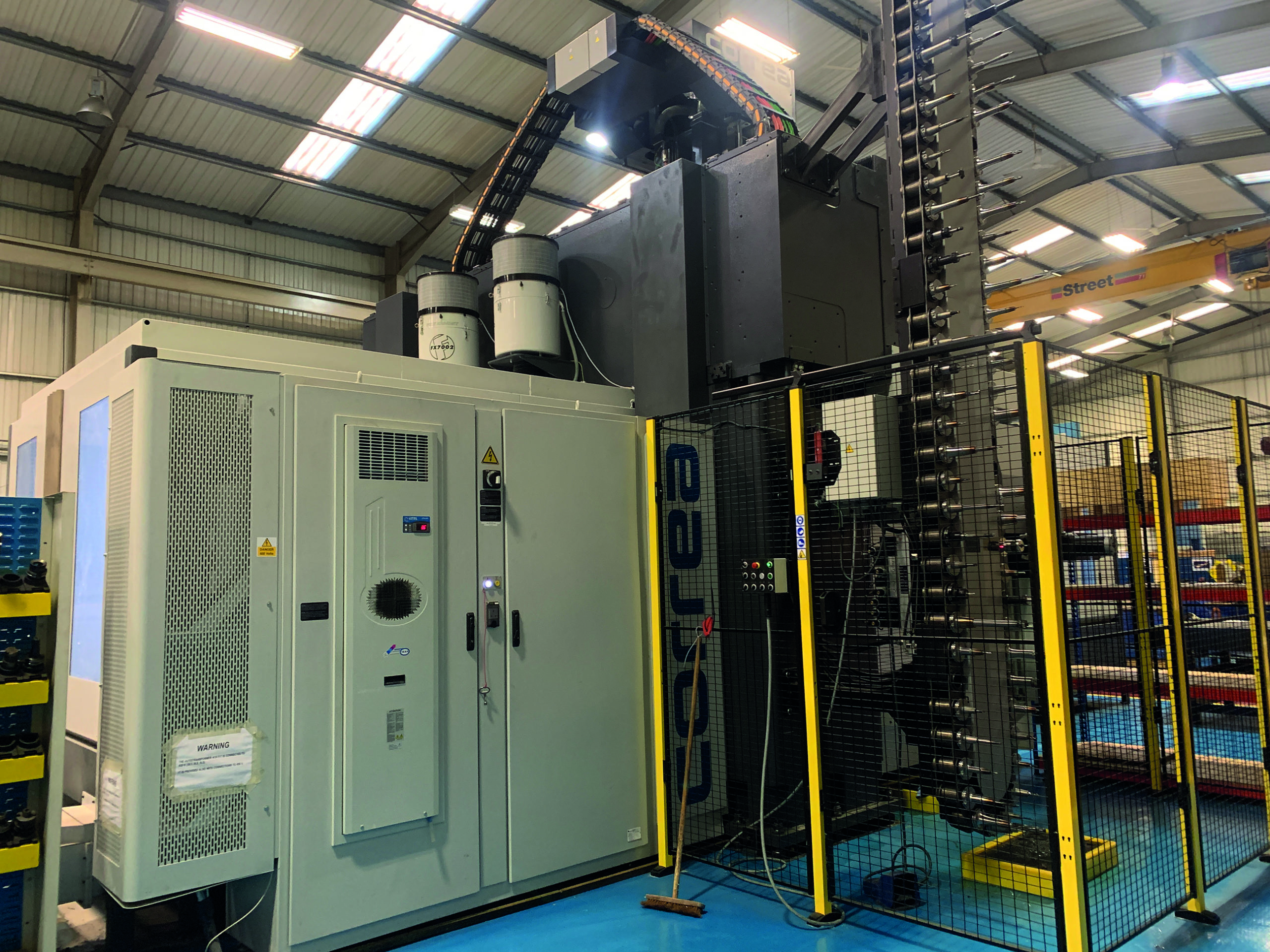
As part of the Hyde Group, Crest Engineering on the outskirts of Manchester is a specialist machine shop with large capacity machine tools for manufacturing critical components for the aerospace industry. One of its latest installations includes a Correa Fox bridge type milling machine from DTS UK, MTD went along to take a look.
As part of the Hyde Group, the Stockport based company is heavily involved in precision machining of aerospace parts, primarily manufacturing engine casings and gearboxes for aircraft. Commenting upon why the company acquired the Correa Fox machine, Gareth Hunt from Crest Engineering says: “We bought the Correa Fox (GNC) machine for a specific component we were looking to machine. The parts need to be machined to a high level of precision and the Correa Fox has thermal compensation throughout the machine area and not just on the spindle, and this was a massive factor in our purchasing decision. In the UK, the climate can change daily, so having a thermally stable machine tool was a crucial factor for us.”
The 3+2 configuration machine also has an ISO BIG Plus 50 spindle taper with a high-torque 6,000rpm spindle, referring to this, Mr Hunt says: “With the components and materials we are machining, we can use the spindle to its full advantage and achieve the best possible surface finishes. With the difficult areas the spindle has to reach into, we can adjust spindle speeds and feeds accordingly to really get the very best finishes on all surfaces of every part.”
Commenting upon the UDX spindle head, its B and C-axis indexing, the 3+2 configuration and the reach of the spindle, Mr Hunt continues: “We are milling lots of angles and features and when you look at the components, you can see all the angles that the spindle is hitting on the part. You really have to look twice to appreciate the angles and surfaces the machine can reach.” From a productivity perspective, Gareth continues: “We have one operator running a couple of machines and we run as smoothly as we can. The machines are highly automated and it just works. It keeps position at all times, it is just brilliant!”
Referring to the capacity of the machine that has an impressive 4m by 3m by 1m in the X, Y and Z-axes, Mr Hunt continues: “The selection of a machine with such a large bed has an element of future-proofing the business, but with the component we are machining on the Correa, we are doing multiple operations on the machine bed. This allows us to have more than one component running on the machine at any given time. We do set the machine up so that we can machine two or three of the same part at any one time with each part being set differently for the subsequent operations. Our operators claim the machine is the best one we have in the factory and I have to absolutely agree with that sentiment.”
With four guideways supporting the ram of the machine, stability and precision are assured. With unsurpassed damping capacity and a water-cooled vertical axis and the BIG Plus spindle configuration, Correa has considered rigidity, stability and performance in every element of the machine.
Concluding upon the relationship and service provided by DTS, Mr Hunt states: “We had already bought a Correanayak M/C 11 Performer machining centre, so we were confident in the service. The way they come across and the fact that we have had dealings in the past; we have found DTS very reliable and if there are ever any issues they will react immediately.”