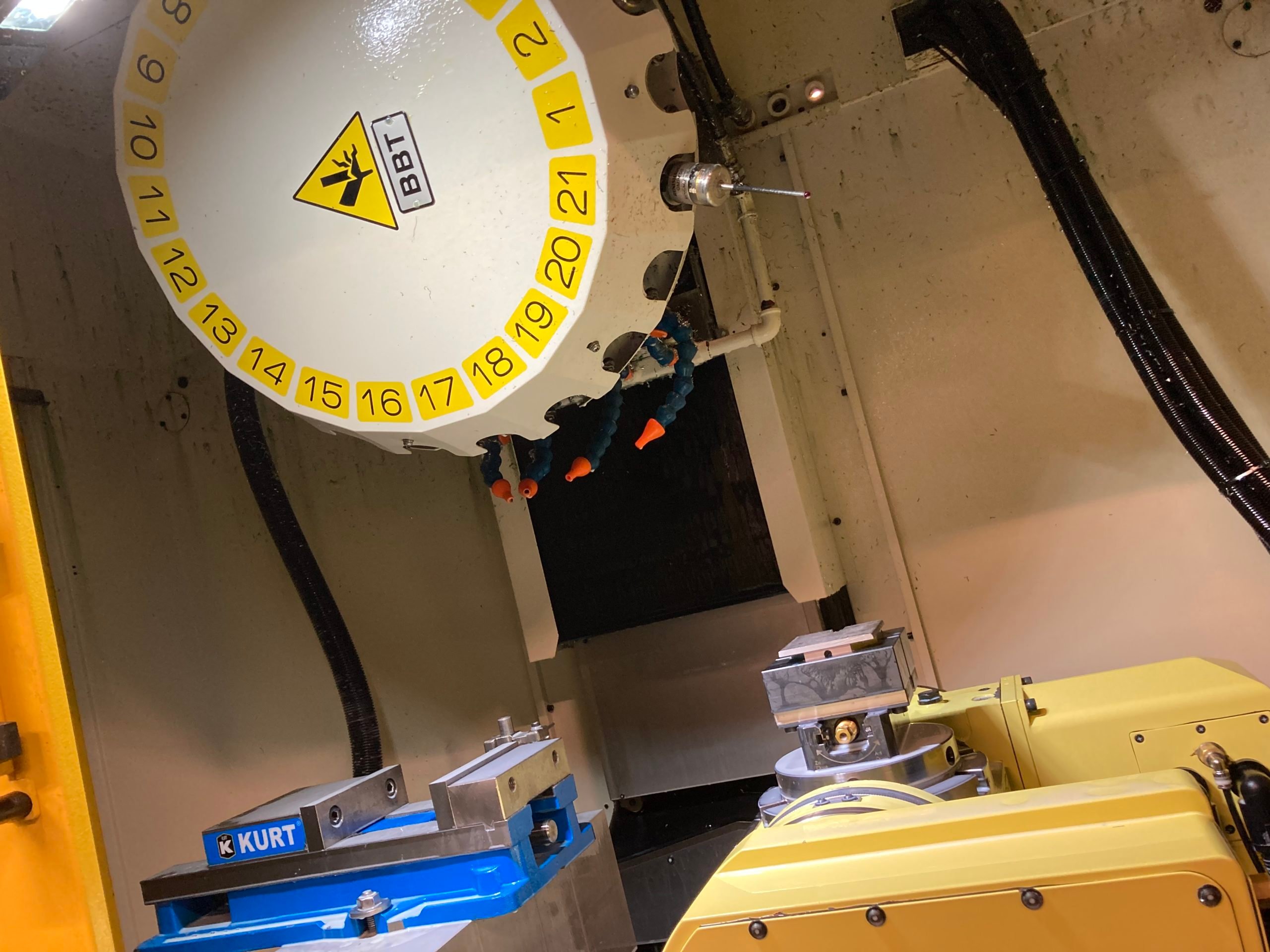
Founded in 1984, Apsley Precision Engineering Ltd was founded by Graham Aymes who had swiftly secured several defence contracts with customers that remain with the business today. To ensure the company remains competitive and flexible, the Salisbury-based subcontract manufacturer to the aerospace, defence and medical industries has recently invested in a ROBODrill D21LiB5 machining centre from FANUC.
Discussing why the company opted for the ROBODrill D21LiB5, Peter Aymes, the Managing Director of Apsley Precision Engineering says: “The ROBODrill has increased our machining capacity because it has a much higher spindle speed than our other machines and we have integrated a 5-axis unit with it as well. The ROBODrill is the fastest machine on our shop floor, it has a 24,000rpm spindle, through spindle coolant and a very fast chip to chip speed. With a BBT30 spindle, I was surprised by how powerful it is. We are machining tool steels, stainless steels, aluminium and any material that comes in front of us.”
“From the investments we have made over the last five years, we can supply 5-axis machined components, mill/turn components and anything else underneath. 18 months ago, we bought the ROBODrill because we were looking to shorten our cycle times. With a 24,000 rpm spindle and Nikken 5-axis unit, it has made a difference to our business. FANUC has an excellent reputation and their ROBODrill has been on the market for many years, and that is why we chose to go for this machine and go for an upgrade to the rest of the machines in our shop floor.”
With a BBT30 being smaller than the BBT40 spindle variant, Peter says: “The performance has surprised me. It can take really deep cuts just like you can on a BT40 machine – with the BBT30 spindle, it is extremely rigid. We run aluminium on the ROBODrill most of the time. However, it is perfectly suited to any other material that goes through the shop. So, today we are running tool steels and last week we were running 316 stainless on the machine. There is the assumption that BT30 spindles are not up to the job, but we have had no trouble at all when running all of those difficult materials on the ROBODrill.”
This rigidity is a credit to the BBT face and taper dual spindle contact system that demonstrates rigidity, stability and precision beyond that of standard BT spindle configurations.
“We initially bought the machine as a 3-axis but then decided to add a 5-axis unit to it. That gives us the facility to complete components in a single operation as we have a fixed vice on one side of the bed and a 5-axis vice on the other side. This gives us incredible flexibility. I have taken parts from our other machines and put them straight onto the ROBODrill and it has proven to be extremely robust.”
Regarding the impressive speed of the ROBODrill, Peter continues: “The spindle runs 24,000rpm and it is the fastest spindle on our shop floor. This has enabled us to knock 40% off many of our cycle times. On the subject of speed, the tool changer is incredibly fast. It has a rotary carousel on there and that means the tool changes take just over one second, in some cases that alone has taken minutes of our cycle times.”
“The price of the machine is competitive, the cycle times are very short and that means that we get more value for our money. The return on investment for this machine has been much better than other machines that are comparable in the market, just because it is so much quicker. This means that we can get components off the machine faster and out to customers sooner than we would do otherwise. In terms of the size of the machine, it has a smaller footprint than a lot of comparable machine tools and this means that we can get more machines into the space that we have.”
“FANUC has been great at supporting us with this machine, the spares are readily available and the service engineers come out as soon as you need them. I’d recommend the FANUC ROBODrill because it is super fast, super accurate and excellent value for money,” concludes Peter.