Listen here
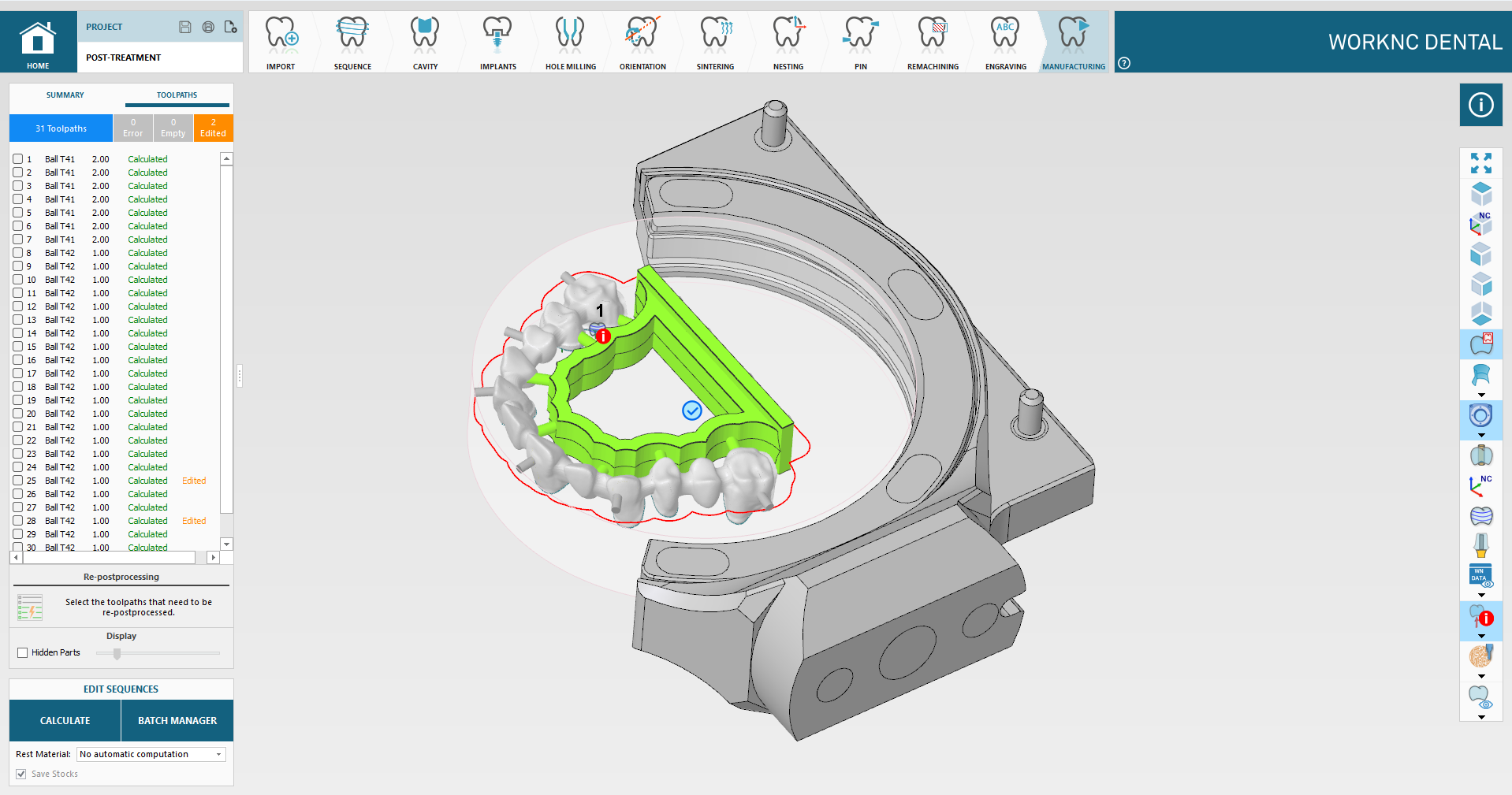
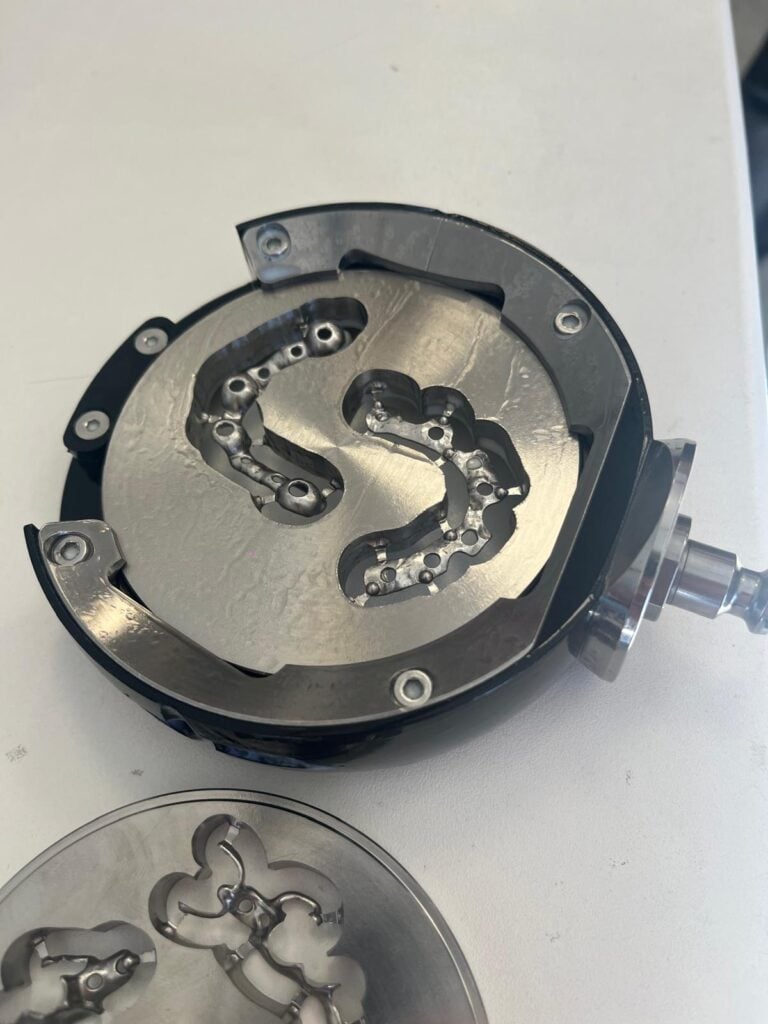
The dental industry has witnessed explosive growth over the last decade. Dentistry has become a lucrative field, with an ageing population retaining their teeth for longer, an increase in sugary foods on supermarket shelves, and a socially media-influenced population pursuing cosmetic enhancements. Over the last ten years, NHS treatments have incrementally increased by 1 to 2% per annum, private dental care by 5 to 7%, and cosmetic dentistry has boomed by as much as 35%. All these factors exert pressure on the supply chain, and itâs here that Quickgrind is making an impact.
By definition, high-street dentists, laboratories, and the supply chain supporting the sector are medical experts, not engineers. Engineering expertise becomes essential as more dentists perform scans, utilise 3D printing, and engage in micromachining at-source or through local laboratories. This is why Anthony Wainwright of Optadent contacted Quickgrind last year.
The company uses a range of small cutting tools and it required a 2-flute ball nose with an extra 5mm of reach. Optadent was compromising its machining strategies, and Anthony believed that processes could be improved with the right solution. Purchasing standard tools via a dental consumable distributor, Optadent, was confident that a better solution was available.
Commenting on the initial meeting with Optadent, Quickgrindâs Technical Support Manager Mark Aspinall says: âDiscussing the dental CNC milling industry with Anthony, it was clear that Quickgrindâs Total Solutions Engineering Strategy (TSE) fitted perfectly with Optadentâs desire to improve processes. This initial meeting sparked Quickgrindâs desire to further investigate the digital dental market to reduce their total costs while optimising efficiency, productivity, and sustainability.â
Understanding the market
Quickgrind has collaborated with digital machining dental lab owners, technicians, machine tool manufacturers, distributors, CAD/CAM developers, CAD/CAM resellers, CNC application engineers, and academics. Discussing this research, Mark adds: âWe have observed firsthand how and where the market is growing, the frustrations the dentistry industry faces regarding its manufacturing practices, and how these challenges impact the speed of market growth, future technologies, and materials. At Quickgrind, we have listened to the industry and support the sector through our advanced cutting technologies.â
Over the past 12 months, Quickgrind has seen the automation and digital workflow within the industry. This encompasses everything from models and materials to CAM programming of toolpaths, loading, tool databases and breakage detection.
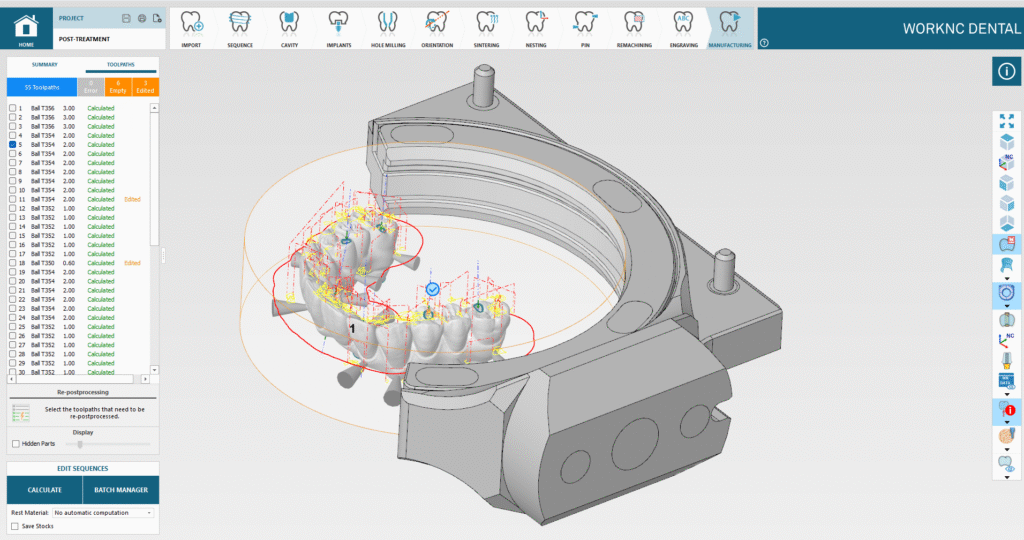
âThe level of automation is impressive, and the manufacturing supply chain in other industries could learn a lot from it. The automation in dental milling laboratories enables them to program and rapidly produce complex dental components to specific quality standards, with minimal manual input. Therefore, cutting tool performance is even more critical for machine uptimes,â Mark says.
âDental labs process a wide variety of materials, ranging from wax to titanium, and comprehending the terminology of the dental world is essential to meet clientsâ requirements. CNC milling strategies, tool databases and âstandardâ cutting tools are typically provided as a package from the distributor of the small and often bespoke machine tools. In many UK laboratories, expertise in cutting tools and machining strategies is often limited to what has been provided by the machine tool distributor.â
âWhile very complex components are machined, the full potential of the CAD/CAM software and the machineâs capabilities is not being utilised to maximise productivity. In this area, our experts are assisting with machining strategies, cutting parameters, and, of course, tools to extend tool life, optimise machine uptime while enhancing the quality of components and implants.â
Quickgrind recognises that the dental industry has been plagued by low-cost and low-quality cutting tools sold by dental consumables and machine tool distributors at inflated prices. Rather than exploiting this industry, Quickgrindâs approach is to collaborate with customers and support them through its Infinite Possibilities program. The Tewkesbury manufacturer has published a cutting tool brochure for the dental industry, with full support available for manufacturers.
In the past 12 months, Quickgrind has worked closely with manufacturers such as Optadent Solutions, Element Digital Solutions, PRO4 DENTAL, Beaumont Ceramics, Radiant Dental Laboratory, and countless others, including Bristol CADCAM and Hexagon.
Commenting on the relationship with Quickgrind, Antony Wainwright, Company Owner at Optadent Solutions, says: âWe were getting frustrated with cutting tool issues when milling titanium and chrome cobalt dental restorations. Typical issues were tool breakage, poor tool life and inadequate reach. By partnering with Quickgrind, we now have a cutting tool supplier whose products have helped us achieve a 40% improvement on tool life, reduced production costs and more stable milling processes.â
âBy utilising Quickgrindâs Infinite PossibilitiesÂź process, we have created our own tooling suite for which we can tailor our milling strategies. This has reduced cycle times significantly with no detrimental effect on quality. Quickgrind has helped us optimise our CNC milling strategies using the latest cutting tool technologies to improve quality, cycle times, and costs. This willingness to collaborate sets them apart from other cutting tool suppliers in the dental market.â
Adding to this testimonial, Dan Barber, Company Owner at Element Digital, says: âQuickgrind doesnât just want to sell us milling tools; they want to work with us to understand our machining requirements, workpiece materials, and quality expectations and to ensure their tools provide improved performance. We have seen huge improvements in tool life and consumable costs using their Zodiac, Gladiator, and Ribcutter ranges across all materials from pre-sintered zirconia to titanium and chrome cobalt.â
We are now interested in applying Quickgrindâs Infinite PossibilitiesÂź methodology for producing non-standard tooling to maximise the capabilities of our CAM systems and CNC milling machines, thereby reducing our cycle times and improving our overall efficiency.
With end mill ranges from the Zodiac, Rib Cutter, and Typhoon to the Orbis, Spectre, and Lynx, along with the infinite possibilities of bespoke solutions, Quickgrind has an engineer and a solution to support the demands of this specialised industry sector. Quickgrindâs Mark Aspinall concludes: âDental laboratory owners are open and willing to collaborate with a desire to learn and utilise their machining capabilities. There are lots of best practices that should be shared between industrial machining and dental labs that would benefit both sectors. The level of automation I have seen in dental milling has genuinely blown me away, and dental labs could benefit more from cutting tool and milling knowledge to utilise the machine capabilities they have. This will help reduce cycle times, improve tool life, minimise downtime, increase capacity, and reduce operational costs.â
Subscribe to the MTDCNC Newsletter
Subscribe to our Newsletter today!
Stay up to date with the latest industry news and events.
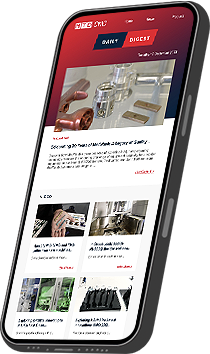
Subscribe to the MTDCNC Newsletter
Dentists know the drill with Quickgrind
0:00 / NaN:NaN