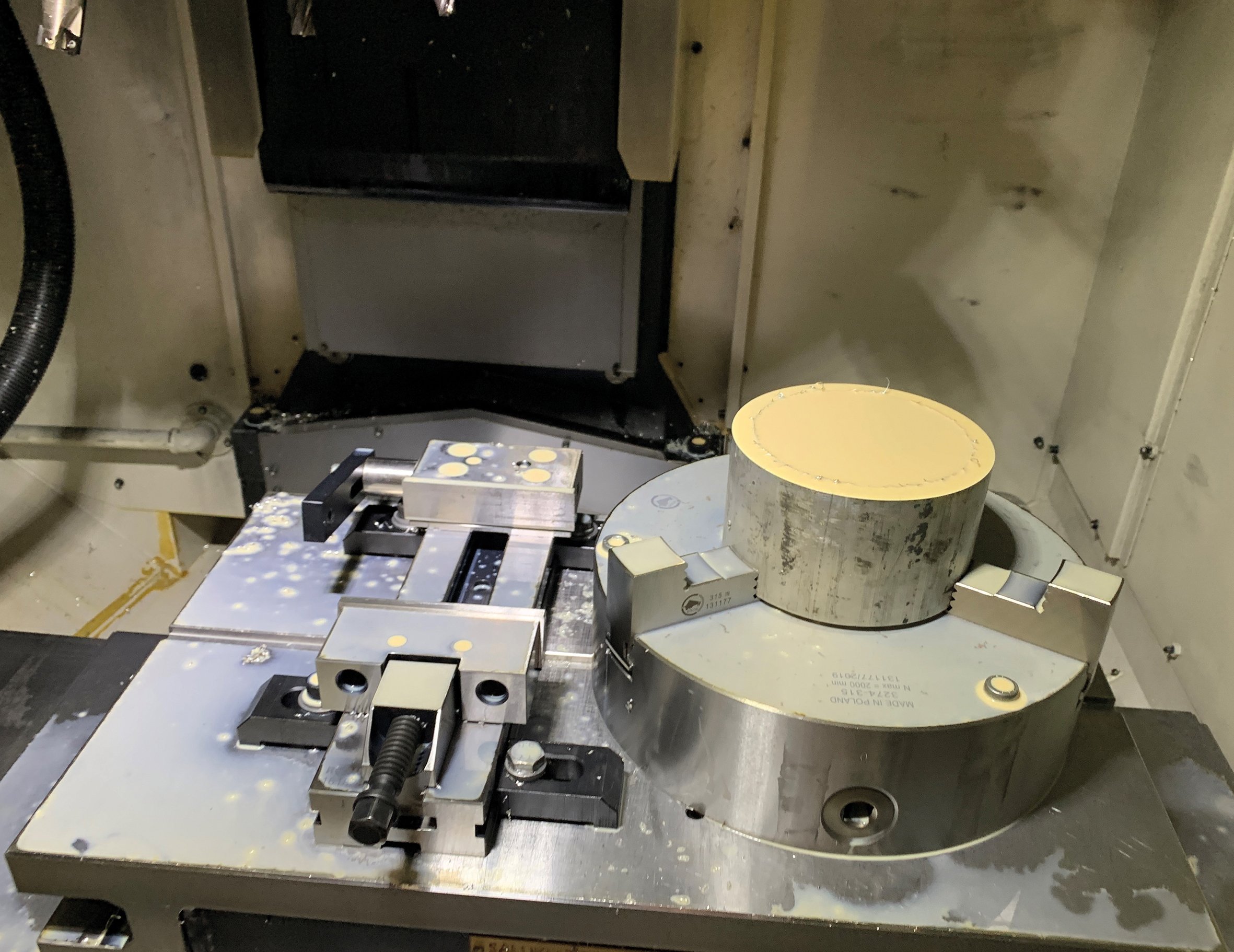
Founded in 1946 to undertake subcontract electric motor repairs, Stoke based Fletcher Moorland recently bought its first vertical machining centre, a FANUC ROBODRILL. MTD visited the company to find out more.
Commenting upon the back story, Matthew Fletcher says: “Fletcher Moorland was a company started by my grandfather in 1946, and three generations later, I am running the business. Primarily a repair company, we work on electric motors, air handling units, pumps, fans, gearboxes and we also have an electronic section where we undertake electronic repairs such as servo drives, inverters and PLCs. Companies all around the UK use us for repairs in a breakdown situation.”
Looking into the reasons behind buying the FANUC ROBODRILL machine, Matthew says: “We often have requests from customers to manufacture parts that either they couldn’t make or there were long delivery times. We have traditional machine tools here and with these machines, it would take too long to machine parts for customers. The only other solution was to subcontract parts out to the suppliers. We made the decision to bring this service ‘in-house’ and the FANUC ROBODRILL proved ideal for what we want and how we can serve our customers.”
“We invested in FANUC, as it is such a well-known brand and we already have a well-established relationship with the company and the people there. We also repair FANUC equipment in our service department, so it naturally seemed to be a good fit.”
Taking a closer look at the high-powered version of the ROBODRILL D21MiA5 at Fletcher Moorland, machine operator Matthew Chidlow says: “It’s an amazing machine as it allows you to improve productivity times. What makes the FANUC machine more productive is the speed that it moves from position to position when it is not cutting. This allows us to move around the part a lot quicker reducing non-cutting times.”
“The majority of the material we machine here is aluminium and soft steel, but the machine allows you to do harder materials like D2 tool steel and it will perform like it is cutting aluminium. The fact it has a BT30 spindle configuration makes no difference, there is no vibration in the machine,” says Matthew.
Looking specifically at the spindle, programming and the reverse engineering the company undertakes, Matthew says: “The maximum operating speed is 10,000rpm and we have MasterCAM software that drives the machine with two CMM’s for inspecting our components. With regards to reverse engineering, a customer will ask us to re-engineer a part and what we will do is sit down measure the part and then put it onto our MasterCAM system by drawing it, generating a program and adding the tools to the process for use in the ROBODRILL.” The machine operates with the FANUC 31i Series Model B5 CNC control system that makes daily operation an easy task, as Matthew continues: “what we ask the machine and the software to do, it does! We can machine to very tight tolerances and with regards to cleaning and in machine maintenance, the flood coolant washes all the chips away from the work area and this reduces our need for swarf management.”
Concluding on the ROBODRILL D21MiA5 at Fletcher Moorland, Matthew says: “It’s a small and very reliable machine that is very compact and this allows production times to be reduced, so we can get the parts of the machine a lot faster.”
Giving his final remarks on the machine, Company Director Matthew Fletcher states: “The machine is a success, but we are still in the very early days at the moment and we are still learning. We employed a guy specifically to run this machine and what I wanted to do is to run 1-off, 5-off and small batch runs and volumes for our customers; essentially producing small volumes with high value. The machine is also a business case, where we are putting our sales team on the case to bring business in to us. It may be our first CNC machine investment, but I would like this to grow and so far the results are positive.”