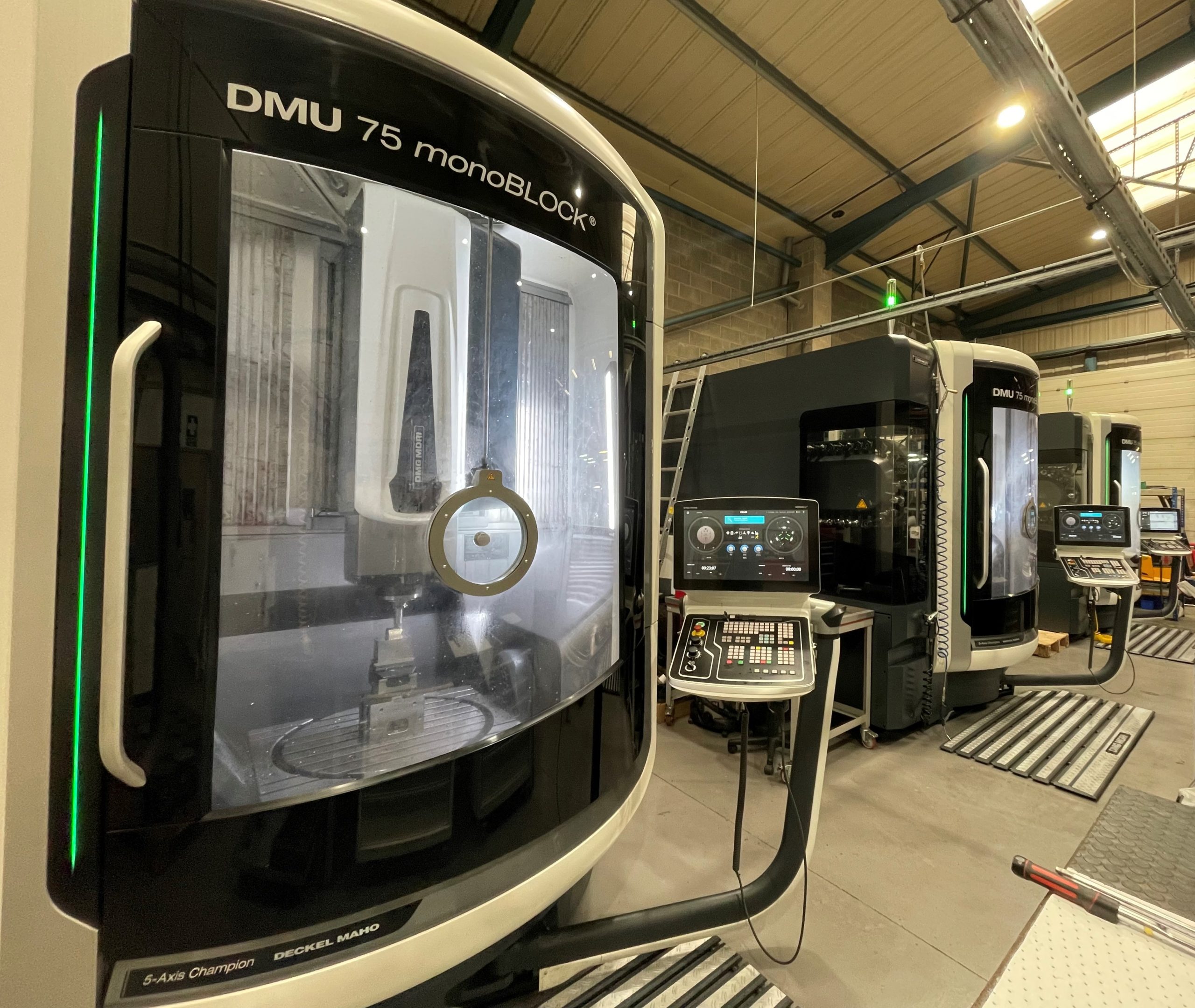
As a company located in Daventry, just a short drive from Silverstone, the JRM Group specialises in design and bespoke manufacturing solutions for the automotive, motorsport, aerospace, marine and medical industries. The company also has a racing division that has progressed through rallying and onto being 2011 FIA GT1 World Champions with the Nissan GT-R. The focus of JRM Racing over more recent years has been in the GT3 endurance competition with the Nissan GT-R GT3. In 2021, JRM Racing was back with the Bentley Continental GT3 fighting for honours in the British GT Championship – behind all of this is a highly advanced manufacturing outfit with a suite of DMG MORI machine tools.
The ISO: 9001 company has the DMG MORI LaserTec 30 SLM additive machine, a CLX450 as well as three DMU 75 monoBLOCK 5-axis machining centres, one of the best-selling machine tools in DMG MORI’s extensive range.
When asked what the company is making on the machines, Mike Sutton from the JRM Group says: “We are currently producing wishbone components for a racing series over in Germany. The parts and materials that we machine vary massively and we are led by the customers’ requirements.”
Looking at why the DMU 75 monoBLOCK has proven such a successful acquisition for machining a diverse range of material types, Mike adds: “The spindle power. The machine has a very robust spindle, and it has a very high torque value. You can actually set the torque value on the machine, so you can input any given value, and this can be adjusted depending on the machine values. In the tool table, you can set the machine to stop if the machine goes over a certain torque value or spindle load.”
Looking at the wishbone components being produced on the machine, Mike continues: “We are currently using a cycle in hyperMILL called arbitrary stock removal and we are currently machining 25Cr 04 steel with a 40mm high feed face mill. The tool is running at an 8m/min feed rate with 0.5mm cuts and 50% of the tool diameter, which is pretty fast. The 0.5mm cut was recommended by the tool manufacturer. The way you machine with high feed cutters is that it takes small depths of cut at high speed. This is different to trochoidal milling where you take larger depths of cut with a smaller radial value.”
Looking at the agility of the machine, Mike continues: “It’s a large machine and we have it running at 80% rapid at the moment and it is feeding at 8m/min – and we could push it further depending on the material, the application and of course the tool capabilities.”
Alluding to the fundamental basics of the DMU 75 monoBLOCK, the machine has exceptional swarf fall away and access to the work area for the operator. As Mike says: “It’s very easy to access the work area and with the curved door, you have very easy access to the worktable once the machine is set at zero. Additionally, the swarf just falls away into the swarf conveyor and this conveyor can be set to come on at various intervals. We have it set so that every four minutes, it comes on for 15 seconds. The machine has quite a large swarf conveyor which will take a while to fill up, so it does not need to be on continuously. The machines are very good, very reliable, very robust and undoubtedly some of the best 5-axis machines that I’ve used in my time.”
The single piece cast machines are extremely stiff and rigid, and this sets the foundation for JRM Engineering to achieve dynamic machining speeds daily. As Mike adds: “You can feel the vibration in the floor, if the machines were not rigid, the vibrations would be going into the base of the machine – but the rigidity of the machines means that sometimes you feel the vibration in the floor.”
Looking closer at the setup on the machines, and in particular, the worktable that offers the ability to clamp large parts whilst also having the rotary table, Mike says: “On one of our machines, we have two parts in a single set up. On another machine, we only have a single component on the table as you need to hit the part from all directions, and you cannot put anything else at the side of it.”
Discussing the CELOS control system on the DMG machines, Mike confirms: “I really like working with this control. It took a little while to get used to, but it is very intuitive, very user-friendly and as long as you know what you’re pressing and when you should be pressing it – it works very well.” Comparing it to CNC systems of years gone by, Mike says: “First and foremost, it has everything that you need to see on the display. There is so much information on the screen that tells you how fast the machine is feeding, the spindle speeds, your positions and how far you have to go, you can also see the programme and it also has gauges where you can see how much power the spindle is using, the torque going through the spindle, the vibration on the spindle – and these can be set to the operator’s preferences. This helps to prolong the life of the spindle bearings and cutting tools. The machine has diagnostic tools and we have used the remote maintenance function where DMG MORI can actually log onto the machine and investigate and resolve issues remotely. You just have to get in touch with them, you are provided with a code that you have to put into the machine – and then they can remotely access and diagnose default problems, it is very good.”