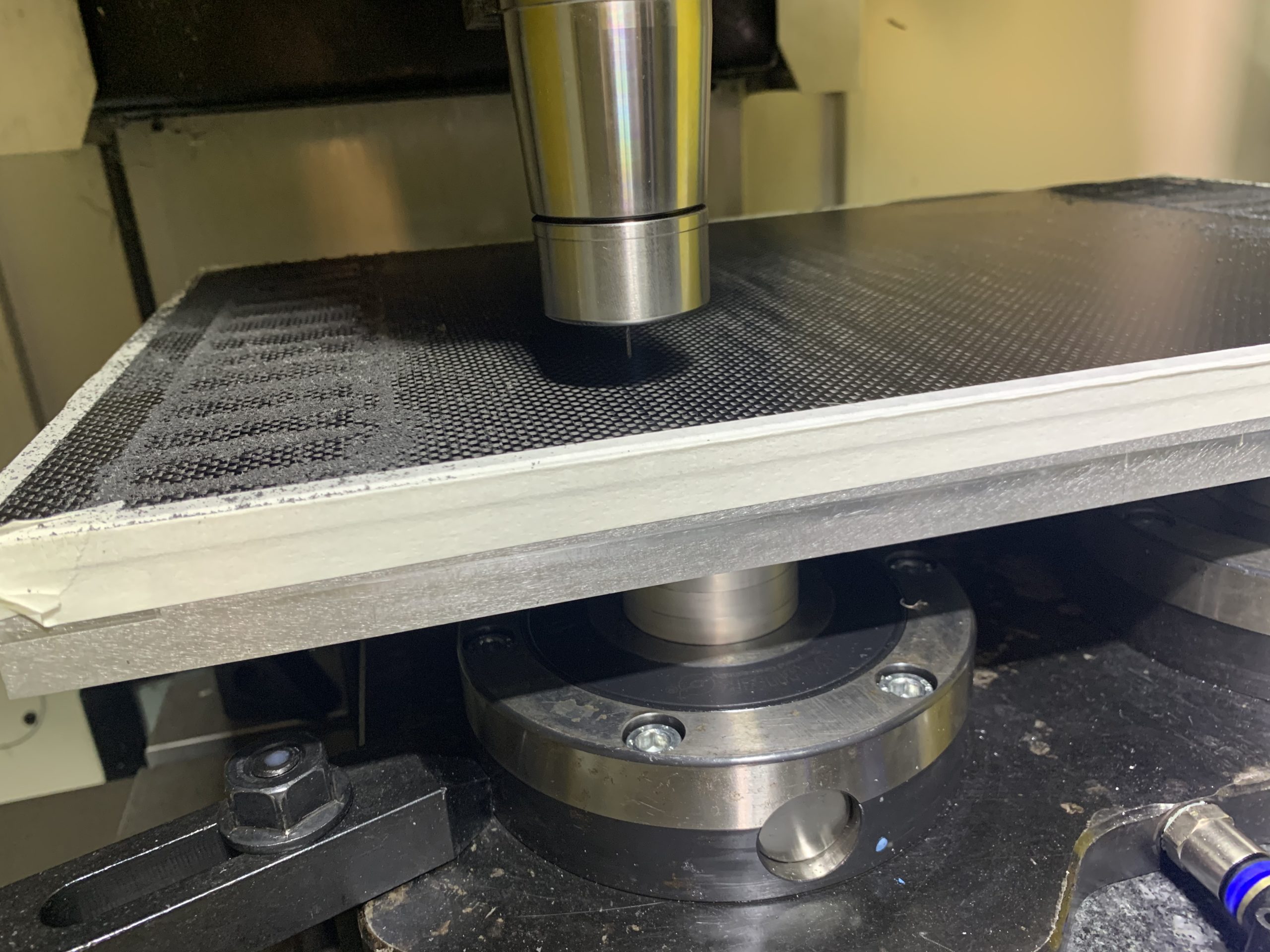
Claiming to be the UK’s only specialist motorcycle and scooter gasket manufacturer, Showe Performance is a specialist in manufacturing gaskets in virtually any material, shape or size. Utilising the latest digital presses, portal milling machines and traditional presses, the West Midlands company has just installed its first CNC vertical machining centre, a FANUC Robodrill D21MiB5.
Showe Performance has created over 4500 bearing and seal kits with over 625,000 make, model and year fitments available for customers to choose from with an in-house manufacturing facility that can produce bespoke gaskets in thicknesses from 0.05mm up to 20mm and dimensions up to 1.6m by 1m with a precision level of just 0.005mm. The Stourbridge company also manufactures bushes, spacers, impellers and a host of other engine components.
Asked why the company installed the FANUC Robodrill D21MiB5, Brett Showell from Showe Performance says: “We bought the machine for several reasons. The spindle speed was one reason, as some of the materials we cut require a high spindle speed. It also has a flexibility that allows us to control and automate processes with the control system. We have only had the machine for a couple of months and the FANUC 31i-Model B5 CNC control system suits what we do. Within less than 10 days of the machine being installed, we were up and running and producing parts.”
Commenting on what parts the company makes on the new FANUC Robodrill D21MiB5, Mr Showell says: “We make copper gaskets, re-valve petals, water pump impellers, spacers, bushes and more. We use a vacuum table for a lot of our components such as small thin carbon fibre parts. This setup allows us to batch cut a lot of parts and the CNC control enables us to program the parts in this way.”
The compact FANUC Robodrill D21MiB5 has an X, Y and Z-axis travel of 500 by 400 by 330mm with a table size of 630 by 400mm that is perfect for the small to medium size components that are produced at Showe Performance. The FANUC Robodrill D21MiB5 machine offers a programmable cutting feed of up to 30m/min with a rapid traverse of 54m/min and end users can select a suitable spindle with a 10,000rpm 80Nm and 14.2kW version or a high-speed 24,000rpm 35Nm 26kW spindle.
The company is also adopting automation, referring to this Mr Showell says: “We are using a gripper that allows us to pick parts off a pallet tray and put them into a vice. This clamps the parts and machines them and then they are popped back onto the pallet. This allows us to do anything from 20 to 70 components in a single go.”
“The reliability of FANUC is particularly important to us. The machine has been fast and reliable and the control is easy and sensible to use. If we purchased another machine it would certainly be another FANUC Robodrill. Additionally, we had a day of training with FANUC and they answered all of our questions. Our contact has been there for telephone and email support ever since the machine has been installed.”