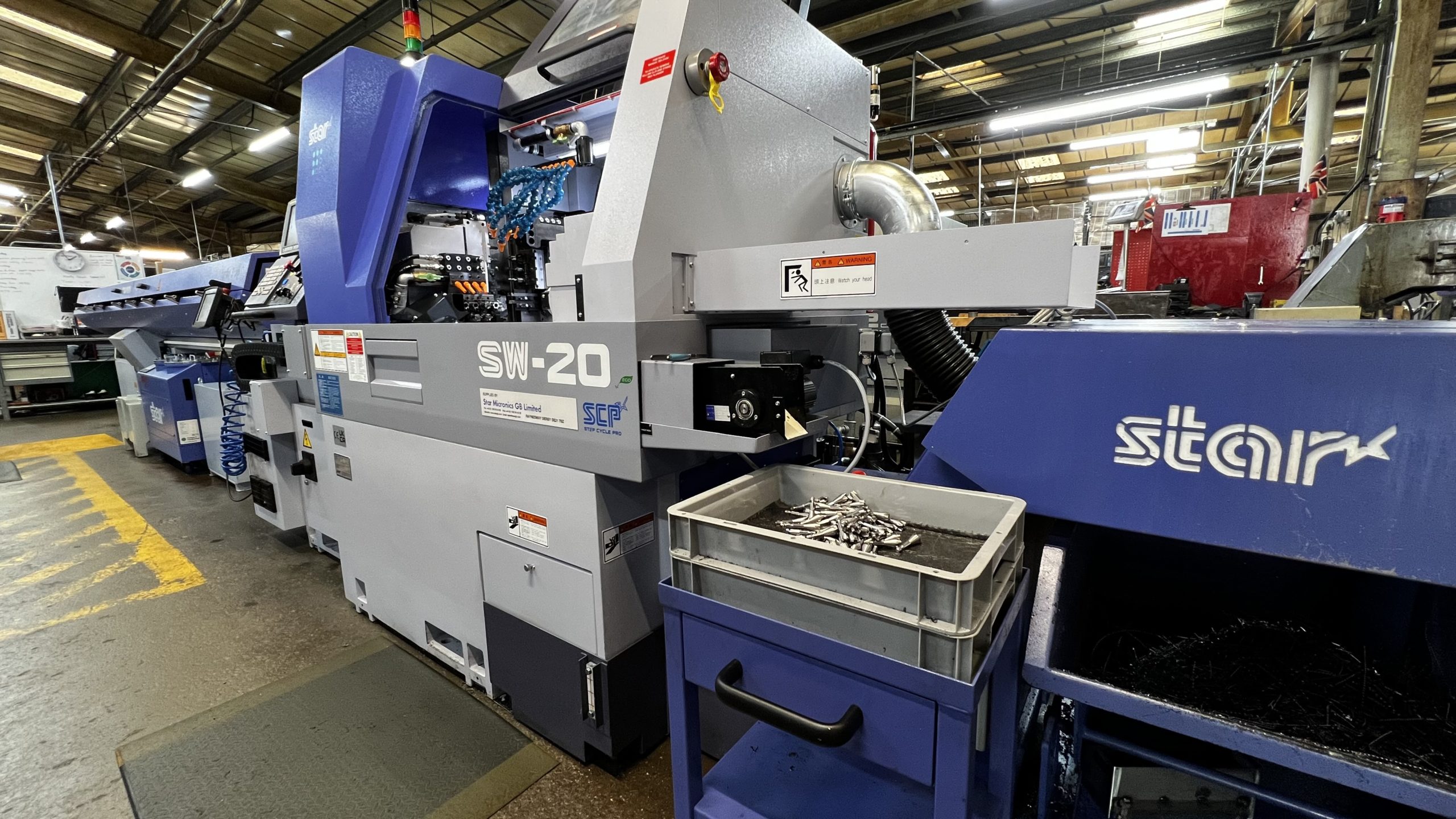
As a brand, Armeg power drilling tools are stocked on shelves in hardware stores and retail outlets the world over. With a product range that encompasses everything from masonry, wood, metal and tile drills to hand and power tools, saw blades, screwdriving products and more, Armeg has been designing and manufacturing products since 1973.
With over 600 products in its armoury, Armeg is utilising sliding head turning centres from Star to enhance its throughput. Looking at one specific product that has given the company manufacturing issues for several years, Armeg’s Paul Bentley says: “The product is very challenging to make and we used to produce it in three operations that included turning, then shanking it, and we had issues getting it off the machine. It was costly and a challenge to serve our customers, and we pride ourselves on price, quality and service. We can now produce the party in one operation.”
“We have also just launched a roofing bolt driver and if it wasn’t for the Star machines, we wouldn’t have been able to get that part to the market. It is a price-sensitive product and the cycle times and technologies on the machine have enabled us to get that roofing bolt driver to market.”
Looking at how investment in a Star SR and two Star SW machines has brought business to Armeg, Andrew Grafton from Armeg says: “If I am trying to secure new business and we come back to the factory and we cannot physically manufacture it, that can be down to simple manufacturing capabilities we cannot accomplish. It could be that we cannot manufacture the parts cost-effectively, or we may simply not have the capacity.”
Discussing the process of buying sliding head turning centres from Star, Andrew says: “We originally invested in a Star SR machine which we got for a certain product. It was fantastic. We realised how versatile the machine was and we were loading it with new products all the time, but we quickly discovered that capacity was filling up on the SR machine. We needed to relieve capacity and we discovered that the Star SW-20 machine was a lot better suited to some of our new products and the geometries of those parts.”
Alluding to this, Andrew says: “The SR machine is very versatile and will let us go up to physically larger components to 38mm diameter and on the smaller components, it is like a jack of all trades. We need to churn the products out at a much higher rate and the SW-20 machines allow us to do that. They have more axes and more capabilities. The machines have three-channel programming and machining that essentially allows us to have three different cuts on the material simultaneously. So, on a standard sliding head lathe your cycle time may be five minutes, but with the SW-20 you can reduce that by two-thirds by having three cutting tools working simultaneously.”
The company initially bought one SR machine and within a year, it bought a second machine. Mentioning this, Andrew continues: “We went for the SR machine originally, which was fantastic but with new product lines – the SW machine was better suited to our parts. There was one product we took on only because we had the SR machine – and we managed to produce it in three minutes. The SW machine sliced that cycle time in half, but as we released more products and need more capacity, we needed to buy another SW machine.”
The company also utilises the Step Cycle Pro (SCP) feature on its Star machines, as Andrew adds: “We are now starting to run low on capacity on the new machine, so we had to go for SCP. This swarf control system works via oscillation to control the length of the chips. The main problem running these machines lights out is swarf control, so the operator may set the machine and an hour after he has gone home, the machine stops due to swarf issues. We have worked out that over our vast array of components, SCP actually increases our capacity by five hours every single night of the week. This is extra capacity that will help us to grow our business.”