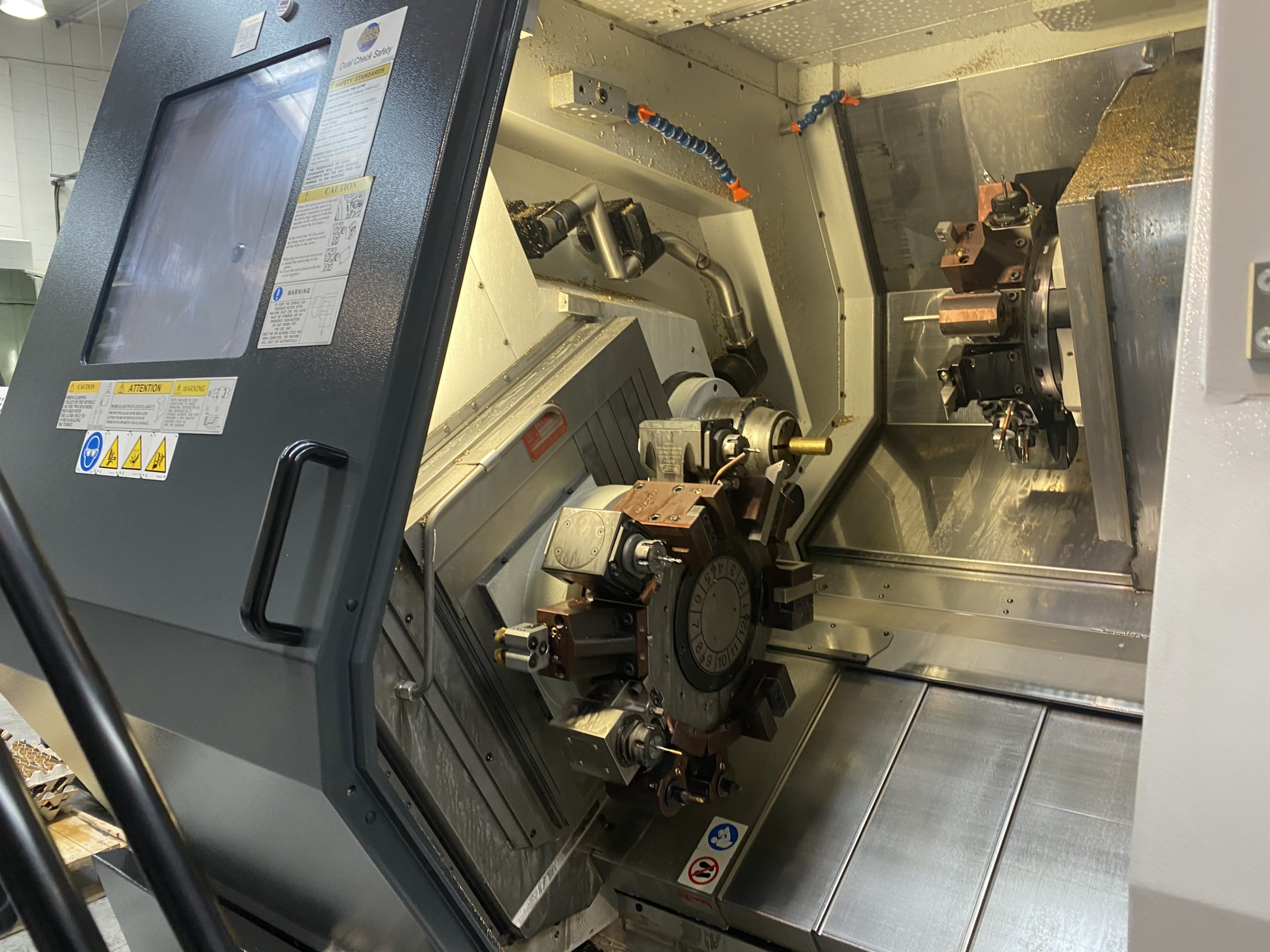
Ashby Precision Engineering Ltd in Abingdon has invested more than £1 million in the last year in new machine tools. Part of this investment has included a twin spindle, twin turret Biglia B465 T2Y2 turning centre from Whitehouse Machine Tools – MTDCNC visited the Oxfordshire company to find out more.
The subcontract manufacturer supplies machined components to the medical, scientific, cryogenics and pharmaceutical industries as well as the motorsport, valve and instrumentation, academic and research sectors. So, when the company specified the new Biglia machine, one key feature that really attracted Ashby Engineering was the fact that the Biglia B465 T2Y2 turning centre has an offset capability on the second spindle. This means the machine is far more flexible, providing the potential to have three tools operating simultaneously. Another key factor was the part ejection system whereby the remnant goes out of the back of the machine and the finished parts are ejected safely and securely, ensuring exceptional quality and consistency.
Giving MTDCNC a run-through of the machine, Ashby Engineering’s Paul West says: “The machine we have has a 65mm bar capacity and it also has a twin Y-axis facility that provides +40 -50mm on both the upper and lower turrets and both turrets have high-pressure coolant facility. The machine also has a B-axis that helps with clearance. This second spindle has 115mm offset function that not only provides clearance but also enables superimposition machining so three tools can be cutting on the two turrets.”
The reason Ashby purchased the machine was that it wanted to undertake a lot of lights out machining. Alluding to this, Mr West says: “What this gives us is the fact the lower turret doesn’t have to travel quite as far to start machining the components. Additionally, it’s quite a compact envelope, so the tools don’t have to travel quite as far, and this improves productivity.”
Referring to the parts coming off the machine, Mr West says: “A lot of the parts are brass, so we don’t want them to be damaged. So, we thought the part catching system on this machine was right up our street. The part catcher is located behind the sub-spindle and when a part is complete, a door will open, and the part catcher will come forward to a midpoint between the two turrets. It will then open the chuck and push the part out with a pneumatic ejector into the catcher, whilst it is washing the part at the same time. The part catcher will then swing back up behind the sub-spindle and drop the part onto a conveyor. The conveyor will move the parts out of the machine. To accumulate the parts during long unmanned periods, we have also invested in a Rota-Rack system. This system with the Biglia is one of the key reasons we selected the machine.”
With the machine acquired for batch and production work, Mr West says: “The machine is already running over 100 hours a week, and this is likely to increase. Whilst cycle time is important, it is not the critical factor in our production. It’s the quality of the parts coming off the machine.”
Picking out some key elements of the Biglia B465 T2Y2 turning centre, Mr West says: “One thing I like is the way the machine washes out the collet. It uses high-pressure coolant, and you can even use air – when you are running a lot of brass, this is quite an important factor. We also like the fact that you can measure tools in-cycle, it just drops the measuring arm over to the tool whilst the machine is in cycle. With regards to programming, sometimes it is down to the operator to program the machine on the shop floor but for other components we do use a CAM system in the office and download the program to the machine.”
Discussing the two Y-axes on the machine, Mr West concludes: “This system is a lot easier to use when you are not governed by a single turret. It means we can think a little bit more ‘out of the box’ when it comes to machining the parts. It makes the machining process far more flexible.”