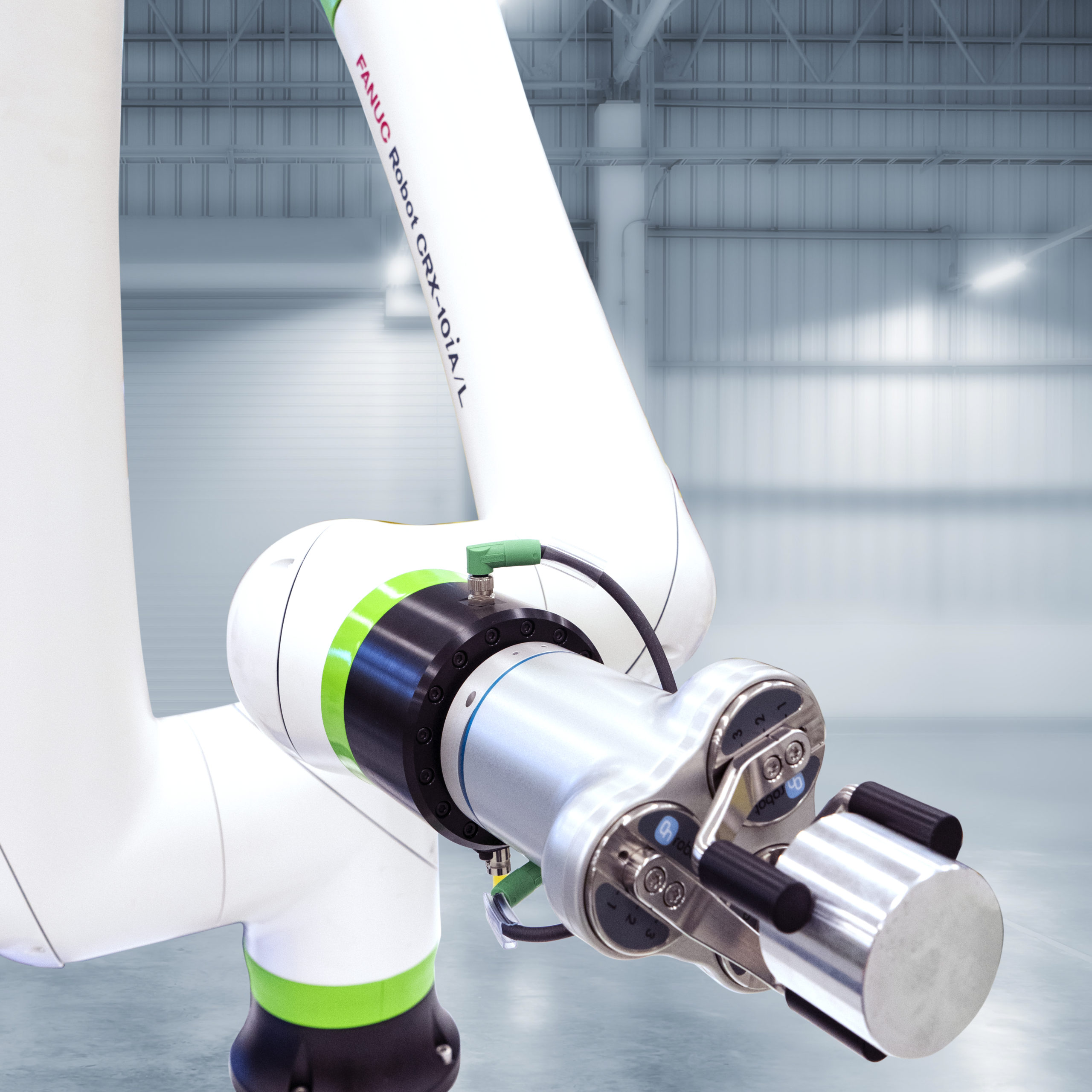
Paul Richards, Global Customer Coordinator Europe, Cobot Market, FANUC Europe
When the International Federation of Robots (IFR) first started collating collaborative robot data in 2017, this new breed of robot had a market share of just 2.8%. The IFR’s latest report showed that by 2021, that figure had leapt to 7.5%, with the number of newly deployed collaborative robots growing by 50% year-on-year to 38,966 units globally.
Cobots are gaining popularity for several reasons. Firstly, they provide a solution to many challenges that manufacturers are facing. In terms of flexibility, the cobot sits between an industrial robot and a human. This agility is valuable for accommodating shorter product lifecycles and the high mix and low volume approach to manufacturing.
As demand for cobots has soared, the number of players in the market has proliferated and there are now over 60 cobot manufacturers worldwide. Whilst more competition can mean greater choice and better value for customers, it can also mean more confusion. This is particularly salient when you consider that cobot sales in the UK are being driven by SMEs, who seldom have the in-house resources and expertise to thoroughly assess numerous different makes and models. To aid the decision-making process, FANUC has compiled a checklist to help first-time buyers navigate the complexities.
1. Establish the business case
Determine whether your operation would benefit from a cobot. Start by identifying the pain points hindering growth. If staff reliability, RSI, health & safety, a lack of labour, or the limitations of hard automation are on your list – cobots are a route worth exploring.
2. Identify potential applications
The next step is to identify the applications associated with these pain points. What are the tasks that are causing RSI? Which tasks don’t humans want to do?
3. Evaluate the applications
Score each application based on the following considerations: Is it a precision task? Are there uncomfortable motions involved? Does it result in high rejection rates? Does it involve heavy loads? Is a constant human presence needed? Does the human operator add any value? What speed does the task need to be performed?
4. Cover off safety concerns
Assess safety. Does the cobot need to be guarded or part-guarded? Part guarding or other safety devices can be employed to enable cobots to work alongside humans at higher speeds. However, if the application requires full guarding, making it less flexible and adding to the cost, a cobot may not be the right solution.
5. Protect your investment
The IFR considers the average lifespan of a robot to be 12 years. To protect your investment, buy from a brand that is still going to be around in 13, 14, 15 or more years. Ask potential suppliers for the predicted life of their cobot.
6. Calculate payload
and reach
Do not go too low on the payload. Don’t assume that if a cobot has a payload of 5kg it can lift an item weighing 5kg. To work out your payload requirement, calculate the total load on the end of the arm (part + gripper + fingers etc) whilst taking into account offset payload and inertia. When calculating reach, bear in mind that working at full reach limits the cobot’s movement in the robot’s wrist, so build in additional margin.
7. Select sensors and ancillary equipment
If your application requires 2D or 3D vision, consider where you want the camera (remotely or on the cobot). If the cobot will always pick from the same area, a camera is best mounted over the pick area.
8. Evaluate your environment
If you want a cobot in a food production environment, you will need to think about IP rating and washdown protection. If the cobot is intended for use in a dusty or dirty environment, you will also need a high protection rating (IP67 or above). When enquiring about IP ratings, make sure that they apply to the entire unit (including the controls), not just the arm.
9. Consider connectivity
Does the cobot need to communicate with other equipment, such as CNC machines, part feeding systems, grippers or vision systems? If so, specifying your cobot with the same communication protocol as peripheral equipment will save cost and integration time.
10. Plan for the future
Finally, think about how flexible the cobot is for meeting your future needs. Will it be able to accommodate new applications and growth? Does it have software that can be updated and supported? As well as driving productivity, a positive experience will pave the way for further automation of more profitable applications and inspire employees as you continue on your automation journey.