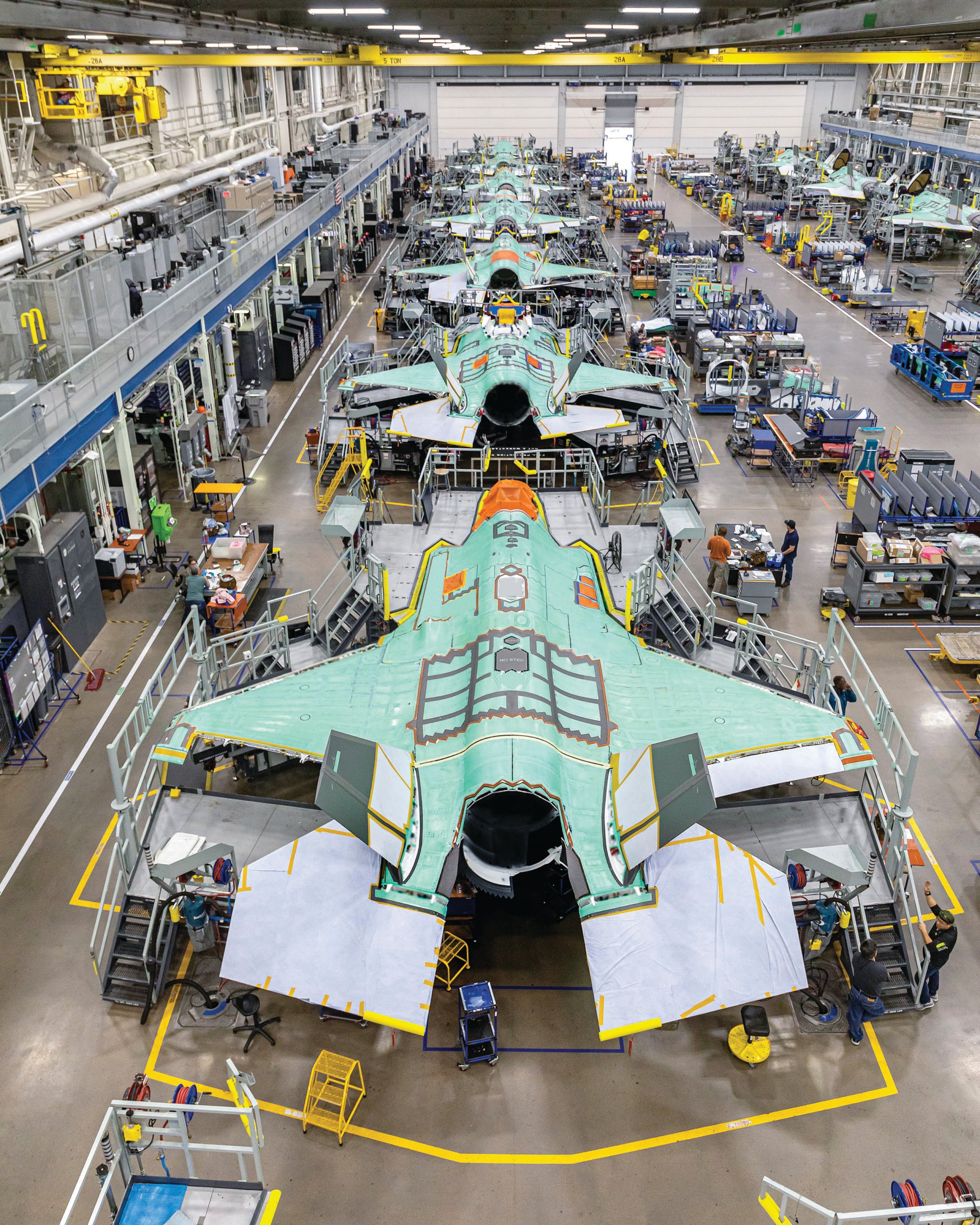
The Lockheed Martin F-35 Lightning II combat aircraft is a long-range supersonic fighter with stealth capability that enables it to evade detection and enter contested airspace. The F-35 also provides impressive connectivity, serving as a communications gateway to share its operational picture with allied ground, sea and air assets. On the ground, the same characteristics of speed, connectivity and technology are recognisable in the manufacturing operations of this fighter.
As the prime contractor for the F-35, Lockheed Martin works with a global supply chain of more than 1,900 companies based in the US and the 13 nations acquiring the aircraft. Lockheed builds the forward fuselage and wings in Fort Worth, Texas and the evolution of machining operations for the cockpit-area forward fuselage understructure demonstrates Lockheed Martin’s commitment to continuous improvement.
Almost five years after the first F-35s were produced in 2006, a multi-day Kaizen event examined the overall manufacturing process for improvement. Jeff Langevin, Manufacturing Technology Fabrication Lead, said the Kaizen sessions showed the transport and ergonomics of readying the fuselage for machining and drilling operations were not value-adding. “Moving aeroplane parts around a factory and transferring NC programs are interface tasks that don’t necessarily build aeroplanes, but they impact our ability to do so efficiently.” The original process used an overhead monorail system to pick up and move the fuselage and present it to different machine tools. Each move required a crane operator and personnel on the shop floor to rig the fuselage, rope off areas and shut down sites under the lifting path to assure shop floor safety. Transporting the fuselage section in and out of the machining locations required about ten moves between machines, including working above and below the fuselage, setting up step stools, ladders, scaffolds and platforms for technician access, as well as washing the fuselage clean of debris.
The team worked with factory automation systems provider Fastems to blend the machining and transfer operations into an integrated machine tool transfer line (MTTL), using flexible manufacturing system (FMS) technology. On the MTTL, a fuselage section is lifted into a Load, Unload, and Skin Installation (LUSI) station. The LUSI station, also built by Fastems, makes it possible for a single worker to raise, lower and spin the fuselage. Operators stay at floor level without climbing over or under the fuselage and can manipulate it to positions necessary to carry out operations. Before the Fastems line was installed, a move from the LUSI station to the wash station took hours and required multiple personnel. Now, the move takes two or three minutes and requires just one worker to push a button.
After this, an FMS stacker crane carries the section down the production line to a house-sized Parpas America Precision Milling Machine (PMM) that mills and drills the understructure of the fuselage to accept the F-35’s composite skin. Following that, the MTTL delivers the fuselage section to a Fastems-designed wash station where machining debris is washed off and dried. Then the transfer line takes the fuselage to a LUSI station where side skins are attached. Following this, the fuselage goes to a FIVES Group Auto-Drill that makes about 500 holes in each side of the structure and a tool preset booth monitors tool wear in real-time and dictates preemptive tool changes meant to avoid process interruptions. After that, the fuselage returns to the wash station and finally to a LUSI station to be prepared for the next step. Brian Sykes, F-35 Forward Fuselage Lead Specialist, said: “The forward fuselage team works hand in hand with the automation system to reduce time, increase accuracy and improve safety. We reduced hours per unit from 132 to 98 hours, which is a 34-hour or 26% saving. The number of monorail moves decreased from 18 to 2, and the system also improved ergonomics for mechanics’ manual drilling operations.”
The system was designed to be modular, with the understanding that it would be expanded as F-35 production increased. Phase 1, installed some 10 years ago, featured four LUSI stations, two PMMs, one wash station, one Auto-Drill, and a tool preset station. About six years later Lockheed added another Auto-Drill and a LUSI station. A third expansion added a third PMM. In the meantime, Fastems has continually developed its Manufacturing Management Software (MMS) that plans, runs, and monitors the production in the MTTL. Fastems worked with Lockheed’s technology group and workers on the line to assure that the integration is seamless and there is no downtime during system upgrades. Langevin said: “The MTTL shows our internal stakeholders and customers that we are committed to making the F-35 affordable. We want to add value to the program that goes beyond just machining faster. This means finding the areas of waste in between the machining processes and making things easier and safer for our workers. The Fastems system shows that there is a place for flexible automation in an aircraft assembly line.” There is now a 75% reduction in span time provided through the MTTL that enables Lockheed Martin to manufacture up to 20 Forward Fuselages a month.
Langevin continues: “The Lockheed/Fastems relationship truly does feel like a team. Sometimes we forget that we’re a supplier and a customer because we are working so closely together. We have a common goal to make things more efficient and that has helped us to take the transfer line to the next level and expand the system with minimal impact on our production.”
While in terms of hardware the MTTL has grown as far as possible, Lockheed and Fastems continue to work with the control software development and other ways to further understand how the system is operating and how efficiency can improve.
Lockheed has found opportunities to continue to work with Fastems in other areas of the manufacturing process. The aircraft plant is about to put into production a new Automated Structure Laser Cleaner (Auto SLC) system supplied by Fastems for the F-35 wing line. The system is based on a laser ablation scan head designed to automatically remove primers and other protective coatings from F-35 wing components. Auto SLC produces a pristine surface to which nutplates can be mechanically bonded without using rivets. The system eliminates manual sanding and solvent wiping that consumed significant time and yielded unbalanced results. Part of the companies’ ongoing relationship is a Fastems-proposed agreement in which it provided on-site support for the first several months of operation. “They are committed to giving Lockheed not just a piece of hardware but also something that’s going to help us take the next step,” Langevin said.