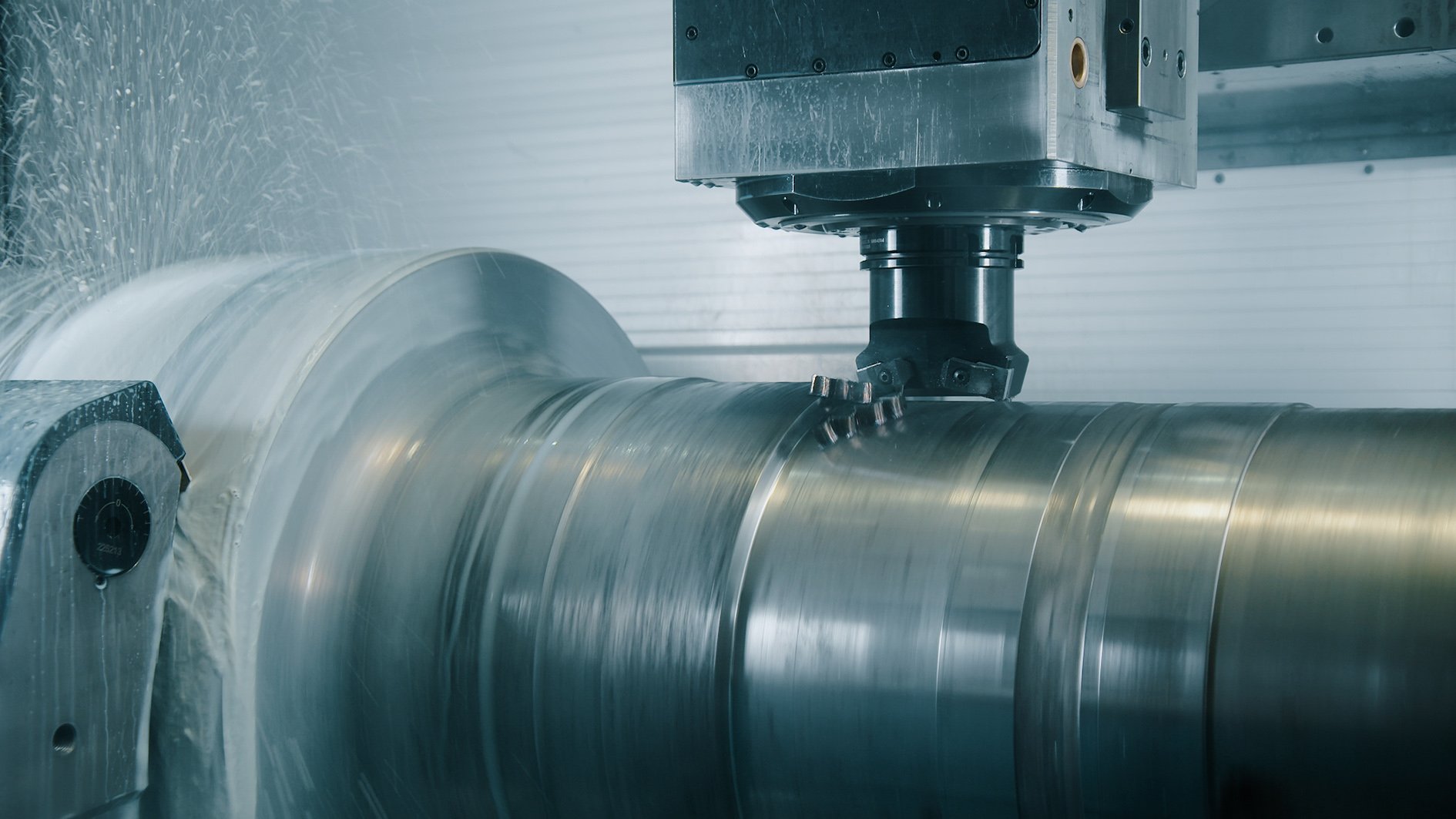
The rampant modernisation in Asia of technology-intensive sectors, such as automotive, aerospace and general engineering, is constantly stretching the local machine tool builders to their limits. This creates opportunities for specialists such as Weingärtner Maschinenbau and its technology partner CERATIZIT to fill the gap between market volumes and local production with high-quality machine tools and turnkey projects. A recent application saw the two companies work together on a project for roll machining.
Austria-based Weingärtner Maschinenbau provides customised complete machining solutions and boasts a wealth of experience in the machining of large parts on its special-purpose machines in Kirchham. “With its vario, pick up, multi-machining and finish machine programmes, Weingärtner offers sector-specific technologies that can be tailored to the requirements of the job in hand,” points out Weingärtner Group Marketing Director Thomas Exenberger.
Collaboration with huge potential
As a complete solution provider for heavy-duty machining, Weingärtner works closely with CERATIZIT. “The expertise of CERATIZIT is expressed not just in the complete tooling programme for the machining of large parts, we also see it in our OEM services, where we provide the structures and skills for the creation of complete machining solutions,” observes Alfred Hofegger, Team Leader for OEM Services at CERATIZIT Austria. “If required, we also define the machining operations, including the associated tooling, specify the cutting data and calculate machining times, make forecasts of unit costs, carry out test machining in the
CERATIZIT Innovation Centre and support machine acceptance and commissioning activities.”
CERATIZIT and Weingärtner’s recent collaboration involved the customer wanting to replace up to four conventional machines for roll production. One of the challenges is the material to be cut, which is produced using the centrifugal casting method that has a hardness of up to 85ShC. The outer shell is 50 to 90mm thick, while the rest of the roll consists of a core material that is much softer with a hardness of between 38 and 45ShC. This mixture of hard roll and soft journal material also required the use of a variety of cutting materials, such as silicon nitride, mixed ceramic, carbide and CBN, all of which are standard in the CERATIZ
IT product portfolio. Machining involved a wide range of machining operations, such as turning, grooving, milling,drilling, deep-hole drilling and thread cutting.
The non-homogeneous nature of the material, the machining times, service life and high degree of process security are clearly the decisive factors as far as the machining is concerned. Against this background, CERATIZIT assembled a tooling package that includes turning, grooving and milling tools as well as systems for drilling, thread milling and tapping – with all the tools coming from the flagship brands Cutting Solutions by CERATIZIT, KOMET, WNT and KLENK.
The cutting inserts LNMR 50, SCMT 38 and SN 25, with cutting lengths of 50mm, 38mm and 25mm respectively, are available for users involved in heavy-duty turning. For grooving, the HX system with groove widths of between 16 and 60mm is used. Among the areas that require milling are key faces and bore radii. “For these applications we use tools from the AHDM series for heavy-duty cutting and AHFC for high-feed cutting, as well as the MaxiMill A271 face miller and special radius milling cutters,” reports Peter Stebele, Process Manager for Heavy-Duty Machining at CERATIZIT Austria. The MaxiMill high-feed milling cutter (HFC) is a key tool in this area due to its excellent productivity. Fitted with ten inserts, this cutter offers extremely high feed rates per tooth with shallow cutting depths to achieve a high level of productivity. And because of these shallow cutting depths, the roughing operations performed by the HFC milling cutter give the optimum preconditions for the finishing of transition radii on key faces. For the finishing of key faces CERATIZIT employs its VHM end mills and CBN-equipped finish milling cutters. When it comes to drilling CERATIZIT can produce diameters up to 155 mm and depths up to 60XD, with the range split between its MaxiDrill MD900 indexable insert drills, which are used across the entire range of diameters from 12 to 63mm, and solid carbide tools for smaller holes.
With the initial turnkey package accepted by the customer, the machines will now be dismantled and shipped to their destination, where the customer will install them before carrying out the final acceptance trials. Specialists from Weingärtner and CERATIZIT will be in attendance as both companies agree that a comprehensive, machining-oriented and professional service offering is vital.