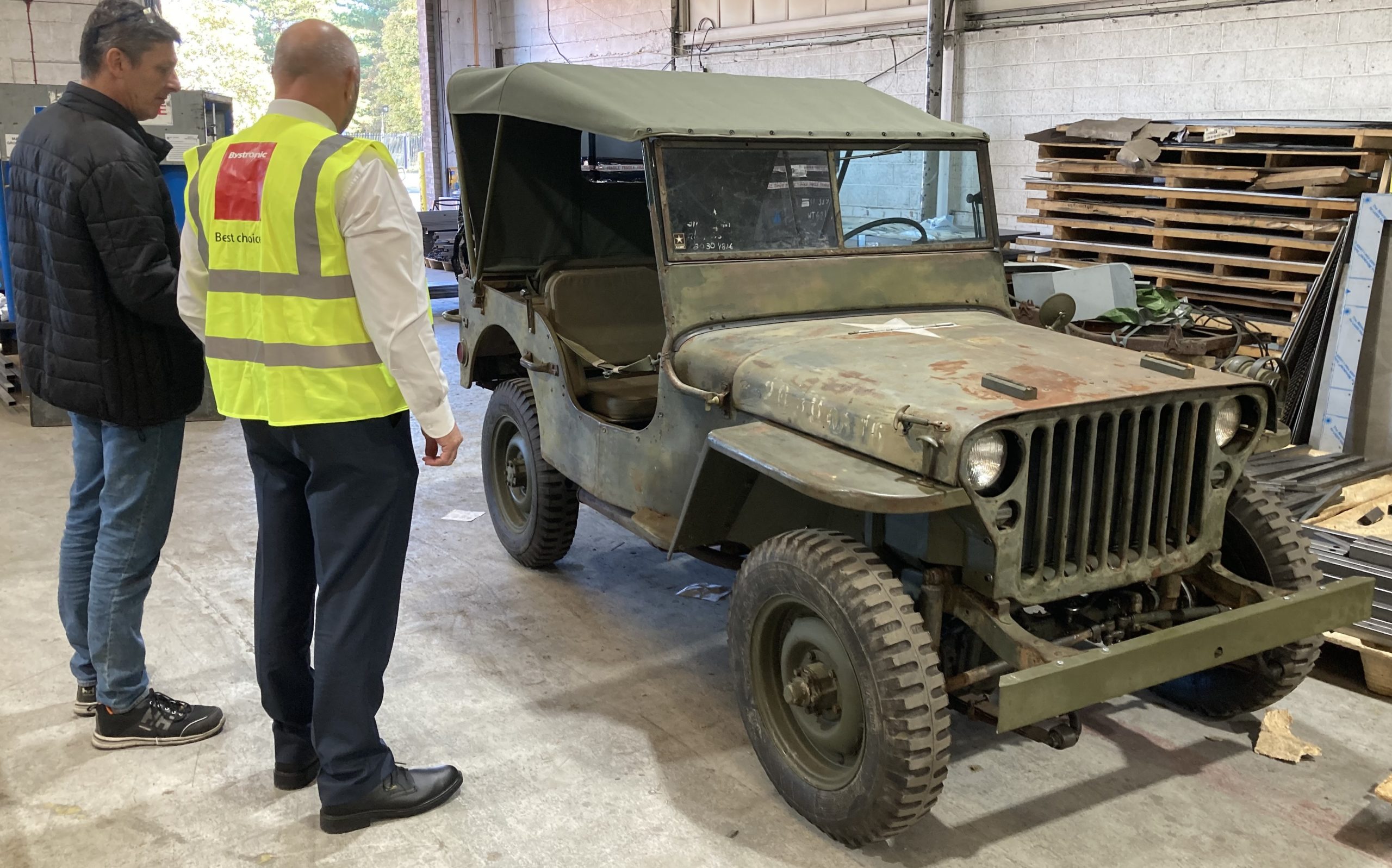
Since its late 1990s inception, Crown Manufacturing has evolved to become a business with a presence on two locations with a team of over 60 staff. Bystronic has travelled this journey with Crown Manufacturing almost from the start.
As a provider of sheet metal and general metal fabrication products and services, the journey for Weston-Super-Mare manufacturer started when an engineer took a passion for Italian Lambretta scooters and took it to a multi-million-pound company. The company evolved from the production of scooter components to ‘fit outs’ for the retail industry.
Paul Read from Crown Manufacturing says: “We started in the late 1990s manufacturing Lambretta parts, which was a hobby and passion of our MD Dean Harvey. It evolved into a business. Now, we manufacture for the retail industry, producing all the fixtures and fittings that are going into a store. We process sheet metal work that is flat, we have to laser cut, fold and bend it; and in some instances, parts move from folding to our welding area for fabrication work or our paint shop for finishing and subsequent assembly.”
Crown Manufacturing has invested heavily in both its staff and technology. As Paul continues: “We found that being dependent on third-party suppliers wasn’t going to enable us to react in every area, to service our customers. So, over the years we have invested to try and bring all the services in-house. Our investment in the last year has been useful to close off that dependency on third-party manufacturers. Another passion of our business is the Ford Willys Jeep, and we now have a website www.joesmotorpool.com that is all about the refurbishment and restoration of Ford Willys Jeeps.”
The ongoing investment strategy has seen Crown Manufacturing invest in fiber laser cutting for both sheet and tube materials as well as investment in bending and forming equipment.
Like a Pheonix from the flames
A disaster struck the business in 2018 when a fire caught hold of the paint department, creating catastrophic damage. Recalling this, Paul says: “We had a fire that would ruin most companies, a malfunction in our paint shop. One of the benefits of having great relationships with our clients was that they knew we were committed to them as a manufacturer. So, even with the disaster of the fire and having to reduce our staff after losing 50% of our factory – they could see that we were determined to deliver on our promises.”
Looking at the relationship with Bystronic, Paul says: “Sheet metalwork was always historically done in the 2D world because it comes in flat, and we form it. By bringing this into the 3D world, we have evolved nicely and the fire was the catalyst that brought that to light along with the new machines that we have invested in since that period – as 3D now exists on the machines as well. We can now create 3D models and send them through to the machines. The transfer straight from PC to the machine is now a reality and something that Bystronic has supported us with.”
Since the fire, Crown Manufacturing has invested in 3 machines from Bystronic, and the plant list now includes the Fiber Laser with automation that can load up to 6 tonnes of steel, an Xpert Pro100t 3m, 3 Xact Smart 100t 3m machines and an Xpert 40. This high-end plant list is complemented by CAD/CAM systems such as Autodesk Inventor; Radan, Alphacam and Bystronic’s Bysoft suite that enables Crown to seamlessly take customers through from concept and design to finished product.
The latest acquisition that arrived in 2022 was the Bystronic ByTube 130. This machine features a fully automatic setup, bundle loading, 6-axis control and high-speed and precision cutting that allows Crown Manufacturing to take on and efficiently complete high-quantity orders to a very high standard. Alluding to this, Paul says: “Our latest investment is the tube laser. This takes away the dependency upon a third-party supplier that we did end up struggling with. Integrating the ByTube 130 into Crown’s arsenal of machinery has been revolutionary, as it removes bottlenecks in the manufacturing process by allowing us to schedule and prioritise tube laser work in-line with due dates and urgency.”