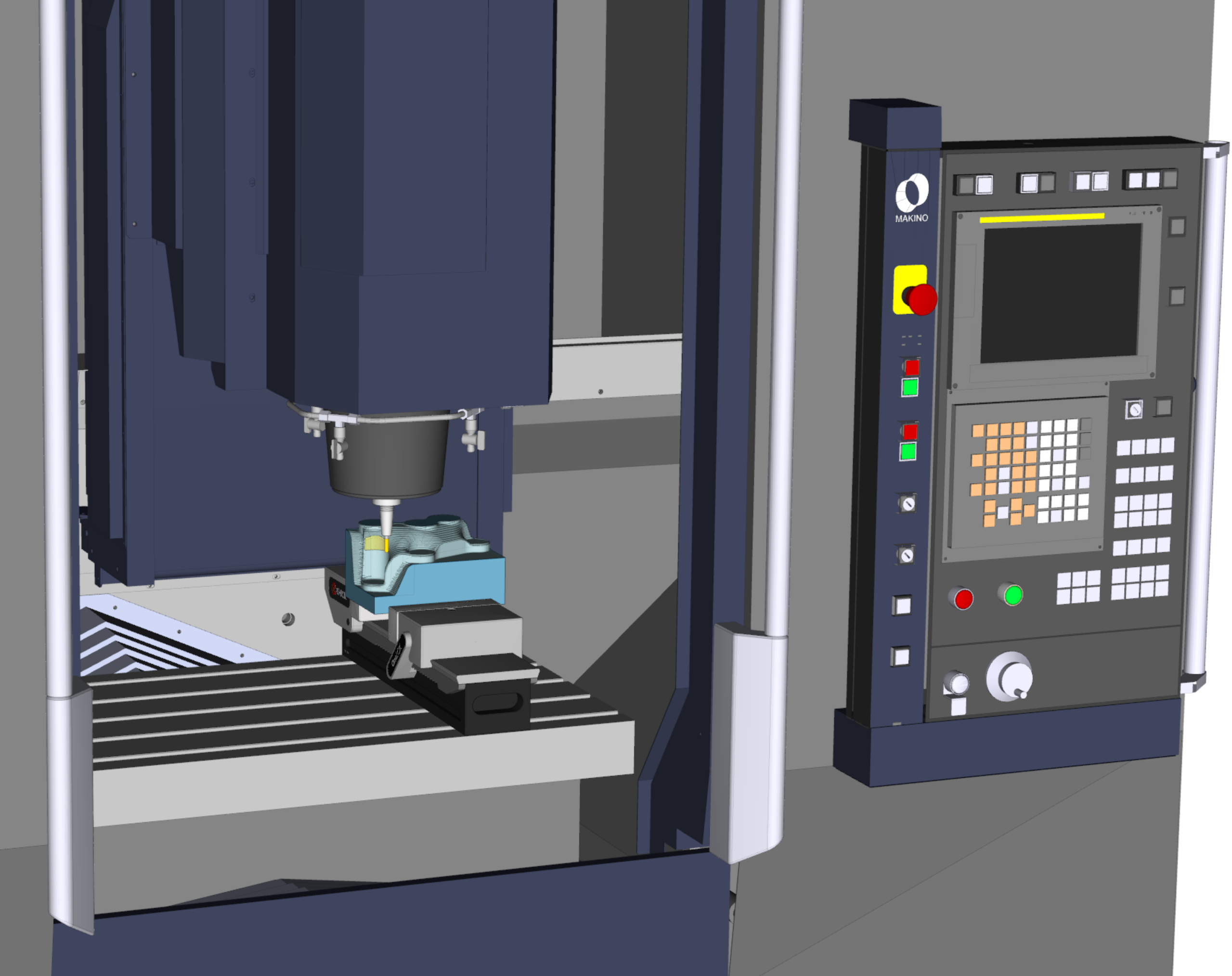
New CAM technology has been introduced by ESPRIT CAM to provide manufacturers with the flexibility needed to use multi-spindle and multi-channel CNC machinery for processing long parts. More accurate simulation of spindle transfers and bar pulls enables manufacturers to exploit multi-tasking machinery with high productivity program creation of error-free toolpaths.
Machining long parts like shafts and axles can be challenging because they require workpiece support to maintain cutting speed and surface quality. The main and sub spindles must be synchronised to ensure that cutting can be performed while both spindles hold the workpiece for maximum support.
Without the ability to track machine motion, a significant amount of time is spent hand-editing NC code and troubleshooting programs. Now, ESPRIT TNG CAM software automatically tracks the location of work offsets regardless of part position by enabling programmers to define the offset and offset translations or the points at which offset changes occur. Also, ESPRIT TNG eliminates the need for custom settings or calculations to the machine post to ensure that parts are machined accurately.
ESPRIT TNG now also enables manufacturers to perform face-milling operations with a unique ‘roll-in’ lead-in strategy recommended by Sandvik Coromant to improve surface quality, reduce cycle time, and extend tool life. The new release also offers productivity benefits for 3-axis operations. Toolpath creation is now 20 times faster, meaning that the toolpath that once took 30 minutes to generate can now be calculated in about two minutes.