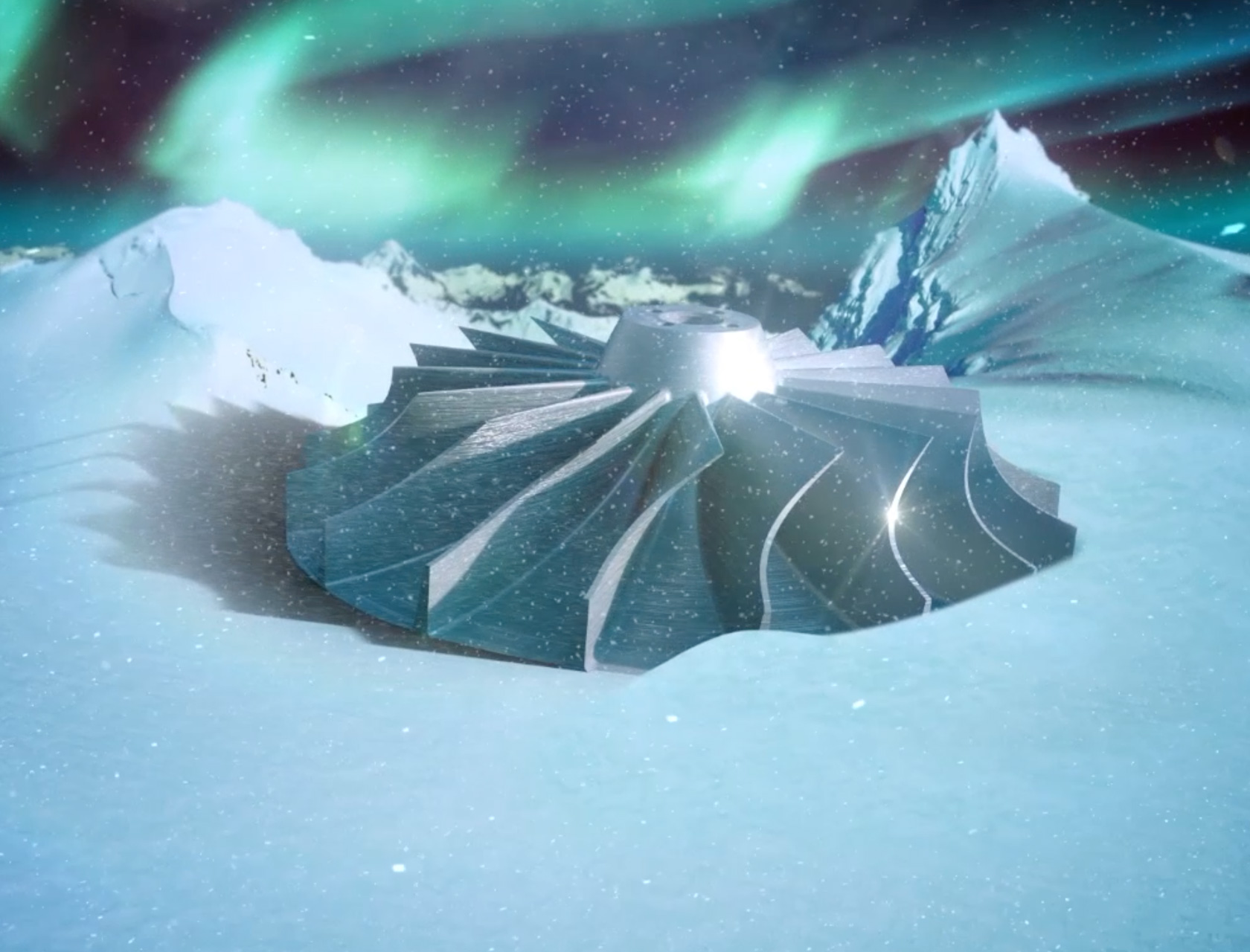
Having been entrenched in 3D printing and additive manufacturing (AM) for over 26 years, Dr Phil Reeves has wide-ranging expertise and experience of the industry. Tanya Weaver sits down with him to explore various themes and topics around AM. These will be covered over a series of articles in MTD magazine, the first one being ‘barriers to additive adoption’ and particularly what stops manufacturers from taking up this technology.
The AM market is a minefield. New machines and technologies are constantly being launched. Not only is it overwhelming to navigate all the various options, but businesses have to decide whether an investment in this technology is worth it and what benefits will be gained.
“Ultimately, the key barrier to AM is economics. For a manufacturing company, AM allows you to add another tool to your toolkit. But it is expensive technology and whether it’s polymers or metals, the economics of AM are still not comparable with traditional manufacturing. You can’t simply swap from one to the other. So, the question you have to ask is what’s the business benefits of adopting AM?” asks Phil Reeves.
“The business benefit could be that AM will help you grow your ‘Top Line’ because you’ll be able to make new products that you couldn’t make before or it will allow you to offer some sort of service that you couldn’t offer before, such as personalisation or customisation, or it’s going to help you grow your ‘Bottom Line’ by making you more productive,” he adds.
Before adopting AM, companies may have weighed up these benefits whilst others may have simply jumped onto the AM bandwagon without fully realising all that is involved in creating an AM part. Yes, you can redesign a part that takes full advantage of AM but there is a lot of work that goes into the production of a part, especially if it is metal.
“For instance, you need to work out how to orientate your parts on the platform, how to build them, how to post-process them, how to test them, how to inspect them… all these sorts of things. And then the question is, who pays for this? The manufacturer or the customer? I think there is a lack of understanding around that.
“I do also think there is probably an overcapacity of machines in the market because some manufacturers may have bought an AM machine under the assumption that there’s a very easy market to tap into. But what there is, is a difficult market to stimulate and you need a lot of people and a lot of skill sets and expertise to do it,” comments Reeves.
Of course, a part that has been manufactured using AM may be more expensive than a traditionally manufactured part. It may be a better part as it’s been redesigned to be better, but will customers pay for that? As Reeves says, selling the benefit of additive through the supply chain is something else that manufacturers are struggling with.
Another key barrier is the lack of standards for AM. “Currently, there are less than 30 globally published standards on additive. That’s all. So, until there are more standards that supply chains can use, you are taking a really big risk because suppliers want a guarantee that you can manufacture an AM part against a standard,” says Reeves.
“But things are changing. There are about another 30 standards in development, but of course, the development of standards takes time. I’m actually writing a specification at the moment for the British Standards Institution (BSI) on how to build a business case to adopt additive, but it’ll be a few months before it’s published, as it has to go through public consultation and review.”
Risk Adverse Industries
The lack of standards is really the icing on the cake for risk-averse industries because by adopting AM you’re not only using a new type of technology, but the material is also a new type of material because effectively the material properties are changed when put into an additive machine and also invariably the part has been redesigned to make it suitable for additive.
“This means that you’ve changed the process, the design and the raw material. So, everything has changed and then there are also no standards. So, understandably, for risk-averse industries, like aerospace and medical, there are far too many variables and that in itself are barriers to adoption,” says Reeves.
Of course, there are companies within these industries that have deep pockets and have successfully adopted AM. Using GE as an example, when it invested in AM a number of years ago the company did it not because it was new and novel, but it saw a real value in using a technology that would enable it to create really complicated geometries to improve the efficiency of its engines.
“GE realised how important it was to have this technology in-house, as it could make more efficient engines that could be sold at a premium and therefore justifying the cost of investing in additive. So, it all comes back to what are the business benefits? In GE’s case, it was making a more efficient product,” explains Reeves.
But then once the part has been produced additively, it has to be certified and this can be a really expensive process. For many, that is another barrier to AM adoption. However, there are machine suppliers that have a certified process. For example, Stratasys’ Fortus F900 Aerospace and F900 Pro is a large-build FDM machine that can produce functional, production parts in a resin material called Ultem 9085, which has been certified by the FIA and meets stringent test criteria and retains traceability required by the aerospace industry.
While barriers to AM are often thought of in the context of providing parts to customers, companies can also find opportunities to use this technology for internal purposes as a lean manufacturing aid. For instance, making customised workholding devices like jigs and fixtures. This is a great use of an in-house AM machine. It could also be used to produce other general shop floor tools and I think this is an undersold benefit of having a 3D printer in your business,” says Reeves.
But as Reeves concludes, before adopting AM, the manufacturer needs to think about how it will add value to its business. “If the company is currently machining metal, for example, they need to look at their products and ask whether by using a metal AM machine they could cost-effectively redesign that product to give their customer a better product? A better heat exchanger, a better fuel injector, a better part of a pump – whatever that object is, the question is whether it can be made better using the AM process and that’s where you get the value.”
Who is Dr Phil Reeves?
Phil Reeves is a leading consultant on Additive Manufacturing & 3D Printing (AM/3DP) business strategy and investment. Phil has worked in the field of AM/3DP for almost 25-years, having gained a PhD in the subject from Nottingham University in the mid-1990s. Since this time, Phil has worked in several AM/3DP related roles including R&D, business development, corporate strategy & consulting. In 2003 Phil founded leading AM/3DP consulting firm Econolyst Ltd which was acquired by Stratasys in 2015. Between 2015 and 2018 Phil was global Vice President of consulting at Stratasys, the world’s largest 3D Printing technology vendor & service provider. Phil is now the managing director at Reeves Insight Ltd, where he advises clients across the AM/3DP ecosystem, from user and vendors to investors and governments.
Phil is widely regarded as a thought leader in understanding the social, economic and environmental impacts of embedding metallic and polymeric AM/3DP into global supply chains. Phil has worked on a diverse range of projects to integrate AM/3DP into many industrial sectors, from healthcare to warfare, aerospace to automotive, computer gaming to consumer goods, and from recreation to education.
Phil’s clients have included many global fortune 500 companies such as Nike, GE, Danone, IBM, BMW, Tata, Boeing, BAE Systems, Merlin Entertainment, Virgin Atlantic, Sony, Unilever, FedEx, Carpenter, Johnson & Johnson and Philips, along with investors such as HSBC, Jeffries and Bank of America Merrill Lynch. Phil has also worked closely with other leading consulting organisations including Bain, BCG, Accenture & McKinsey.
In recognition of his contribution towards AM/3DP, Phil was conferred in the summer of 2019 by the University of Nottingham as the Universities honorary fellow for Additive Manufacturing Strategy.
Breaking the barriers to additive adoption
0:00 / NaN:NaN